Your cart is currently empty!
SayPro Q&A and Troubleshooting Host live Q&A sessions to address
SayPro is a Global Solutions Provider working with Individuals, Governments, Corporate Businesses, Municipalities, International Institutions. SayPro works across various Industries, Sectors providing wide range of solutions.
Email: info@saypro.online Call/WhatsApp: Use Chat Button 👇
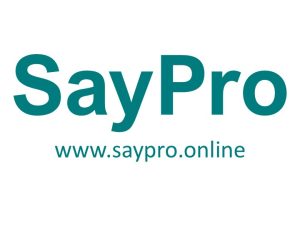
SayPro Live Q&A & Troubleshooting Sessions: Best Practices for Repair Report Documentation
Objective:
The goal of hosting live Q&A sessions is to offer participants an opportunity to directly engage with experts, address challenges they encounter while completing their repair reports, and improve their troubleshooting and documentation skills. These sessions will also provide an interactive platform for participants to ask questions, share experiences, and receive real-time advice on handling repair scenarios effectively.
1. Structure of the Live Q&A Session
The live Q&A session will be divided into three main parts to ensure it is comprehensive and engaging for participants:
- Introduction and Overview (10 minutes)
- Welcome: Brief introduction to the session format and goals.
- Key Topics Covered: Highlight the common repair scenarios, documentation challenges, and best practices for troubleshooting that will be addressed during the session.
- Facilitators: Introduction of the expert technicians or trainers leading the session.
- Live Q&A – Participant Questions (30-40 minutes)
- Real-Time Troubleshooting: Participants submit questions or issues they’ve encountered while working on their repair reports.
- Examples of Questions:
- “How do I handle a situation where the root cause is unclear after initial troubleshooting?”
- “What’s the best way to document intermittent generator issues that occur under specific conditions?”
- “I’m having trouble with categorizing parts in the repair report. Any advice?”
- Facilitators’ Input: Trainers and technicians provide expert solutions, guiding participants step-by-step through their questions and sharing troubleshooting tips.
- Best Practices for Troubleshooting & Documentation (15-20 minutes)
- Common Troubleshooting Scenarios: Discuss typical generator issues, how to diagnose them, and how to document these findings accurately.
- Repair Report Best Practices:
- How to properly structure the repair report.
- How to categorize parts and services for clarity.
- How to write clear, concise, and accurate problem descriptions and repair steps.
- Interactive Troubleshooting: Share sample case studies and have participants walk through troubleshooting steps in real time. Participants can ask follow-up questions as they work through the example scenarios.
2. Key Topics to Address During the Live Q&A
Here are some key topics that can guide the troubleshooting and repair documentation discussions during the live Q&A:
Common Troubleshooting Challenges
- Identifying the Root Cause of Generator Failures
- Problem: “The generator is not starting after maintenance, but the fuel system looks fine.”
- Troubleshooting Steps:
- Check for issues with the ignition system.
- Inspect the alternator and charging system.
- Examine any sensors that might be failing (e.g., fuel level sensor, temperature sensor).
- Documenting these steps clearly and thoroughly in the report.
- Intermittent Issues (e.g., Overheating, Noise, or Vibration)
- Problem: “The generator overheats intermittently, but it seems fine during normal operation.”
- Troubleshooting Steps:
- Check coolant levels and radiator performance.
- Inspect temperature sensors and fan functionality.
- Perform stress tests to simulate overheating conditions.
- Record every condition under which overheating occurs.
- Documentation Tip: It’s important to document the time, temperature readings, and any operating conditions that lead to intermittent failures.
- Electrical System Failures
- Problem: “The generator’s electrical system is not delivering power even though the engine runs.”
- Troubleshooting Steps:
- Verify all electrical connections, including fuses and relays.
- Test the alternator’s output and voltage regulator.
- Inspect for short circuits or damaged wiring.
- Document voltages and resistance readings.
- Documentation Tip: Include diagnostic codes (if applicable), voltage readings, and equipment serial numbers.
Best Practices for Repair Documentation
- Accurate Problem Descriptions
- Clear and concise descriptions of the issue can help technicians and managers quickly understand the problem.
- Example: “Generator failed to start after routine maintenance. Initial checks show fuel system is operational, but the starter motor is not engaging.”
- Organizing Repair Steps
- List the troubleshooting and repair actions in a logical sequence.
- Break down steps: Diagnosis → Action → Verification → Outcome.
- Example:
- Diagnosis: “Starter motor failure, no engagement.”
- Action: “Replaced faulty starter motor and cleaned electrical contacts.”
- Verification: “Tested generator startup; successful.”
- Outcome: “Generator now starts without issue.”
- Parts Replaced/Serviced
- Clearly document the parts that were replaced, including part numbers, quantities, and vendor information.
- Example: “Replaced starter motor (Part No. 56789) and spark plugs (Part No. 112233).”
- Recording Test Results
- Always test the generator after repairs and include test results in the report.
- Example: “Tested generator under load. Output power: 400V at 50Hz, stable operation.”
3. Tools and Techniques for Troubleshooting
During the live session, participants should be introduced to tools and methods that can help them troubleshoot more effectively:
- Diagnostic Tools:
- Multimeter (for voltage, resistance, and current tests).
- Thermal cameras (for detecting overheating issues).
- Vibration sensors (for monitoring generator vibration levels).
- Troubleshooting Checklists:
- Providing participants with troubleshooting checklists for common generator issues will help them stay organized and methodical when diagnosing problems.
- Example Checklist for Generator Not Starting:
- Verify fuel levels and fuel quality.
- Inspect the battery voltage.
- Test the ignition system components (e.g., starter motor, relay).
- Check for any electrical shorts or fuse issues.
- Test the alternator’s voltage output.
- Root Cause Analysis:
- Introduce the 5 Whys Method: Ask “why” repeatedly (usually five times) to drill down to the root cause of a problem. This helps technicians move beyond symptoms and pinpoint underlying issues.
4. Common Q&A Scenarios
Q1: How do I troubleshoot when the issue isn’t immediately obvious?
- Solution: Start with a general inspection (visual checks, listening for irregular sounds, checking for leaks, etc.). Use diagnostic tools (e.g., multimeters, thermal imaging, or vibration sensors) to narrow down the cause. Always keep detailed records of what you tested and what results were observed.
Q2: How should I document intermittent issues that don’t happen every time the generator is used?
- Solution: In cases of intermittent failure, it’s essential to document the exact conditions when the problem occurred (e.g., under heavy load, after X hours of operation). Include relevant data, such as temperature readings or system logs, to provide insight into the issue.
Q3: My repair report is getting too long. How can I make it more concise while still being thorough?
- Solution: Focus on clarity and brevity. Avoid overly technical jargon, but don’t leave out essential details. Break the report into clear sections: Problem, Diagnosis, Repairs, Parts Replaced, Test Results, Outcome. Use bullet points to streamline information and make it easy to digest.
5. Wrap-Up and Next Steps
At the end of each live Q&A session, summarize the key takeaways and offer guidance on how participants can implement the best practices in their day-to-day work:
- Recap Key Points: Summarize the key troubleshooting techniques and documentation tips discussed during the session.
- Encourage Practice: Encourage participants to apply what they’ve learned to their ongoing repair reports. Offer ongoing support for questions that come up as they put the new knowledge into practice.
- Provide Additional Resources: Share links to troubleshooting guides, repair report templates, or further reading materials.
Final Reminder: Participants are encouraged to submit questions ahead of time for the next Q&A session to ensure that all relevant issues are addressed.
By hosting these live Q&A and troubleshooting sessions, SayPro can provide significant value to its technicians and service managers, helping them become more effective at diagnosing issues and creating accurate, detailed repair reports. The sessions will also foster a collaborative learning environment where participants can exchange knowledge and experiences.
Leave a Reply