Your cart is currently empty!
SayPro Product and Service Offerings
SayPro is a Global Solutions Provider working with Individuals, Governments, Corporate Businesses, Municipalities, International Institutions. SayPro works across various Industries, Sectors providing wide range of solutions.
Email: info@saypro.online Call/WhatsApp: Use Chat Button 👇
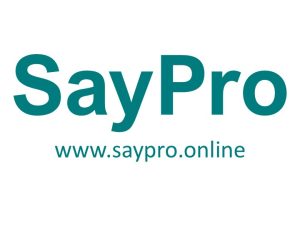
SayPro’s Product and Service Offerings: Understanding the Machinery and Equipment
SayPro is a leading provider of high-quality machinery and equipment used in various industries, ranging from manufacturing to specialized operations. This section outlines the different types of machinery SayPro offers and the associated repair services, helping entrepreneurs, technicians, and service providers gain a comprehensive understanding of the products they will be working with.
1. Overview of SayPro Machinery and Equipment
SayPro designs and manufactures cutting-edge machinery tailored to meet the needs of businesses in a wide range of industries. These products are known for their durability, efficiency, and innovative technology. Understanding the core machinery and their functions is essential for anyone operating a repair service that specializes in SayPro equipment.
a) Industrial Machinery
- Description: SayPro’s industrial machinery is designed to optimize large-scale manufacturing processes, automation, and precision. These machines are used in factories, warehouses, and other production environments.
- Examples: CNC machines, industrial robots, conveyor systems, and automated assembly lines.
- Repair Focus: Common repairs involve mechanical components, electrical systems, and software updates or troubleshooting.
b) Agricultural Equipment
- Description: SayPro also offers agricultural machinery designed for efficiency in farming and crop production. These machines include tractors, harvesters, irrigation systems, and soil preparation equipment.
- Examples: Tractors, plowing machines, seeders, irrigation pumps, and automated harvesting systems.
- Repair Focus: Repairs often involve engine maintenance, hydraulic systems, and parts replacement for wear-and-tear components.
c) Construction Machinery
- Description: SayPro manufactures heavy-duty construction machinery designed for building, excavation, and roadwork tasks. These machines are built to withstand demanding job sites.
- Examples: Excavators, bulldozers, cranes, concrete mixers, and backhoes.
- Repair Focus: Repair services focus on hydraulic systems, electrical components, and drivetrain maintenance.
d) Packaging and Processing Equipment
- Description: SayPro’s packaging and processing equipment is used in various industries, including food and beverage, pharmaceuticals, and consumer goods. These machines help automate the packaging, labeling, and processing stages.
- Examples: Automated packaging machines, filling and capping machines, and labeling equipment.
- Repair Focus: Regular maintenance of motors, sensors, mechanical parts, and troubleshooting machine settings.
2. Key Features and Technologies of SayPro Equipment
SayPro machinery integrates advanced technology to deliver high levels of productivity, precision, and reliability. Repair service businesses need to understand the key technological aspects of these machines to provide high-quality repair services.
a) Automation and Robotics
- Description: Many SayPro machines, especially in industrial and manufacturing settings, are equipped with automation features. Robotics systems improve efficiency, consistency, and speed, reducing the need for manual labor.
- Repair Focus: Technicians must be skilled in troubleshooting and repairing automated control systems, robotic arms, and sensors. Understanding programming and software is crucial in diagnosing issues related to automation.
b) Integrated Software and Controls
- Description: SayPro machinery often includes sophisticated software that controls various functions, from operational speed to precision and diagnostics. These machines may require regular software updates or troubleshooting.
- Repair Focus: Repair technicians must be proficient in diagnosing software issues, performing firmware updates, and recalibrating control systems. They must also understand how to interface with machinery through specialized software.
c) Hydraulic Systems
- Description: Hydraulic systems are common in many of SayPro’s machines, particularly in construction, agricultural, and industrial equipment. These systems use pressurized fluid to drive components and enable powerful movements.
- Repair Focus: Understanding hydraulic pumps, valves, actuators, and pressure systems is essential for repairing leaks, blockages, or mechanical failures in these systems.
d) Electrical and Power Systems
- Description: Electrical systems in SayPro machinery include power circuits, motors, controllers, sensors, and other components necessary for operation. Many machines rely on complex electrical setups for precision and automation.
- Repair Focus: Repair technicians should be skilled in electrical diagnostics, troubleshooting circuit boards, replacing damaged wires or components, and ensuring electrical systems are running optimally.
e) Mechanical Components and Assemblies
- Description: SayPro machinery contains a range of mechanical components like gears, belts, pulleys, and structural elements that need regular maintenance and servicing to ensure smooth operation.
- Repair Focus: Mechanical repair focuses on wear-and-tear components such as bearings, belts, shafts, and motors. Technicians must be capable of dismantling and reassembling machinery to replace worn or broken parts.
3. SayPro’s Service Offerings
In addition to manufacturing machinery, SayPro provides various services that complement their products. These services are critical for customers who require ongoing maintenance, repairs, and technical support. Repair service entrepreneurs can leverage these offerings to create additional revenue streams or improve customer relationships.
a) Preventative Maintenance Services
- Description: SayPro offers regular maintenance contracts to ensure that machinery operates at peak performance. Preventative maintenance is a cost-effective way to identify issues before they become serious problems.
- Opportunity for Repair Services: Repair service businesses can partner with SayPro to offer maintenance services, including regular inspections, part replacements, cleaning, and system recalibration.
- Benefit: Regular maintenance contracts can provide a steady stream of income and increase customer loyalty.
b) Technical Support and Consultation
- Description: SayPro provides technical support for businesses using their machinery. This includes troubleshooting assistance, consultation, and expert advice on optimizing machinery for different operations.
- Opportunity for Repair Services: Service providers can offer technical consultation services to assist clients with equipment setup, operation, and troubleshooting, enhancing the repair services they offer.
- Benefit: This provides an additional revenue source while establishing your company as an expert in SayPro machinery repair and maintenance.
c) Spare Parts and Component Sales
- Description: SayPro sells genuine replacement parts for its machinery. These parts are designed to maintain the performance and longevity of their machines.
- Opportunity for Repair Services: Repair businesses can source parts directly from SayPro or authorized distributors and offer them to customers during repair jobs.
- Benefit: Selling spare parts allows repair businesses to increase their profit margins, as parts sales typically have higher margins than labor.
d) Training and Certification Programs
- Description: SayPro offers training programs to teach users how to operate and maintain their machinery effectively. These programs are beneficial for both individual operators and maintenance teams.
- Opportunity for Repair Services: Repair service providers can offer additional training for customers’ staff, helping them become proficient in routine maintenance and basic troubleshooting of SayPro machinery.
- Benefit: This positions your service as an all-in-one solution provider and provides an opportunity to charge for training programs or workshops.
e) Warranty and Service Contracts
- Description: SayPro offers warranties and extended service contracts for their machinery. These contracts cover repairs and replacements for a defined period, often beyond the initial warranty.
- Opportunity for Repair Services: Repair service businesses can provide services under these warranties, offering repairs or replacements covered by SayPro’s warranty terms. Extended service contracts can also be managed to provide long-term maintenance and repair support.
- Benefit: Offering warranty repair services can create long-term partnerships and customer retention, providing ongoing opportunities for revenue.
4. Repair Challenges and Solutions
SayPro machinery, while known for its reliability, still requires regular maintenance and occasional repairs due to the wear and tear from heavy use. Repair service providers need to be prepared for a variety of challenges related to these machines.
a) Parts Availability and Sourcing
- Challenge: Sometimes, customers may need specific parts for their SayPro machinery, and these parts may be on backorder or difficult to source.
- Solution: Establish relationships with SayPro or authorized dealers for quicker access to spare parts. Offer customers options for expedited shipping if needed.
b) Specialized Knowledge and Training
- Challenge: SayPro machinery can be complex, and repair technicians must have specialized knowledge and training to handle repairs effectively.
- Solution: Ensure that your team receives regular training from SayPro or an authorized training center to stay up to date with the latest technologies and repair methods.
c) Diagnostic Tools and Equipment
- Challenge: Many SayPro machines require sophisticated diagnostic tools to identify issues, particularly when dealing with electronic or automated systems.
- Solution: Invest in the proper diagnostic equipment and software required to perform accurate assessments of machinery health. This could include machine-specific diagnostic tools or general equipment for monitoring electrical and mechanical functions.
Conclusion
Understanding SayPro’s machinery and its product offerings is critical for repair service businesses to succeed. By gaining insight into the technology, features, and common issues associated with SayPro machines, entrepreneurs can offer more efficient, informed, and comprehensive repair services. By also leveraging SayPro’s additional services like spare parts sales, preventative maintenance, and technical support, repair businesses can build a more robust and sustainable business model. This holistic approach to understanding both the machinery and associated services helps ensure that repair services meet the high standards that SayPro customers expect.
Leave a Reply