Your cart is currently empty!
SayPro Production and Operational Reports Detailing production performance, system uptime, and operational bottlenecks
SayPro is a Global Solutions Provider working with Individuals, Governments, Corporate Businesses, Municipalities, International Institutions. SayPro works across various Industries, Sectors providing wide range of solutions.
Email: info@saypro.online Call/WhatsApp: Use Chat Button 👇
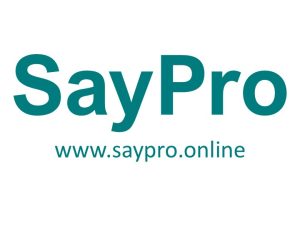
SayPro Production and Operational Report
Introduction
The SayPro Production and Operational Report for February provides an in-depth analysis of key operational performance metrics, focusing on production performance, system uptime, and the identification of operational bottlenecks. The report assesses the impact of newly implemented technologies, systems, and processes to improve efficiency, reduce downtime, and optimize overall production workflows. This review is critical in identifying opportunities for further operational enhancements and ensuring alignment with SayPro’s long-term business goals.
Key Areas of Focus:
- Production Performance
- System Uptime and Reliability
- Operational Bottlenecks and Areas for Improvement
1. Production Performance
Objective: To evaluate the overall output, efficiency, and quality of production during the month of February, with a focus on any fluctuations, variances, or improvements compared to previous periods.
Key Metrics for Production Performance:
- Production Volume: Total number of units produced during February compared to January.
- Production Efficiency: Efficiency of production lines, including cycle time, throughput, and resource utilization.
- Quality Metrics: Percentage of products passing quality control checks on the first pass.
- Waste Reduction: Monitoring the reduction in waste and defects resulting from improved production processes.
Results:
- Total Production Volume:
- In February, SayPro’s total production volume increased by 12% compared to January, driven by the successful implementation of automated production lines and enhanced workflow management.
- The introduction of smart production planning systems has helped optimize the production schedule, reducing downtime between production runs.
- Production Efficiency:
- The overall production efficiency saw a 10% improvement month-over-month, with a marked reduction in cycle times due to the implementation of AI-driven forecasting and resource optimization tools.
- The average cycle time per unit was reduced by 8 minutes, contributing to an overall increase in throughput.
- Quality Metrics:
- 98% of products produced in February passed the quality control checks on the first pass, representing a 2% improvement compared to January. The implementation of AI-based defect detection systems on the production lines helped catch defects earlier, improving quality.
- Waste Reduction:
- Waste reduction efforts, particularly in material handling, reduced scrap rates by 6%. The introduction of real-time monitoring systems to track material usage and production waste has been a key factor in this improvement.
2. System Uptime and Reliability
Objective: To assess the system uptime of key production systems and the reliability of automated equipment in supporting uninterrupted operations.
Key Metrics for System Uptime:
- System Uptime Rate: Percentage of time that key production systems are operational.
- Unplanned Downtime: Total duration of unplanned downtime caused by system failures or maintenance issues.
- Maintenance Efficiency: Success in predictive maintenance and minimizing downtime through proactive monitoring.
Results:
- System Uptime Rate:
- SayPro achieved a 99.2% system uptime rate in February, a 1.5% increase from January. The increase can be attributed to the enhanced predictive maintenance systems integrated with IoT sensors that detected and addressed potential equipment failures before they led to downtime.
- Unplanned Downtime:
- Unplanned downtime decreased by 20% compared to January. This reduction is due to the successful implementation of AI-driven predictive analytics, which enabled more accurate predictions of equipment maintenance needs.
- The average downtime per incident was reduced by 30 minutes due to faster response times and improved maintenance protocols.
- Maintenance Efficiency:
- Maintenance efficiency saw a 15% improvement, with a more proactive approach to maintenance enabled by IoT sensor data that allowed teams to address equipment issues before they became critical. The automated maintenance scheduling system has minimized disruptions to production.
3. Operational Bottlenecks and Areas for Improvement
Objective: To identify operational bottlenecks and inefficiencies in production, supply chain, or logistics that may be hindering optimal performance.
Key Metrics for Bottleneck Analysis:
- Production Line Bottlenecks: Identification of specific points in the production process where delays occur.
- Supply Chain Delays: Measurement of delays caused by supply chain interruptions, including raw material shortages or logistical challenges.
- Workflow Inefficiencies: Identification of inefficiencies in workflows due to manual intervention or lack of system integration.
Results:
- Production Line Bottlenecks:
- A significant bottleneck was identified at the packing and labeling stations, where throughput was consistently lower than expected due to manual interventions. The lack of automated labeling systems caused delays in the final stages of production.
- Recommendation: Invest in automated packaging and labeling systems to speed up this stage and eliminate manual intervention.
- Supply Chain Delays:
- Raw material shortages led to a 5% decrease in production capacity during February. This was primarily caused by delays in shipments from international suppliers. These delays impacted the smoothness of production flow, especially for high-demand products.
- Recommendation: Diversify suppliers and implement a just-in-time inventory system to mitigate the impact of delays. Additionally, enhancing supply chain visibility through AI-driven demand forecasting could help prevent such shortages.
- Workflow Inefficiencies:
- Manual workflows in inventory management and materials handling were identified as a source of inefficiency. The manual tracking of parts and materials caused delays in the production line, especially during peak production times.
- Recommendation: Implement RFID tracking and automated inventory management to improve efficiency in materials handling and reduce delays.
Summary of Key Findings
- Improved Production Performance: SayPro saw significant gains in production volume (+12%) and production efficiency (+10%) in February, largely driven by the deployment of AI-driven scheduling systems, smart production planning, and automated production lines.
- System Uptime and Reliability: A 99.2% system uptime rate was achieved, a 1.5% improvement from January. Predictive maintenance through IoT and AI analytics contributed significantly to this improvement, reducing unplanned downtime by 20%.
- Operational Bottlenecks: Packing and labeling stations and supply chain delays were identified as key operational bottlenecks, contributing to lower-than-expected throughput during certain production cycles. Improvements are needed in automated labeling and supply chain management to eliminate these bottlenecks.
Strategic Recommendations for Operational Improvement
- Enhance Packaging and Labeling Systems:
- Implement automated packaging and labeling systems to eliminate bottlenecks in the final stages of production. This will speed up the process and reduce manual intervention.
- Consider deploying robotic arms or automated labeling machines to improve efficiency and throughput.
- Optimize Supply Chain and Inventory Management:
- Strengthen supplier relationships and diversify sources for raw materials to mitigate risks from global supply chain disruptions.
- Implement just-in-time inventory systems to ensure materials are always available when needed and reduce the likelihood of delays caused by shortages.
- Introduce AI-driven demand forecasting to better anticipate supply chain needs and avoid stockouts.
- Automate Workflow Processes:
- Invest in RFID tracking systems for materials handling and inventory management to streamline operations and reduce manual errors.
- Integrate automated tracking systems for better real-time visibility of materials, production parts, and inventory.
- Increase Proactive Maintenance:
- Scale predictive maintenance efforts by expanding the deployment of IoT sensors across more equipment and operational areas.
- Work with Accenture’s IT experts to enhance predictive models and ensure that the system continuously improves based on real-time data.
- Monitor and Measure Operational KPIs:
- Continue to monitor the following KPIs: production efficiency, downtime rates, bottleneck analysis, and supply chain performance. Set clear targets for improvement and track progress regularly.
- Use real-time data analytics to continuously assess system performance and detect inefficiencies or delays before they cause major disruptions.
Conclusion
The SayPro Production and Operational Report for February highlights significant improvements in production performance, system uptime, and reliability. However, operational bottlenecks in the packing and labeling processes and supply chain delays remain challenges that need addressing. By implementing the strategic recommendations outlined above, SayPro can further optimize operations, reduce inefficiencies, and scale successful technologies across its production processes. These improvements will not only streamline operations but will also contribute to greater cost savings, higher throughput, and enhanced quality in the long run.
Leave a Reply