Your cart is currently empty!
SayPro Safety Protocols in Plastic Chair Manufacturing
SayPro is a Global Solutions Provider working with Individuals, Governments, Corporate Businesses, Municipalities, International Institutions. SayPro works across various Industries, Sectors providing wide range of solutions.
Email: info@saypro.online Call/WhatsApp: Use Chat Button 👇
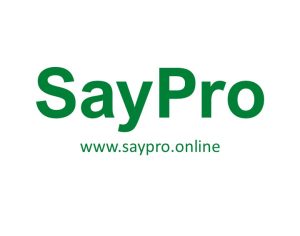
SayPro: Safety Protocols in Plastic Chair Manufacturing
Ensuring a safe working environment and complying with environmental regulations is essential in any manufacturing facility, including plastic chair production. Adopting robust safety protocols helps protect workers, minimizes operational risks, and supports compliance with industry regulations. Below are comprehensive safety measures that should be implemented in a plastic chair manufacturing facility to ensure both worker safety and environmental sustainability.
1. Worker Safety Protocols
Overview:
Worker safety is paramount in the plastic chair manufacturing process, where employees are exposed to various hazards such as machinery, chemicals, heat, and heavy lifting. Establishing strict safety protocols minimizes the risk of accidents, injuries, and long-term health issues.
Best Practices:
- Personal Protective Equipment (PPE):
Ensure that all workers wear the necessary PPE to protect themselves from workplace hazards. This includes:- Gloves: To protect hands from cuts, burns, and contact with hot surfaces or chemicals.
- Safety Glasses or Face Shields: To protect eyes from flying debris, chemicals, or molten plastic.
- Hearing Protection: For workers exposed to loud machinery, such as injection molding or blow molding machines.
- Safety Boots: To protect feet from heavy objects and prevent slips and falls.
- Respirators: In areas with high concentrations of dust or fumes, workers should use respirators to avoid inhaling harmful particles.
- Machine Safety:
- Safety Guards: Install protective guards on machines to prevent accidental contact with moving parts. This includes guards on injection molding machines, extrusion machines, and other high-risk equipment.
- Emergency Stop Buttons: Ensure that emergency stop buttons are easily accessible on all machinery. These should be clearly marked and maintained in a functional state.
- Lockout/Tagout (LOTO) Procedures: Implement strict lockout/tagout procedures when performing maintenance or repairs on machines. This ensures that machinery is properly de-energized to prevent accidental startups.
- Training and Awareness:
- Employee Training: All workers should receive comprehensive training on safety protocols, emergency procedures, and proper equipment usage. Training should be provided regularly to ensure workers are up-to-date on best safety practices.
- Safety Signage: Place clear and visible safety signs throughout the facility to remind workers of potential hazards, safety zones, and emergency exits.
- First Aid: Ensure that employees are trained in basic first aid and CPR. Additionally, the facility should be equipped with first-aid kits, and staff should know the location of medical supplies.
- Ergonomics and Manual Handling:
- Lifting Procedures: Train workers on proper lifting techniques to prevent strain injuries, particularly when handling heavy or bulky materials, like large molds or stacks of plastic chairs.
- Workstation Design: Ensure that workstations are ergonomically designed to reduce strain on workers. Adjustable tables, chairs, and equipment should be provided to accommodate various worker heights and preferences.
- Fire Safety:
- Fire Extinguishers and Sprinklers: Place fire extinguishers at strategic locations throughout the facility, especially near machines that may overheat or pose a fire risk. Ensure that sprinklers are installed and operational.
- Fire Safety Training: Conduct regular fire drills and provide fire safety training for all employees, focusing on safe evacuation procedures and the use of fire extinguishers.
2. Environmental Compliance Protocols
Overview:
Manufacturing facilities must comply with local, state, and federal environmental regulations to minimize their impact on the environment. This includes managing waste, controlling emissions, and ensuring proper disposal of hazardous materials.
Best Practices:
- Waste Management:
- Plastic Waste Reduction: Implement processes to minimize waste during production. This includes optimizing material usage and reusing scrap plastic in the production of new parts or as recycled raw material.
- Recycling Program: Establish a comprehensive recycling program for plastic scraps, defective parts, and packaging materials. Partner with recycling companies to ensure that materials are properly processed and reused.
- Waste Segregation: Separate hazardous waste (such as solvents, chemicals, or contaminated materials) from non-hazardous waste to ensure safe disposal and compliance with regulations.
- Air Quality Control:
- Ventilation Systems: Install adequate ventilation systems to reduce the concentration of fumes, vapors, or dust generated during the production process, such as from the heating of plastics or chemical additives.
- Emission Control: Monitor and control emissions from equipment such as injection molding machines or extruders. Ensure that machines are properly maintained and comply with air quality regulations.
- Dust Management: Use dust collection systems to reduce the presence of fine plastic particles in the air, which can be harmful to workers’ respiratory health.
- Chemical Handling and Storage:
- Hazardous Material Handling: Properly label, store, and dispose of any chemicals used in the manufacturing process, including lubricants, solvents, or flame retardants. Follow Material Safety Data Sheet (MSDS) guidelines for each chemical.
- Chemical Spill Response: Implement protocols for quickly and safely dealing with chemical spills. This includes having spill kits readily available and training workers on how to use them.
- Proper Labeling and Storage: Store chemicals in designated, clearly marked areas that meet safety and environmental standards. Containers should be tightly sealed to prevent leaks or contamination.
- Energy Efficiency and Waste Reduction:
- Energy Consumption Monitoring: Monitor energy consumption across the facility and identify opportunities to reduce energy usage. Invest in energy-efficient machinery and lighting systems.
- Sustainable Materials: Whenever possible, choose environmentally friendly raw materials, such as recycled plastics or biodegradable alternatives. This helps reduce the environmental impact of manufacturing operations.
3. Emergency Protocols
Overview:
In addition to daily safety measures, it is crucial to have emergency protocols in place to address unexpected incidents, such as fires, chemical spills, or equipment failures. These protocols must be clearly communicated and rehearsed regularly.
Best Practices:
- Emergency Response Team: Designate and train a team of employees to respond to emergencies. The team should be well-versed in first aid, fire response, spill containment, and evacuation procedures.
- Evacuation Plan: Develop and display a clear evacuation plan with designated exits and assembly points. Conduct regular evacuation drills to ensure that all employees know what to do in case of an emergency.
- Incident Reporting: Establish a system for reporting and documenting workplace accidents, near-misses, and environmental incidents. This helps identify hazards and implement corrective actions.
4. Regulatory Compliance and Audits
Overview:
To ensure compliance with environmental and safety regulations, regular audits and inspections are necessary. This includes both internal assessments and external inspections by regulatory bodies.
Best Practices:
- Regular Safety Audits: Conduct periodic safety audits to assess adherence to safety protocols and identify any gaps in training or equipment maintenance.
- Environmental Audits: Perform environmental audits to verify compliance with waste management, emissions, and chemical handling regulations. This ensures that the facility is operating within the bounds of environmental laws.
- Third-Party Inspections: Engage with external safety and environmental consultants to review practices and recommend improvements. This provides an independent assessment of your facility’s compliance.
Conclusion
Implementing comprehensive safety protocols and environmental compliance measures in a plastic chair manufacturing facility is essential for ensuring worker well-being and meeting regulatory standards. From worker protection through proper PPE, machine safety, and ergonomics, to environmental measures like waste management, energy efficiency, and air quality control, these protocols are vital for a safe and sustainable operation. Regular training, audits, and improvements will help maintain high safety standards while reducing environmental impact, ensuring that the manufacturing facility remains compliant and responsible.
Leave a Reply