Your cart is currently empty!
SayPro Follow-Up Workshops
SayPro is a Global Solutions Provider working with Individuals, Governments, Corporate Businesses, Municipalities, International Institutions. SayPro works across various Industries, Sectors providing wide range of solutions.
Email: info@saypro.online Call/WhatsApp: Use Chat Button ๐
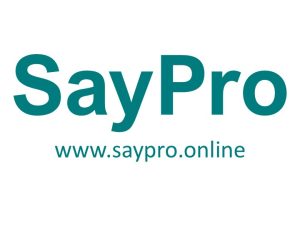
SayPro Monthly January SCSPR-98: Collaboration for Continuous Improvement and Follow-Up Workshops
Collaboration with other departments within SayPro is essential to ensure the continuous enhancement of the Plastic Chairs Manufacturing Training Program. By working together across various departments, SayPro can combine expertise, resources, and innovative ideas to improve training content, delivery methods, and provide valuable follow-up workshops for participants.
Hereโs a detailed approach to collaborating with other SayPro departments to make improvements and offer follow-up workshops:
1. Inter-Departmental Collaboration for Program Improvements
By collaborating with different departments, SayPro can leverage a range of expertise to ensure that the training program stays relevant, up-to-date, and high-quality.
A. Collaboration with the Product Development Team
The Product Development Team can provide valuable insights into the latest trends in plastic chair design, material innovation, and new manufacturing techniques. Working closely with them will help ensure that the course content is always aligned with the latest industry advancements.
- Actions:
- Integrate Latest Innovations: Regularly update the training curriculum with new trends, such as emerging plastic materials or sustainable manufacturing techniques, based on feedback from the Product Development Team.
- Incorporate New Products: If new types of plastic chairs or machinery are being developed, include those in the course content to help participants stay current with cutting-edge industry practices.
B. Collaboration with the Marketing and Communications Team
The Marketing and Communications Team can help design promotional materials and support the launch of the course, ensuring it reaches the right audience. Additionally, they can assist in gathering testimonials and feedback from participants to promote future iterations.
- Actions:
- Promote Workshops and New Courses: Work together to design engaging marketing materials (e.g., emails, social media posts, flyers) that highlight key features of the training program and attract participants.
- Leverage Testimonials: Use positive feedback from past participants to create promotional materials that showcase the course’s success and build trust with potential future learners.
C. Collaboration with the IT and Technical Support Team
The IT and Technical Support Team plays a critical role in ensuring the SayPro course platform runs smoothly, provides a seamless user experience, and addresses technical issues that may arise during the course.
- Actions:
- Improve Platform Usability: Work with IT to address any technical difficulties that participants face during the course, such as login issues, video buffering, or course navigation challenges.
- Incorporate Virtual Simulations: Develop interactive virtual simulations or 3D modeling tools in collaboration with IT to give participants hands-on practice with machinery or manufacturing processes.
D. Collaboration with the HR and Training Development Team
The HR and Training Development Team can assist in evaluating the effectiveness of the course and providing ongoing support for participants.
- Actions:
- Monitor Participant Progress: Collaborate with HR to track how participants progress through the training course and offer targeted support for those who may need additional help.
- Design Career Pathways: Work with HR to design pathways for participants to progress within SayPro after completing the course, ensuring they feel encouraged to apply what they’ve learned in real-world scenarios.
E. Collaboration with the Quality Control (QC) Team
The Quality Control Team can share best practices in ensuring the quality of products, which is a key element of the manufacturing process. Their insights will be valuable in reinforcing the importance of quality during the training course.
- Actions:
- Incorporate Quality Standards: Integrate quality control standards into the training program, emphasizing the importance of consistent quality in manufacturing plastic chairs.
- Provide Hands-On QC Demonstrations: Develop practical, real-life scenarios where participants can assess and test the quality of plastic chairs using the methods employed by the QC team.
2. Offering Follow-Up Workshops for Participants
Offering follow-up workshops is a great way to enhance learning and address any ongoing needs that participants may have after completing the training course. These workshops provide an opportunity for hands-on practice, advanced topics, and in-depth discussions on areas where participants need further improvement.
A. Identify Topics for Follow-Up Workshops
Based on the feedback from participants, instructors, and department collaboration, identify key areas where additional workshops would be beneficial.
- Advanced Manufacturing Techniques: For participants who want to deepen their knowledge, offer workshops that cover more advanced topics in plastic chair manufacturing, such as advanced machine settings or troubleshooting.
- Troubleshooting and Maintenance Workshops: Offer a practical workshop that focuses on troubleshooting common machine problems, machine maintenance, and preventive techniques to ensure longevity and optimal performance.
- Quality Control and Inspection: Focus on practical QC techniques and how to inspect finished products effectively to meet industry standards. This could include hands-on testing, measuring, and reporting.
- Sustainability in Manufacturing: Organize a session on sustainable practices in the plastic chair industry, such as using recycled materials, reducing waste, and adhering to environmental standards.
B. Designing Interactive and Hands-On Follow-Up Workshops
To ensure participants gain practical, applicable knowledge, structure the follow-up workshops to be highly interactive and hands-on.
- Live Demonstrations: In collaboration with the Product Development Team, offer live demonstrations of new machines or production processes, allowing participants to interact with the equipment and ask questions.
- Workshops with Simulations: Offer virtual simulations for processes like injection molding or blow molding, so participants can practice without the risk of machine downtime or material waste.
- Collaborative Group Projects: Encourage group projects that involve problem-solving in real-world manufacturing scenarios. This can include troubleshooting machine issues, optimizing the production line, or designing a new chair model.
C. Incorporating Industry Experts
To add depth to the follow-up workshops, consider inviting industry experts to provide valuable insights into emerging trends, new technologies, or advanced manufacturing methods.
- Guest Speakers: Collaborate with external experts in plastic chair manufacturing or sustainable materials to provide talks or workshops that add new perspectives to the course.
- Industry Visits: Organize visits to manufacturing plants or research facilities where participants can see industry best practices in action and learn directly from professionals in the field.
3. Ongoing Feedback and Continuous Improvement for Follow-Up Workshops
Just as with the initial course, gathering feedback after each follow-up workshop is critical to ensure they are meeting participant needs and expectations.
- Post-Workshop Surveys: Send out surveys after each follow-up session to gather feedback on the content, instructors, and overall experience.
- Evaluate Effectiveness: Use the feedback to assess whether the follow-up workshops addressed participants’ questions, provided deeper insights, and helped them apply the skills they learned.
- Refine Future Workshops: Continuously improve the design and delivery of follow-up workshops based on participant feedback, ensuring that they stay relevant and effective.
4. Encouraging Long-Term Engagement and Learning
The goal of follow-up workshops is to build a long-term relationship with participants, fostering ongoing learning and professional development.
- Alumni Network: Create an alumni network for participants who have completed the training. This could include access to exclusive workshops, job opportunities, and peer networking.
- Continual Learning Resources: Offer continued access to course materials, additional resources, and updated content so that participants can keep up with the latest industry advancements.
- Advanced Certifications: Provide advanced certification programs or specialization tracks for participants who wish to further develop their skills in specific areas, such as machine optimization or sustainable production.
5. Conclusion
By collaborating with other SayPro departments and offering valuable follow-up workshops, SayPro can continuously improve the Plastic Chairs Manufacturing Training Program and ensure that participants are well-equipped with the latest knowledge, skills, and industry best practices. This interdepartmental synergy and ongoing support will not only enhance the quality of the training but also help build a strong community of well-trained professionals in the plastic manufacturing industry.
Leave a Reply