Your cart is currently empty!
SayPro Machine Maintenance in Plastic Chair Manufacturing
SayPro is a Global Solutions Provider working with Individuals, Governments, Corporate Businesses, Municipalities, International Institutions. SayPro works across various Industries, Sectors providing wide range of solutions.
Email: info@saypro.online Call/WhatsApp: Use Chat Button 👇
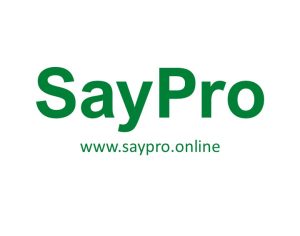
SayPro: Machine Maintenance in Plastic Chair Manufacturing
Maintaining manufacturing machines is crucial for ensuring smooth production, minimizing downtime, and maximizing the efficiency and lifespan of the equipment. In plastic chair manufacturing, machines such as injection molding machines, blow molding machines, and extrusion machines play a pivotal role in creating high-quality products. Regular maintenance and troubleshooting practices help prevent breakdowns and extend the life of these machines. Below are some best practices for maintaining and troubleshooting plastic manufacturing machines.
1. Routine Preventive Maintenance
Overview:
Preventive maintenance involves regular, scheduled checks and servicing to ensure that equipment continues to operate efficiently and reduce the risk of unexpected failures. This proactive approach helps to identify and fix issues before they result in costly downtime.
Best Practices:
- Scheduled Inspections: Set a maintenance schedule based on the manufacturer’s recommendations and production requirements. Machines should be inspected daily, weekly, or monthly depending on usage. Key components to check include:
- Hydraulic systems
- Cooling systems
- Drive motors
- Hopper and feed mechanisms
- Lubrication: Regularly lubricate moving parts such as screws, bearings, and gears to reduce friction and prevent premature wear. Proper lubrication also helps maintain smooth machine operation.
- Tip: Use the correct type and amount of lubricant specified in the machine’s manual to avoid overuse or contamination.
- Cleaning: Keeping machines clean is essential for preventing dust, debris, and plastic residue from affecting performance. Cleaning should be done regularly to remove material build-up from the molding or extrusion processes, which can cause clogs, inconsistencies, and damage to the machine.
- Tip: Clean all vents, molds, and cooling systems after every production run.
- Filter Replacement: Regularly replace filters in hydraulic, cooling, and air systems to ensure efficient operation. Clogged filters can reduce performance and lead to overheating.
2. Calibration and Alignment
Overview:
Proper calibration and alignment of the machine ensure that the molds, heating elements, and other components are functioning at optimal performance, which is critical for producing high-quality plastic chair parts.
Best Practices:
- Mold Alignment: Check the alignment of molds to ensure even pressure distribution during molding. Misalignment can lead to defects such as uneven parts or flash (excess plastic).
- Tip: Use a dial indicator or laser alignment tool to check mold alignment and adjust accordingly.
- Temperature Calibration: Ensure that the temperature controllers are calibrated and maintain the correct temperature settings for the material being used (e.g., for injection molding, blow molding, and extrusion).
- Tip: Regularly verify the accuracy of temperature gauges to prevent overheating or underheating, which can affect product quality.
- Pressure and Speed Settings: Review the pressure and speed settings for molding and extrusion processes to maintain consistency in material flow and part production. Misconfigured settings can cause defects in the final product or machine malfunctions.
- Tip: Regularly check the machine’s pressure gauges and adjust to maintain optimal performance.
3. Wear and Tear Management
Overview:
All manufacturing machines experience wear and tear over time, especially with components such as screws, nozzles, molds, and seals. Timely replacement of worn-out parts is critical for preventing costly repairs and maintaining consistent production quality.
Best Practices:
- Monitor High-Wear Components: Components like injection molding screws, mold cavities, and nozzle tips are prone to wear. Regularly inspect these parts for signs of damage such as cracks, wear marks, or material erosion.
- Tip: Keep an inventory of critical spare parts for quick replacement to minimize downtime.
- Replace Worn Seals: Seals and gaskets in machines can wear out over time, leading to air or fluid leaks. Replace seals as part of routine maintenance to maintain proper pressure and prevent material contamination.
- Tip: Use high-quality seals to reduce the frequency of replacements.
- Check and Replace Filters and O-Rings: Filters and O-rings should be checked regularly for damage and replaced as needed to ensure a clean, smooth operation. Damaged seals can lead to contamination of materials or hydraulic fluid, affecting product quality and machine efficiency.
4. Troubleshooting Common Issues
Overview:
Even with regular maintenance, issues can still arise with manufacturing machines. Knowing how to troubleshoot common problems quickly can prevent prolonged downtime and reduce repair costs. Below are some common issues that may arise and how to address them.
Common Issues and Solutions:
- Machine Not Starting:
- Possible Causes: Electrical issues, tripped circuit breaker, or malfunctioning power supply.
- Solutions:
- Check the electrical connections and ensure the circuit breaker is not tripped.
- Inspect the power supply and control panel for signs of damage or malfunction.
- Inconsistent Injection Pressure (for Injection Molding Machines):
- Possible Causes: Blocked or worn-out nozzles, clogged heating elements, or incorrect machine settings.
- Solutions:
- Clean and inspect the nozzle and heating elements for blockages.
- Verify that pressure settings are calibrated correctly.
- Check for worn-out seals or damaged valves in the injection system.
- Plastic Overflow or Flashing:
- Possible Causes: Excessive pressure, improper mold alignment, or damaged mold components.
- Solutions:
- Check mold alignment and adjust to ensure even pressure distribution.
- Ensure the machine is not over-pressurizing, and adjust the pressure settings if needed.
- Inspect the mold for wear and tear, and replace worn components.
- Uneven Cooling (for Blow Molding):
- Possible Causes: Clogged cooling channels, incorrect cooling temperature settings, or uneven mold temperature.
- Solutions:
- Inspect and clean cooling channels to ensure there is no blockage.
- Adjust cooling settings to ensure uniform temperature distribution across the mold.
- Check that the mold is evenly heated and cooled to prevent warping.
- Extrusion Problems (for Extrusion Machines):
- Possible Causes: Material inconsistency, blocked die, or damaged drive motors.
- Solutions:
- Ensure that the raw material is free of contaminants and has the correct composition.
- Clean the extrusion die to remove any blockages or build-up.
- Inspect drive motors for proper operation, and replace any faulty parts.
5. Record Keeping and Data Analysis
Overview:
Accurate record-keeping of maintenance activities, machine performance, and any troubleshooting interventions is essential for tracking machine health and improving efficiency over time.
Best Practices:
- Maintenance Logs: Keep detailed logs of all preventive maintenance tasks performed, including inspections, lubrication, parts replacements, and calibrations. This ensures consistency and helps identify patterns of wear or recurring issues.
- Tip: Use digital platforms or software to track maintenance schedules and machine performance.
- Performance Data Analysis: Collect data on machine performance, such as production rates, downtime, and defect rates. Analyzing this data can identify recurring problems or areas where maintenance needs to be improved.
- Tip: Use predictive maintenance software that can monitor machine conditions in real-time and provide alerts for potential issues before they occur.
Conclusion
Effective machine maintenance is critical to ensuring long-term efficiency and minimizing downtime in plastic chair manufacturing. By implementing best practices such as regular preventive maintenance, calibration, monitoring wear and tear, troubleshooting common issues, and keeping detailed records, manufacturers can keep their equipment running smoothly. With these practices, they can maximize machine lifespan, improve production efficiency, and consistently produce high-quality plastic chairs.
Leave a Reply