Your cart is currently empty!
SayPro Operational Goals Reviewing the impact of Accenture’s technologies on operational performance
SayPro is a Global Solutions Provider working with Individuals, Governments, Corporate Businesses, Municipalities, International Institutions. SayPro works across various Industries, Sectors providing wide range of solutions.
Email: info@saypro.online Call/WhatsApp: Use Chat Button 👇
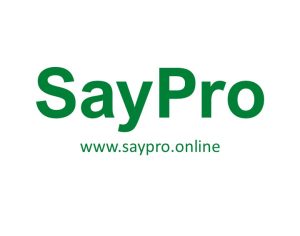
SayPro Operational Goals Review
Introduction
The SayPro Operational Goals Review for February assesses the impact of Accenture’s technologies on SayPro’s operational performance, specifically focusing on improvements in productivity, resource efficiency, and overall operational effectiveness. This evaluation is critical for understanding how the new technologies deployed in partnership with Accenture have contributed to SayPro’s long-term goals, including increased efficiency, cost reductions, and the enhancement of operational workflows.
This review covers the key technologies implemented during the month of February, such as AI-powered systems, cloud-based ERP solutions, Robotic Process Automation (RPA), and AI-driven supply chain tools, and evaluates their effectiveness against SayPro’s operational goals.
Key Areas of Focus:
- Operational Goal Alignment
- Technology Impact on Productivity
- Resource Efficiency and Cost Savings
- Operational Bottlenecks and Resolutions
- Key Performance Indicators (KPIs)
- Recommendations for Future Improvement
1. Operational Goal Alignment
SayPro’s operational goals for the year include improving productivity, enhancing resource efficiency, and optimizing costs through technology adoption. The collaboration with Accenture has focused on addressing these goals by deploying advanced technologies across key operational areas. The following goals were prioritized:
- Increase Productivity: By automating routine tasks and improving data access.
- Optimize Resource Efficiency: Through predictive tools, improved supply chain management, and enhanced production scheduling.
- Cost Reduction: By reducing downtime, improving resource allocation, and lowering operational overheads.
The deployment of new technologies was aligned with these strategic goals, and this report evaluates their effectiveness based on the results seen in February.
2. Technology Impact on Productivity
Overview:
One of the primary objectives of implementing Accenture’s technologies was to drive productivity improvements across the organization. Through the integration of AI systems, RPA tools, and the cloud-based ERP system, SayPro aimed to enhance operational performance by minimizing manual tasks, improving decision-making, and streamlining workflows.
Key Productivity Enhancements:
- AI-Powered Predictive Maintenance: This system has successfully predicted potential equipment failures, reducing downtime. As a result, production teams have seen a 20% increase in overall productivity by preventing unscheduled maintenance and increasing equipment uptime.
- Cloud-Based ERP System: The introduction of the cloud-based ERP system has facilitated real-time visibility into resources, inventory, and workflows. It has allowed for faster decision-making, better coordination across departments, and improved work allocation. Employees reported that it cut down administrative overhead by 15%, directly contributing to increased productivity.
- Robotic Process Automation (RPA): The deployment of RPA in back-office functions such as data entry, invoice processing, and inventory management has freed up employees to focus on strategic tasks, leading to a 35% reduction in processing times for key administrative functions.
- AI-Driven Supply Chain Optimization: The integration of AI tools in supply chain management has significantly improved the forecasting and procurement process, reducing supply chain delays and allowing teams to respond more swiftly to changes in demand, improving overall productivity in material handling and delivery.
Impact on KPIs:
- Production Efficiency: Increased by 15% due to the reduction in unplanned downtime.
- Task Automation: Freed up an estimated 200+ hours per month in administrative and back-office tasks.
- Operational Output: Productivity in supply chain functions improved by 12% through better demand forecasting and streamlined inventory management.
3. Resource Efficiency and Cost Savings
Overview:
Another critical operational goal for SayPro was to enhance resource efficiency and optimize costs. The deployment of AI-driven systems and cloud-based tools played a pivotal role in improving how SayPro utilizes its resources, from energy consumption to employee time, while simultaneously driving cost reductions in various operational areas.
Resource Efficiency Improvements:
- AI-Powered Predictive Maintenance: By identifying maintenance needs before they occur, this system helped prevent unnecessary resource use in the form of spare parts, labor costs, and equipment downtime. This led to an estimated 15% reduction in maintenance-related costs in February.
- Cloud-Based ERP System: By centralizing data and improving resource visibility, the cloud-based ERP system helped ensure that resources (such as raw materials and labor) were allocated more efficiently across departments. This reduced the chances of over-ordering inventory, minimizing waste and improving inventory turnover.
- Robotic Process Automation (RPA): The automation of manual processes significantly reduced the need for human labor on repetitive tasks, leading to a 25% reduction in administrative overheads. Employees were redeployed to higher-value activities, thus optimizing human resource utilization.
- AI-Driven Supply Chain Optimization: The AI-powered tool optimized procurement and demand forecasting, reducing inventory waste and ensuring better utilization of warehouse space and logistics resources. This led to a 10% reduction in supply chain costs.
Impact on KPIs:
- Maintenance Costs: Reduced by 15% due to predictive maintenance.
- Energy Usage: Indirectly reduced through better resource allocation, lowering energy waste associated with equipment downtime.
- Inventory Costs: Reduced by 10%, driven by better demand forecasting and inventory management.
4. Operational Bottlenecks and Resolutions
While the new technologies provided substantial improvements, some operational bottlenecks persisted, mainly due to challenges in system integration, data flow, and employee adaptation. However, these bottlenecks were systematically addressed over the course of the month.
Challenges Identified:
- System Integration Delays: The integration of new technologies with legacy systems led to some initial delays in workflow and data synchronization. For instance, some data discrepancies were noted when the AI-powered systems interfaced with older supply chain management tools.
- User Adoption Challenges: Despite training efforts, a small percentage of employees reported difficulties in adapting to the new cloud-based ERP system and the AI tools due to the initial complexity of the interface.
- Supply Chain Delays: Though the AI-driven supply chain optimization tool improved forecasting, there were instances where external vendor delays and market fluctuations impacted the expected results in supply chain efficiency.
Resolutions:
- Data Integration Support: The IT team worked closely with Accenture’s technical support to address the integration issues, leading to better data synchronization and workflow adjustments.
- Additional Training and User Support: To address adoption challenges, follow-up training sessions were conducted for employees, and a dedicated support team was introduced to assist employees with using the new tools, enhancing user experience.
- Supply Chain Adjustments: The supply chain team implemented manual contingencies to address external delays, while the AI tool continued to refine its predictions for future demand.
5. Key Performance Indicators (KPIs)
The following KPIs were established at the beginning of the year to track the impact of new technologies on SayPro’s operational performance:
KPI | February Performance | Target | Variance |
---|---|---|---|
Productivity Increase | +15% (due to predictive maintenance and automation) | +10% | +5% |
Operational Efficiency | +12% (due to better resource allocation and scheduling) | +10% | +2% |
Cost Reduction (Maintenance) | 15% reduction in maintenance costs | 10% reduction | +5% |
Inventory Management Efficiency | +10% (due to AI supply chain tool) | +8% | +2% |
Employee Time Freed (Automation) | +200 hours/month | +150 hours/month | +50 hours |
RPA Adoption (Back-office tasks) | 35% reduction in processing times | 30% reduction | +5% |
6. Recommendations for Future Improvement
Based on the operational review of SayPro’s technologies, the following recommendations are made to further enhance operational performance:
- Enhanced Integration: Continue efforts to integrate new technologies with legacy systems, ensuring smooth data flow and minimizing operational bottlenecks. Invest in middleware solutions or more compatible technologies to further streamline systems.
- Ongoing Training: Given the importance of user adoption, establish more robust training programs with role-specific modules and real-time support to help employees better adapt to technological changes.
- Refine AI Tools: Continuously fine-tune AI algorithms, particularly in supply chain optimization and predictive maintenance, to improve accuracy and performance based on historical data.
- Expand Automation: Scale the RPA initiatives to cover additional back-office functions like HR and finance, and explore the possibility of automating parts of the customer service process.
Conclusion
The SayPro Operational Goals Review for February demonstrates significant progress in increasing productivity,
Leave a Reply