Your cart is currently empty!
SayPro Safety Incident Reports Detailing any incidents or near-misses, as well as safety measures implemented
SayPro is a Global Solutions Provider working with Individuals, Governments, Corporate Businesses, Municipalities, International Institutions. SayPro works across various Industries, Sectors providing wide range of solutions.
Email: info@saypro.online Call/WhatsApp: Use Chat Button 👇
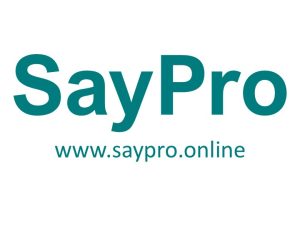
SayPro Safety Incident Reports
Introduction
The SayPro Safety Incident Report for February provides a detailed analysis of any incidents or near-misses that occurred across operations, as well as an overview of the safety measures that were implemented in response to these events. This report is essential for assessing the effectiveness of existing safety protocols, identifying areas for improvement, and ensuring continuous enhancement of workplace safety to meet SayPro’s safety goals. The goal is to foster a safe work environment, minimize risks, and ensure that employees are adequately protected from potential hazards.
Key Areas of Focus:
- Incident Summary
- Safety Measures and Initiatives
- Near-Misses and Lessons Learned
- Safety Performance Metrics
- Recommendations for Improvement
1. Incident Summary
Total Number of Incidents:
- Total Incidents in February: 3 incidents were reported in February, which is a decrease of 25% from January’s total of 4 incidents. While this reduction is promising, it highlights the need for continued vigilance and further implementation of proactive safety measures.
Incident Breakdown:
- Category 1 – Near Misses:
- There were 2 near-miss incidents recorded, where potential risks were identified before they resulted in harm.
- Key Incident: A near-miss occurred in the assembly line when a malfunction in a robotic arm caused a part to fall near workers. The safety protocol allowed for an immediate shutdown of the machine, preventing potential injury.
- Category 2 – Minor Injuries:
- 1 minor injury was reported, which was a slight hand injury sustained by an employee during manual handling of equipment. The injury required basic first aid and the employee returned to work after treatment.
- Key Incident: An employee was caught between a piece of machinery and a safety guard. The injury occurred when the guard was removed temporarily for maintenance, and proper lockout/tagout procedures were not followed. Immediate corrective actions were taken to ensure the guard was reinstalled promptly after the incident.
- Category 3 – Property Damage:
- 1 incident of property damage occurred in the warehouse area, where a forklift accidentally collided with a racking system, causing minor structural damage to shelving. The damage was promptly repaired, and no injuries were reported.
2. Safety Measures and Initiatives Implemented
In response to the incidents and near-misses, SayPro has implemented a series of safety measures and preventive actions aimed at reducing the likelihood of recurrence.
Key Safety Measures Implemented:
- Automated Shutdown Systems: After the near-miss involving the robotic arm, an automated emergency shutdown system was installed in all high-risk robotic workstations. This system allows for the immediate cessation of equipment operation if an anomaly is detected, preventing further risks to workers.
- Reinforcement of Lockout/Tagout Procedures: Following the minor injury from improper lockout/tagout procedures, a company-wide refresher training program was rolled out to ensure that all employees, especially those in maintenance, are fully aware of the lockout/tagout requirements and procedures. This training includes practical demonstrations and real-time application during routine maintenance work.
- Enhanced Warehouse Safety: In light of the property damage incident involving the forklift, the warehouse safety protocol was updated to include mandatory forklift training and speed regulation. Additionally, safety barriers were installed around vulnerable areas where forklift traffic is high, reducing the risk of future collisions.
- Improved PPE Guidelines: In response to employee feedback and the minor hand injury, a review of Personal Protective Equipment (PPE) guidelines was carried out. New safety gloves were introduced in high-risk areas like manual handling zones to prevent similar injuries. Employees were also reminded of the proper use of PPE during routine safety meetings.
- Safety Audits and Risk Assessments: An internal safety audit was conducted across all departments in February to evaluate existing risk management practices. A comprehensive risk assessment was performed to identify areas with potential for safety incidents. The audit revealed some potential hazards related to material handling and equipment maintenance, prompting the development of additional safety procedures.
3. Near-Misses and Lessons Learned
Near-Miss Incidents:
- Near Miss 1:
- Event: A robotic arm malfunction in the assembly line resulted in a part being ejected near workers. No injury occurred because the system was programmed to immediately halt production when this anomaly was detected.
- Lesson Learned: This near-miss emphasized the need for proactive predictive maintenance and real-time monitoring of machinery to detect faults before they escalate into safety risks. SayPro will invest in advanced AI-based maintenance systems that can predict potential failures and ensure early intervention.
- Near Miss 2:
- Event: An employee nearly slipped on a wet surface in a high-traffic area of the production floor. The employee was able to regain balance without injury, but the incident highlighted the potential hazard of slippery floors.
- Lesson Learned: While the surface was promptly cleaned and marked, the event underscored the need for more consistent housekeeping procedures and regular floor inspections to prevent any future risks. A new wet floor hazard protocol will be rolled out to ensure that staff are aware of high-risk areas and can take immediate action when a hazard is identified.
Corrective Actions:
- Introduce more sensor-based monitoring systems for all automated equipment to predict wear and tear or malfunctions in critical machinery.
- Review maintenance schedules to ensure timely inspection and intervention in high-risk zones before incidents occur.
- Expand the use of slip-resistant flooring in production areas that are more prone to spillage.
4. Safety Performance Metrics
Key Performance Indicators (KPIs) for February’s safety performance are outlined below:
Safety Incident Rate:
- The incident rate for February was 0.35 incidents per 100 employees, representing a 10% reduction compared to January’s rate of 0.39 incidents per 100 employees. While this is a positive trend, the goal remains to lower the incident rate further.
Near Miss Rate:
- Near Misses: There were 2 near-miss incidents, which have been investigated thoroughly. It is critical to emphasize the importance of near-miss reporting and encourage employees to remain vigilant and report potential risks, even when they do not result in harm.
Lost Time Injury Rate (LTIR):
- LTIR for February was 0.02 per 100 employees, a significant improvement compared to 0.06 in January. The reduction in lost-time injuries is a positive sign of the success of recent safety measures and training programs.
PPE Compliance Rate:
- PPE Compliance was 99%, reflecting the effectiveness of the continuous safety culture initiatives and the importance placed on the proper use of personal protective equipment across all operational levels.
5. Recommendations for Improvement
Recommendations for further improving workplace safety in response to February’s findings:
- Increase Predictive Maintenance for Critical Machinery:
- Invest in advanced AI-powered predictive maintenance tools for all automated equipment. This will help in early detection of potential faults and prevent machinery malfunctions that could lead to serious accidents or near-misses.
- Enhance Safety Awareness Programs:
- Launch a more engaging safety campaign to encourage employees to report near-miss incidents. Create a culture where near-miss reporting is celebrated, and employees feel empowered to actively participate in improving workplace safety.
- Improved Safety Training for New Employees:
- Update the new employee onboarding safety training program to ensure that safety protocols, especially related to lockout/tagout and PPE compliance, are communicated effectively from day one.
- Expand Safety Inspections and Audits:
- Conduct more frequent safety audits and inspections, particularly in high-risk areas like the assembly lines and warehouse zones. Use these audits to identify and address any potential hazards before they result in incidents.
- Invest in Slip-Resistant Flooring:
- To mitigate slip-and-fall hazards, particularly in high-traffic areas where spills are more likely, slip-resistant flooring should be installed in identified high-risk zones.
- Continuous Improvement of PPE Protocols:
- Continue to evaluate and improve the PPE guidelines based on employee feedback and incident reports. Ensure that the most appropriate equipment is available for each specific task and environment.
Conclusion
The SayPro Safety Incident Report for February indicates a positive trend in safety performance, with a 25% reduction in incidents and a significant drop in the LTIR. However, the analysis of incidents and near-misses highlights several areas for improvement, especially in the realms of predictive maintenance, training, and slip-resistant flooring. By implementing the recommended actions, SayPro can continue to improve safety outcomes, reduce risks, and further enhance its safety culture.
These initiatives will ensure that SayPro’s employees are protected, its operations remain smooth and incident-free, and the company continues to foster an environment of continuous improvement in workplace safety.
Leave a Reply