Your cart is currently empty!
SayPro Understanding Plastic Manufacturing Machines
SayPro is a Global Solutions Provider working with Individuals, Governments, Corporate Businesses, Municipalities, International Institutions. SayPro works across various Industries, Sectors providing wide range of solutions.
Email: info@saypro.online Call/WhatsApp: Use Chat Button ๐
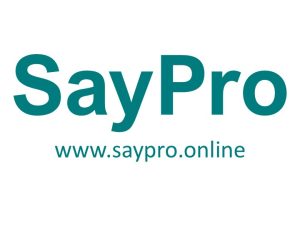
SayPro: Understanding Plastic Manufacturing Machines
Plastic chair manufacturing involves several specialized machines that are key to producing high-quality, durable products efficiently. These machines utilize various molding and shaping techniques to transform raw materials into finished plastic chairs. In this section, we will provide an in-depth explanation of the three main machines used in plastic chair manufacturing: injection molding machines, blow molding machines, and extrusion machines.
Each of these machines serves a specific function and has its own advantages and applications in the manufacturing process of plastic chairs.
1. Injection Molding Machines
Overview: Injection molding is one of the most common and versatile methods for producing plastic components, including plastic chairs. In this process, plastic pellets or granules are heated and then injected into a mold under high pressure to form the desired shape.
Key Components:
- Hopper: A container where plastic granules are stored before being fed into the machine.
- Barrel and Screw: The screw inside the barrel melts and pushes the plastic material through the nozzle into the mold.
- Mold: A metal cavity where the melted plastic is injected and cooled to form the shape of the chair part (e.g., backrest, seat).
- Clamping Unit: Holds the mold in place during the injection process.
How It Works:
- Plastic pellets are loaded into the hopper, where they are heated by the barrel to become molten.
- The molten plastic is then injected into a precisely designed mold under high pressure.
- The mold cools and solidifies the plastic into the shape of the chair part.
- The mold is then opened, and the finished part is ejected.
Applications in Chair Manufacturing:
- Injection molding machines are widely used for producing intricate chair parts, such as armrests, backrests, and legs.
- The method allows for high precision and consistency, producing parts with excellent dimensional accuracy and surface finishes.
- It’s also ideal for manufacturing large quantities of identical parts efficiently.
Advantages:
- High precision and repeatability.
- Complex shapes can be achieved, including hollow designs and intricate details.
- Fast production speeds, especially for large volumes.
2. Blow Molding Machines
Overview: Blow molding is another widely used manufacturing process for creating plastic chair components, particularly for parts that need to be hollow, such as the seat of a plastic chair. This method is ideal for producing lightweight, durable, and ergonomic plastic seating solutions.
Key Components:
- Extruder: Used to heat and shape the plastic into a tube, known as the parison.
- Mold: A cavity in which the parison is inflated to take its final shape.
- Blow Pin: The tool used to inflate the parison by blowing air into it to mold the plastic into the shape of the chair.
How It Works:
- Plastic is fed into the extruder, where it is heated and formed into a hollow tube (the parison).
- The parison is then clamped into a mold that matches the shape of the chair seat (or other parts).
- Air is blown into the parison, inflating it and forcing it to conform to the moldโs shape.
- The plastic is cooled and solidified, and the mold is opened to release the finished component.
Applications in Chair Manufacturing:
- Blow molding is used primarily for creating hollow chair parts such as the seat, backrest, or bases.
- The process is ideal for lightweight designs while maintaining the strength and durability of the chair.
- It can be used to create ergonomic designs with a smooth, seamless finish.
Advantages:
- Efficient for producing hollow and large parts with a uniform wall thickness.
- Suitable for lightweight designs.
- High production speed with low material waste.
3. Extrusion Machines
Overview: Extrusion is a continuous manufacturing process used to shape plastic materials into long profiles, which can then be cut to specific lengths or used in further assembly. In the context of plastic chair manufacturing, extrusion is often used to create plastic parts like chair legs, supports, or frames.
Key Components:
- Extruder: A machine that melts the plastic and forces it through a die to create a continuous profile.
- Die: A mold that determines the shape of the extruded plastic profile (e.g., round, square, or custom shapes).
- Cooling System: The extruded material is cooled and hardened as it exits the die.
- Cutter: The extruded material is cut into specific lengths or shapes as needed for assembly.
How It Works:
- Plastic pellets or granules are loaded into the extruder and heated until they become a molten state.
- The molten plastic is forced through a die that shapes it into the desired profile.
- The extruded plastic is cooled, either by air or water, to solidify the shape.
- The cooled extrusions are then cut to the required lengths or processed further.
Applications in Chair Manufacturing:
- Extrusion is commonly used to produce long chair components, such as the frames, legs, or crossbars that provide structural support for the chair.
- The process is ideal for creating uniform, straight profiles that can be used in various chair designs.
Advantages:
- Ideal for continuous production of long, straight components.
- Cost-effective for large-scale production runs.
- Allows for flexibility in designing profiles for chair frames and supports.
Conclusion: The Role of Machines in Plastic Chair Manufacturing
Each of the machines mentioned above plays a critical role in the overall manufacturing process of plastic chairs. While injection molding machines are essential for producing intricate, detailed parts with high precision, blow molding machines are optimal for creating lightweight, hollow parts like seats and backrests. Meanwhile, extrusion machines provide the necessary means for producing continuous profiles, such as the structural components of a chair.
Understanding the functions, benefits, and applications of these machines is crucial for manufacturers to optimize production processes, reduce costs, and maintain high-quality standards in the plastic chair industry. By utilizing these machines effectively, manufacturers can create functional, durable, and ergonomic plastic chairs to meet the demands of a wide variety of customers.
Leave a Reply