Your cart is currently empty!
SayPro Inventory and Resource Management: Oversee inventory management, ensuring the availability and proper handling of materials, equipment, and supplies.
SayPro is a Global Solutions Provider working with Individuals, Governments, Corporate Businesses, Municipalities, International Institutions. SayPro works across various Industries, Sectors providing wide range of solutions.
Email: info@saypro.online Call/WhatsApp: Use Chat Button 👇
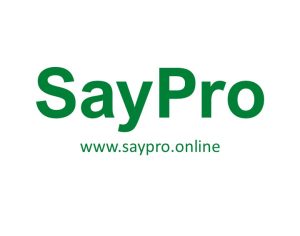
SayPro: Inventory and Resource Management – Overseeing Inventory Management, Ensuring Availability, and Proper Handling of Materials, Equipment, and Supplies
Effective inventory and resource management is vital to the success of any event or project, particularly when overseeing multiple moving parts such as materials, equipment, and supplies. By ensuring proper handling, organization, and tracking of inventory, SayPro can minimize waste, reduce the risk of shortages, and enhance the efficiency of operations. This process involves careful planning, regular monitoring, and strategic coordination to ensure that all materials and resources are available when needed and are handled properly.
The following is a comprehensive guide on how SayPro can oversee inventory management for events, projects, or any organizational needs, ensuring the smooth operation of activities.
1. Understanding Inventory and Resource Needs
A. Identify Inventory Categories
The first step in managing inventory is to clearly categorize the materials, equipment, and supplies needed. These categories will help in the organization and tracking of inventory, making it easier to manage.
- Materials: This includes consumables, promotional items, documents, brochures, or giveaways.
- Equipment: All physical assets that are reusable for events, such as sound systems, stages, projectors, AV equipment, furniture (chairs, tables), tents, and decor items.
- Supplies: Items that are necessary for day-to-day operations, such as office supplies, cleaning products, safety gear, first aid kits, and personal protective equipment (PPE).
- Vendor/Partner Materials: Items required by vendors or partners to set up their booths or services (e.g., tents, tables, signage).
B. Determine Quantities and Specifications
- Forecast quantities: Estimate the quantity of each material or equipment needed based on the expected number of attendees or the scale of the event. For example, how many chairs, tables, or safety supplies are needed per area or per activity.
- Specifications: Define the specifications for each item, including the size, quality, and type required for the event. This is particularly important for items like AV equipment, furniture, or branded materials.
2. Inventory Tracking and Management System
A. Set Up an Inventory Tracking System
A central inventory management system is essential for tracking all materials, equipment, and supplies. This could be a manual system (spreadsheet) for small-scale operations or an automated inventory software for large-scale events and projects.
- Create a master inventory list: Compile a comprehensive list of all materials, equipment, and supplies, detailing quantities, suppliers, delivery schedules, and costs.
- Barcode scanning or RFID tags: For larger or more complex inventories, implementing barcode scanning or RFID technology can streamline tracking and updates.
- Cloud-based inventory management: Utilize software that allows team members to access and update inventory information in real-time, ensuring that data is always accurate and current.
B. Track Items from Acquisition to Event Use
- Monitor purchasing: As materials and supplies are acquired, they should be logged into the inventory system. Each item should be tracked from procurement to delivery and eventual usage.
- Assign locations: Assign specific storage locations for materials and equipment to prevent confusion during event setup or resource allocation. This could involve warehouse shelves, storage containers, or even on-site designated areas for easy access.
- Track usage: As materials or supplies are used (such as decorations, flyers, or consumables), ensure they are properly logged, and their availability is updated in the inventory system.
3. Procurement and Replenishment Planning
A. Establish Supplier Relationships
To ensure smooth procurement, it’s important to maintain reliable supplier relationships:
- Vendor selection: Establish relationships with trusted suppliers and vendors for the materials and supplies required. This can include purchasing event-specific supplies, office supplies, or specialized equipment.
- Long-term contracts: For regular events, consider establishing long-term agreements with suppliers to ensure pricing consistency, priority access to stock, and timely deliveries.
- Backup suppliers: Identify backup suppliers or vendors in case of delays or shortages from primary sources.
B. Inventory Replenishment
- Monitor inventory levels: Regularly review the inventory to identify low stock levels of essential materials and equipment. For example, track the number of programs, brochures, or sound equipment available for events.
- Establish reorder points: Set thresholds that trigger automatic reordering or procurement. For instance, if the stock of event chairs drops below a certain number, the inventory system should notify the team to reorder.
- Order lead times: Consider the lead times for ordering and receiving materials. Order non-perishable items (such as banners, furniture, and tech equipment) well in advance, while consumables (such as food or brochures) can be replenished closer to the event date.
4. Storage and Handling of Materials
A. Organize and Label Storage Areas
Proper storage and handling of materials and equipment is essential to ensure items are not lost, damaged, or difficult to access when needed.
- Designate storage areas: Allocate specific storage spaces for each category of materials and supplies. For instance, one area for signage, another for technical equipment, and another for event-related documents.
- Labeling systems: Use clear, color-coded labels, tags, or bins to ensure materials are easy to identify and retrieve. Label items with the event or project name, contents, and handling instructions.
- Security measures: Implement security measures, including lockable storage areas for high-value equipment, to prevent theft or misuse of materials.
B. Handling and Protection of Sensitive Equipment
- Fragile items: Handle delicate equipment, such as AV equipment or electronics, with extra care. Ensure that packing materials (such as padded cases, bubble wrap, or foam) are used for storage and transportation.
- Preventative maintenance: Regularly inspect and maintain equipment, such as projectors, speakers, or lighting, to ensure they are in working condition prior to events. This can prevent technical failures during an event.
5. Delivery and Distribution Management
A. Logistics of Delivery to Event Sites
- Pre-event delivery scheduling: Confirm that all materials, equipment, and supplies are delivered to the event venue on time. Create a schedule for deliveries and coordinate with transportation vendors to avoid delays.
- Verify the list of deliveries: Cross-reference the incoming deliveries against the inventory system to ensure everything ordered has arrived. If any items are missing or damaged, follow up with the supplier or adjust event plans as necessary.
B. On-Site Resource Allocation
- Assign resources to specific areas: As materials arrive on-site, allocate them to their designated event areas (e.g., vendor booths, registration desk, performance stage). This can be coordinated by the event team to ensure that each area has the necessary supplies.
- Monitor resource usage during the event: Track materials as they are used during the event. For example, if there are changes in attendee numbers, more seating or promotional materials might need to be delivered or replenished during the event.
6. Post-Event Inventory and Resource Evaluation
A. Post-Event Inventory Count
- Inventory check: After the event, conduct a thorough inventory check to identify materials and equipment that were used, returned, or lost. This helps track the condition of items and prepares for future events.
- Return unused supplies: Ensure any unused materials, such as promotional items, brochures, or vendor supplies, are properly stored or returned to suppliers if needed. For rental equipment, arrange for timely pick-up.
B. Resource Evaluation and Feedback
- Assess the condition of items: Inspect the condition of all rented or owned equipment to determine if it requires repairs or replacement before the next use.
- Document lessons learned: Collect feedback from the event team, vendors, and participants to identify any resource-related challenges during the event. Use this information to refine the inventory management process and avoid issues in the future.
7. Continuous Improvement of Inventory Practices
A. Data Analytics for Better Resource Allocation
- Analyze usage trends: Use data collected from previous events to assess which materials, equipment, and supplies were most in demand and which were underutilized. This can guide future purchasing decisions and resource allocation.
- Forecasting future needs: Based on past events, develop forecasts for future inventory needs to prevent over-purchasing or understocking.
B. Regular System Updates and Audits
- System updates: Keep the inventory management system up to date, ensuring that all information is accurate and reflective of actual inventory levels.
- Regular audits: Conduct periodic audits of materials and supplies to ensure proper handling, security, and accuracy of records. This will help identify any inefficiencies or discrepancies in the system.
Conclusion
By implementing a structured inventory and resource management system, SayPro can ensure the availability, proper handling, and timely delivery of all materials, equipment, and supplies required for events and projects. A thorough, proactive approach to managing inventory not only reduces waste and prevents shortages but also enhances operational efficiency and ensures that resources are utilized effectively.
This level of organization will help ensure that SayPro’s events are executed smoothly, with all materials and supplies available as needed, and no critical resources overlooked.
Leave a Reply