Your cart is currently empty!
SayPro Monthly January SCSPR-98: SayPro Monthly Plastic Chairs Training Course
SayPro is a Global Solutions Provider working with Individuals, Governments, Corporate Businesses, Municipalities, International Institutions. SayPro works across various Industries, Sectors providing wide range of solutions.
Email: info@saypro.online Call/WhatsApp: Use Chat Button 👇
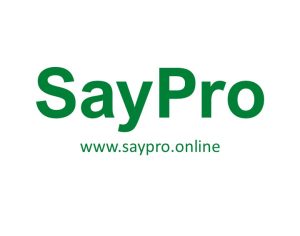
Course Overview: The SayPro Monthly Plastic Chairs Training Course provides an in-depth exploration of the plastic chair manufacturing process, with a special focus on the strategic partnerships involved in bulk manufacturing, and the role of royalty in the production process. This course, presented under the auspices of the SayPro Strategic Partnerships Office, aims to educate both current and potential partners about the intricate details of plastic chair production.
Module 1: Raw Material Selection
The first step in the plastic chair manufacturing process is choosing the appropriate raw materials. This section covers:
- Types of Plastics Used:
- Polypropylene (PP): The most common material, known for its durability and low cost.
- Polyethylene (PE): Lightweight and resistant to impact.
- Acrylonitrile Butadiene Styrene (ABS): Known for its strength and resilience.
- Material Sourcing:
- Overview of the suppliers and global sourcing strategies for high-quality plastics.
- Considerations regarding the sustainability of the materials.
- Additives and Colorants:
- How additives like UV stabilizers, antioxidants, and colorants are incorporated for durability, appearance, and protection from environmental degradation.
Module 2: Material Processing
Once the raw materials are selected, they must undergo processing before they can be molded into the desired shape.
- Pelletizing:
- Plastics are converted into uniform pellets to ensure consistency during molding.
- Drying Process:
- The importance of drying plastics to remove any moisture content, which can affect the final quality of the product.
- Melting and Compounding:
- The materials are melted and compounded with additives to form a homogenous mixture that can be molded.
Module 3: Molding Process
The molding stage is critical to achieving the final shape of the plastic chair. The following processes are discussed:
- Injection Molding:
- Plastic is injected into a mold under high pressure. This method is commonly used for producing large quantities of plastic chairs with consistent shapes and dimensions.
- Compression Molding:
- Materials are placed into an open mold cavity and compressed to form the chair structure. This method is typically used for larger, more durable chairs.
- Rotational Molding:
- This technique involves heating the material in a mold that rotates on two axes to ensure even distribution. It’s often used for hollow chairs or furniture.
- Quality Control in Molding:
- Ensuring the consistency of the mold, from temperature control to mold pressure, to prevent defects in the final product.
Module 4: Cooling Process
Cooling is a crucial step in shaping the plastic chair, where the material solidifies into its final form.
- Cooling Techniques:
- Air-cooling and water-cooling methods are explored, with an emphasis on cooling times and uniformity to prevent warping or deformities in the plastic.
- Cooling Cycle Duration:
- The time needed for cooling varies depending on the material used, the mold design, and the thickness of the plastic.
- Post-Cooling Inspection:
- Once cooled, the chairs undergo a thorough inspection to detect any irregularities or defects that might have occurred during the cooling process.
Module 5: Final Assembly
After the chair parts are molded and cooled, they must be assembled into the finished product.
- Component Assembly:
- Chairs are often made from multiple molded pieces that require assembly. For instance, backrests, seat sections, and legs might be separate components that need to be joined together.
- Fastening and Securing:
- Various fastening methods such as screws, snap-fits, and welded joints are employed to secure the components.
- Surface Treatment and Finishing:
- The plastic chairs are often polished, coated, or painted to improve their aesthetic appeal or durability.
Module 6: Testing and Quality Control
To ensure that each chair meets SayPro’s high standards, rigorous testing and quality control procedures are followed.
- Load Testing:
- Chairs are tested for weight tolerance, checking their strength and stability under varying amounts of pressure.
- Durability and Impact Resistance Testing:
- Simulations are carried out to assess the chair’s ability to withstand impacts and long-term use.
- Safety Checks:
- Ensuring that all edges are smoothed and that the chair poses no safety hazards to users, such as sharp corners or unstable legs.
Module 7: Packaging and Distribution
Once assembled and tested, the chairs are prepared for distribution.
- Packaging Techniques:
- Discussing the most efficient and cost-effective packaging methods to prevent damage during transportation. Options include plastic wraps, cardboard boxes, and protective corner reinforcements.
- Logistics and Bulk Manufacturing:
- Efficient strategies for handling large volumes of product, including warehousing, shipping, and managing orders.
Module 8: Strategic Partnerships and Royalties
A crucial aspect of the SayPro business model is the collaboration with strategic partners in the manufacturing process.
- Understanding Strategic Partnerships:
- Explanation of the various stakeholders involved in the production chain, including suppliers, manufacturers, and distributors.
- Role of Royalties in the Production Process:
- The royalty structure for the production and sale of plastic chairs.
- How partners contribute to the manufacturing process and how SayPro benefits from royalty payments from bulk manufacturers.
- Sustainability and Ethical Considerations:
- How SayPro works with partners to ensure that environmental sustainability and ethical labor practices are maintained throughout the supply chain.
Conclusion: The SayPro Monthly Plastic Chairs Training Course gives participants a comprehensive understanding of the entire manufacturing process, from raw material selection to assembly and distribution. It also sheds light on the importance of strategic partnerships and royalties, ensuring that all stakeholders are aligned in producing high-quality, sustainable products. By fostering collaboration and ensuring strict quality control, SayPro maintains its position as a leader in the plastic chair manufacturing industry.
Leave a Reply