Your cart is currently empty!
SayPro Engage in logistical planning exercises
SayPro is a Global Solutions Provider working with Individuals, Governments, Corporate Businesses, Municipalities, International Institutions. SayPro works across various Industries, Sectors providing wide range of solutions.
Email: info@saypro.online Call/WhatsApp: Use Chat Button 👇
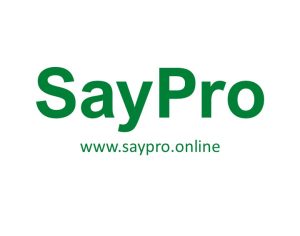
Establish the Logistics Planning Framework
- Define the scope of the exhibition: Identify the exhibition’s scale (e.g., local, regional, or international) and the specific service products or solutions SayPro will showcase.
- Set clear objectives for logistics: Determine the logistics goals, such as ensuring timely delivery of materials, smooth on-site operations, and effective vendor coordination to create a successful event experience.
- Design a logistics timeline: Create a detailed timeline of key milestones leading up to, during, and after the exhibition, including deadlines for vendor coordination, shipping, inventory, and setup.
2. Simulate Vendor Coordination Scenarios
- Vendor selection exercise: Simulate the process of selecting and contracting vendors, such as those providing booth construction, catering, audio-visual equipment, and promotional material printing. Consider factors like cost, quality, and service reliability.
- Create vendor communication plans: Develop mock communication strategies for keeping vendors informed about event schedules, requirements, and changes. This can include email templates, checklists, and reminders.
- Assign roles and responsibilities: Assign specific roles to the logistics team, such as vendor liaison, transportation coordinator, or on-site operations manager, and outline their tasks in each scenario.
- Plan contingency strategies: Simulate scenarios where vendors may face challenges, such as delays in delivery, equipment malfunction, or last-minute cancellations. Develop backup plans and mitigation strategies for these situations.
- Conduct mock meetings with vendors: Role-play mock meetings where team members simulate discussions with vendors to review timelines, contracts, and specific exhibition needs.
3. Inventory Management Exercises
- Create an inventory list: Develop a comprehensive inventory of all items needed for the exhibition, such as booth materials, product samples, marketing collateral, signage, and promotional giveaways.
- Simulate inventory tracking: Practice using inventory management tools or software to track the arrival, distribution, and utilization of items. Ensure that quantities are accurate and there is no stock depletion during the event.
- Develop packing and shipping plans: Plan the logistics of packing, labeling, and shipping the inventory to the exhibition venue. Simulate scenarios where items may get lost or damaged during shipping and how to handle such situations.
- Conduct mock inventory checks: Create a mock scenario in which the inventory team conducts an on-site check to ensure all materials have arrived and are in the correct quantities. Practice the process of resolving discrepancies.
- Establish on-site inventory flow: Simulate the arrival and distribution of materials on the day of the event. Determine how to manage the flow of materials to the booth and ensure everything is properly set up in time for the exhibition.
4. On-Site Operations Planning
- Develop an event setup checklist: Create a checklist outlining all tasks for setting up the exhibition booth, including booth assembly, product displays, signage, audio-visual equipment setup, and arranging promotional materials.
- Simulate booth layout and design adjustments: Role-play scenarios where the booth layout needs to be modified due to unforeseen circumstances, such as space limitations, technical issues, or last-minute changes.
- Coordinate team members on-site: Assign specific tasks to team members during event setup, such as managing booth design, product placement, arranging demo stations, or overseeing visitor registration.
- Create a staff scheduling plan: Develop a schedule for staff working at the booth, covering all hours of the exhibition. Include roles like customer service, product demonstrations, lead collection, and general assistance.
- Simulate handling of operational challenges: Conduct mock exercises to simulate issues that may arise during the event, such as equipment failures, customer complaints, or logistical delays. Develop strategies for resolving these challenges in real-time.
- Plan for health and safety compliance: Ensure that on-site operations follow all safety regulations, such as emergency evacuation routes, fire safety protocols, and crowd control measures. Simulate situations that require swift response to maintain safety.
5. Vendor and Staff Coordination During the Event
- Simulate communication with vendors during the event: Role-play scenarios where real-time communication with vendors is necessary for problem-solving or adjustments. Practice quickly resolving issues like equipment malfunctions, unexpected deliveries, or last-minute booth changes.
- Establish clear lines of communication: Set up a communication system for event staff and vendors (e.g., walkie-talkies, phones, or a messaging platform) to facilitate quick response times during the exhibition.
- Simulate on-site troubleshooting: Practice handling on-the-spot issues, such as missing materials, damaged equipment, or last-minute booth adjustments. Ensure that team members can act efficiently under pressure.
6. Shipping and Transportation Planning
- Simulate transport and shipping logistics: Plan the transportation process for all materials and equipment, including securing transportation providers, creating a loading and unloading plan, and coordinating the delivery timeline.
- Track shipping progress: Use simulated tracking tools to monitor the shipping process in real-time, ensuring that shipments arrive on time and are correctly labeled. Practice handling delays or issues during transit.
- Organize post-event logistics: Plan the transportation and shipment of materials after the exhibition, including coordinating the return of unsold products, promotional materials, and booth setup components.
7. Post-Event Breakdown and Clean-Up Procedures
- Develop a teardown plan: Create a comprehensive plan for breaking down the booth and packing materials at the end of the exhibition. Simulate scenarios where the teardown needs to be expedited or where materials get lost.
- Coordinate logistics for packing: Organize the packing process, ensuring that all items are properly packed, labeled, and transported back to the storage facility or office.
- Assess post-event team debriefing: Schedule a debriefing session after the exhibition where the logistics team can discuss what worked well, what challenges arose, and how to improve for future events.
8. Practice Time Management and Deadline Adherence
- Simulate time-sensitive scenarios: Develop scenarios in which the team has tight deadlines or must adhere to strict timelines for deliveries, setups, or breakdowns. Practice staying on track while managing multiple tasks.
- Develop time buffers: Create contingency plans with buffer times built in to ensure the team is not stressed or rushed during crucial phases, such as shipping or setup.
9. Evaluate the Logistics Simulation
- Review team performance: After completing the simulation exercises, conduct a review to evaluate how well the team handled the logistics challenges. Identify strengths and areas for improvement.
- Gather feedback: Collect feedback from team members on what went well and what challenges were encountered during the logistics planning exercise.
- Document lessons learned: Create a report or presentation that outlines key takeaways, solutions to common logistical problems, and recommendations for improving future logistics planning.
10. Continuous Improvement
- Implement improvements based on simulation outcomes: Use the insights gathered from the exercise to refine SayPro’s logistics processes, such as vendor coordination, inventory management, or on-site operations.
- Integrate logistics planning into overall exhibition strategy: Ensure that logistics planning becomes an integral part of SayPro’s strategy for managing future exhibitions and events.
By completing these tasks, SayPro’s team will be better prepared to handle real-world logistics challenges, ensuring smooth operations, effective vendor coordination, and a successful exhibition.
Leave a Reply