Your cart is currently empty!
SayPro Vendor and Supplier Coordination: Ensuring Timely Production and Adherence to Quality Standards.
SayPro is a Global Solutions Provider working with Individuals, Governments, Corporate Businesses, Municipalities, International Institutions. SayPro works across various Industries, Sectors providing wide range of solutions.
Email: info@saypro.online Call/WhatsApp: Use Chat Button 👇
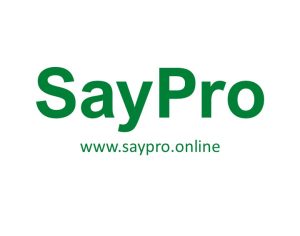
Overview: Effective vendor and supplier coordination is critical to ensuring that SayPro’s merchandise is produced both on time and to the required quality standards. By carefully managing relationships with suppliers and maintaining consistent communication, SayPro can mitigate production delays, ensure products meet the desired specifications, and manage any quality issues that arise. This process involves establishing clear expectations, maintaining active oversight, and ensuring that all parties are aligned toward delivering high-quality merchandise that meets event timelines.
1. Establishing Clear Production Timelines:
Setting Realistic Production Schedules: One of the first steps in vendor coordination is to set clear, achievable production timelines. This involves understanding the full scope of the production process from design approval to final delivery, and then establishing milestones that align with event schedules.
- Initial Planning Stage:
- Design Approval Timeline: Once the merchandise designs are finalized, say within 1–2 weeks, it is crucial to allow ample time for the vendor to review the designs and approve the prototypes or samples. Delays at this stage should be identified and communicated early to avoid further setbacks.
- Production Start: After the sample approval, the actual production phase begins. SayPro will negotiate a start date with the supplier and set check-in dates to ensure that the vendor stays on schedule.
- Production Milestones:
- Material Procurement: Vendors need to confirm that the raw materials for the merchandise (e.g., fabric, ink, packaging materials) are sourced and available for production. SayPro will need to verify that these materials are on hand or are being ordered well in advance to avoid delays.
- Manufacturing Phases: The production process will likely have several phases (e.g., cutting, sewing, printing, assembly). SayPro will monitor the completion of each phase and set deadlines for interim quality checks to ensure everything is on track.
- Final Production and Packaging: A final milestone would be the packaging and final inspection stages. These should be completed with adequate buffer time for any potential last-minute adjustments or quality issues.
- Shipping and Delivery:
- Shipping Timeframes: It’s important to establish clear timelines for when the products will be shipped and when they are expected to arrive. SayPro will need to negotiate with the supplier for expedited shipping if the timeline tightens due to unexpected delays.
- Shipping Method: Deciding on the best shipping method (e.g., air freight for faster delivery or sea freight for larger volumes) and ensuring that it aligns with the event’s deadlines.
Buffer Time for Unexpected Delays: SayPro should work with suppliers to build in buffer time for potential production delays, such as raw material shortages, machine failures, or weather-related shipping disruptions. It’s critical to set a contingency plan in case the original timeline cannot be met.
2. Ensuring Product Quality Standards:
Establishing Quality Expectations Early: SayPro will clearly define the quality standards expected for the merchandise, ensuring that suppliers understand the importance of maintaining a consistent, high-quality product. These standards will cover various aspects, including:
- Material Quality: Ensure that the materials used in the merchandise (e.g., fabrics, inks, plastic, metals) meet specific durability and sustainability standards. SayPro may require certifications (e.g., organic, eco-friendly) for certain items.
- Design Consistency: Ensure that the designs are faithfully reproduced with accurate colors, text, and logos. If there are any custom printing or embroidery details, these need to be verified and consistently applied across all items.
- Durability: The products should meet certain durability standards. For example, apparel should withstand regular washing without fading, and accessories should not show signs of wear after minimal use.
- Safety Standards: Ensure that the products comply with any relevant safety regulations (e.g., non-toxic materials, fire resistance) based on the type of merchandise. This is especially crucial if the products will be used by children or the general public in an event setting.
Inspection and Quality Control (QC): SayPro will work closely with the vendor to develop and implement quality control procedures at various stages of production:
- Pre-Production Samples: Vendors should submit samples for review before beginning full-scale production. These samples should be evaluated for design, material quality, and overall appearance. Once approved, SayPro can confirm that the final batch will meet the necessary standards.
- In-Process Inspections: During production, SayPro can implement in-process quality checks, either through direct oversight or by engaging a third-party QC service. These checks will focus on:
- Ensuring that the correct materials and designs are being used.
- Verifying that production techniques (e.g., printing, stitching) are applied consistently.
- Post-Production Inspections: Once the production run is completed, a final inspection of the products will ensure that they meet SayPro’s standards. This inspection should assess the overall finish, packaging, and any special features (e.g., custom labeling).
Third-Party Quality Control Services: If necessary, SayPro can also employ third-party inspection services to conduct checks at the vendor’s facility. This ensures that the vendor maintains objectivity in the inspection process and adheres to the required standards.
3. Vendor Communication and Accountability:
Regular Updates and Communication: Effective communication is key to staying on top of production timelines and quality standards. SayPro will establish a regular communication protocol with the vendor to receive timely updates on the production progress:
- Weekly or Bi-Weekly Check-ins: Regular meetings or email updates will be scheduled to discuss the status of the production, address any potential issues, and ensure timelines are being adhered to.
- Reporting Tools: SayPro may use shared project management tools (e.g., Trello, Asana) or spreadsheets to track production milestones, document quality inspections, and review progress. These tools allow for transparency and real-time updates for all stakeholders.
Point of Contact: SayPro will designate a single point of contact for each vendor, ensuring that communication is streamlined and efficient. This person will be responsible for coordinating production schedules, inspections, and any quality-related concerns.
Addressing Issues Early: Should any issues arise during production (e.g., material shortages, design inconsistencies, or machine breakdowns), it’s crucial to address them as soon as possible. SayPro will ensure that the vendor is held accountable for any delays and that mitigation strategies (e.g., finding alternative suppliers or materials) are in place.
4. Final Delivery and Follow-Up:
Delivery Management: SayPro will manage the final delivery logistics to ensure the products arrive on time:
- Confirming Shipment Dates: The vendor should confirm the expected shipment date and provide tracking information for all shipments. SayPro will monitor these deliveries closely to ensure they are arriving according to the agreed-upon schedule.
- Inspection Upon Arrival: Upon receipt of the merchandise, SayPro will conduct an inspection to verify that all items meet the required standards. Any discrepancies (e.g., damaged goods or incorrect orders) should be immediately reported to the vendor for resolution.
Post-Delivery Evaluation: Once the merchandise is delivered, SayPro will assess the overall success of the vendor relationship:
- Performance Review: This review will evaluate how well the vendor met production deadlines, quality standards, and communication expectations.
- Feedback to Vendor: Constructive feedback will be provided to the vendor to encourage future improvements, particularly in areas such as delivery times, product quality, and customer service.
Establishing Long-Term Relationships: Maintaining good relationships with reliable vendors is important for future events. SayPro will seek to establish long-term partnerships with vendors who consistently meet deadlines and quality standards, potentially negotiating better pricing and terms for future merchandise orders.
Conclusion:
Effective vendor and supplier coordination is a cornerstone of ensuring that SayPro’s merchandise is delivered on time and to the required quality standards. By setting clear production timelines, establishing rigorous quality control processes, maintaining open and transparent communication, and carefully managing logistics, SayPro can ensure a successful merchandise program for its events. Strong relationships with suppliers will also lay the foundation for future success, with high-quality products consistently delivered to meet SayPro’s brand and audience expectations.
Leave a Reply