Your cart is currently empty!
SayPro Design Training Material Prepare training materials that include detailed reports
SayPro is a Global Solutions Provider working with Individuals, Governments, Corporate Businesses, Municipalities, International Institutions. SayPro works across various Industries, Sectors providing wide range of solutions.
Email: info@saypro.online Call/WhatsApp: Use Chat Button 👇
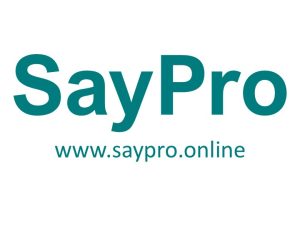
SayPro Design Training Material
Training on Repair Documentation: Monthly March Generator Repair Report by SCDR
Introduction to SayPro Repair Documentation Process
The purpose of this training is to help participants become proficient in documenting repair activities for SayPro’s monthly generator repairs. The primary focus will be on learning how to create clear, accurate, and standardized reports that adhere to SayPro’s repair documentation format.
Training Material Overview
This material will guide participants through the following:
- Repair Documentation Process
- Overview of repair reports
- Importance of clear documentation
- Standard formatting conventions
- Sample Case Studies
- Real-world scenarios for practice
- Repair Scenarios
- Common generator repair situations
- Repair Report Template
- Explanation of the required fields and structure
1. Repair Documentation Process: Overview & Importance
Repair documentation serves as the official record of work done on a generator and provides stakeholders (e.g., technicians, managers, and clients) with the detailed information they need. Accurate documentation ensures the repair process is traceable, compliant with industry standards, and facilitates decision-making for future maintenance.
Why Repair Documentation is Critical:
- Accountability: A documented repair ensures everyone is on the same page about what was fixed, how, and why.
- Quality Assurance: Ensures that repairs meet company and regulatory standards.
- Troubleshooting: Past reports can guide future repairs by providing insights into recurring issues.
- Communication: Repair reports serve as an important communication tool between technicians, customers, and management.
- Compliance: Some repair processes need to adhere to strict industry regulations, so documentation ensures compliance.
2. Sample Case Studies: Real-World Scenarios
Case Study 1: Generator Fails to Start After Routine Maintenance
- Problem: Generator fails to start after routine maintenance was conducted.
- Step-by-step repair:
- Diagnosis: Technician notices no fuel is reaching the engine despite full tanks.
- Repair Steps:
- Checked fuel lines and filters for blockages.
- Replaced clogged fuel filter.
- Inspected fuel pump for leaks.
- Test-started the generator successfully.
- Documentation:
- Diagnosis: “Fuel flow obstruction.”
- Repairs Made: “Replaced fuel filter and checked fuel lines for leaks.”
- Outcome: “Generator started successfully after replacement.”
**Case Study 2: Generator Overheating
- Problem: Generator is overheating during operation.
- Step-by-step repair:
- Diagnosis: Technician observes that coolant levels are low, and the radiator fan is not functioning.
- Repair Steps:
- Refilled coolant to optimal levels.
- Replaced faulty radiator fan.
- Checked all hoses and seals for leakage.
- Tested generator for overheating after repair.
- Documentation:
- Diagnosis: “Low coolant levels and malfunctioning fan.”
- Repairs Made: “Refilled coolant, replaced radiator fan, and checked coolant lines for leaks.”
- Outcome: “Generator operated within normal temperature range after repairs.”
3. Common Generator Repair Scenarios
Scenario 1: Generator Not Generating Power
- Possible Causes:
- Faulty alternator
- Worn-out stator or rotor
- Broken wiring
- Repair Steps:
- Inspect alternator and stator.
- Check electrical connections for continuity.
- Replace faulty components as required.
- Test generator output.
Scenario 2: Engine Misfires During Start-up
- Possible Causes:
- Insufficient fuel supply
- Ignition system failure
- Dirty fuel injectors
- Repair Steps:
- Inspect fuel injectors and clean or replace them.
- Check ignition system components (e.g., spark plugs, wiring).
- Test and diagnose further if necessary.
Scenario 3: Excessive Noise or Vibration During Operation
- Possible Causes:
- Loose parts or mounts
- Misaligned components
- Faulty bearings
- Repair Steps:
- Tighten and secure all loose parts.
- Inspect the alignment of the generator.
- Replace any faulty bearings.
- Conduct vibration testing.
4. Repair Report Template: Structure & Explanation
A repair report should be thorough, concise, and organized in a standardized format. The following sections should be included in each repair report:
SayPro Monthly Generator Repair Report Template
1. Header Section
- Report ID: Unique identifier for the repair report.
- Report Date: Date the repair was completed.
- Generator ID: The unique identifier for the generator being serviced.
- Repair Technician Name: Name of the technician performing the repair.
- Location: Site or facility where the repair was done.
Example:
- Report ID: 2025-03-001
- Report Date: March 10, 2025
- Generator ID: GEN-0002345
- Repair Technician Name: John Doe
- Location: SayPro Facility, New York
2. Problem Description
- A brief summary of the problem observed with the generator.
- Example: “Generator failing to start after routine maintenance.”
3. Diagnostic Steps Taken
- Outline the diagnostic steps performed to identify the cause of the issue.
- Example:
- Checked fuel levels and fuel filter for blockages.
- Tested ignition system.
- Conducted load tests.
4. Repairs Performed
- Detailed description of the repairs carried out.
- Be specific about parts replaced, components tested, and actions taken.
- Example:
- Replaced clogged fuel filter.
- Inspected and cleaned fuel injectors.
- Replaced faulty spark plugs.
5. Parts Replaced or Serviced
- List the parts replaced or serviced during the repair.
- Include part numbers, quantity, and cost if applicable.
- Example:
- Fuel filter (Part No. 33452) – 1 unit
- Spark plugs (Part No. 112233) – 2 units
6. Test Results & Outcome
- Document the outcome of testing after repairs.
- Was the issue resolved? Any additional observations?
- Example: “Tested generator; started without issue. Load tests successful with no overheating.”
7. Recommendations for Future Maintenance
- If applicable, provide any suggestions for future care or areas that may require attention.
- Example: “Recommend replacing the fuel filter every 6 months to avoid clogs.”
8. Technician’s Comments
- A brief note from the technician regarding the repair process, challenges, or observations.
- Example: “Repair completed as per protocol. No further issues identified.”
9. Signature
- Signature of the technician who performed the repair.
- Signature of the supervisor or manager who reviewed the report.
5. Example of a Completed Repair Report
SayPro Monthly Generator Repair Report
Report ID: 2025-03-001
Report Date: March 10, 2025
Generator ID: GEN-0002345
Repair Technician Name: John Doe
Location: SayPro Facility, New York
Problem Description: Generator failing to start after routine maintenance.
Diagnostic Steps Taken:
- Checked fuel levels and fuel filter for blockages.
- Tested ignition system and fuel pump.
Repairs Performed:
- Replaced clogged fuel filter.
- Inspected and cleaned fuel injectors.
- Replaced faulty spark plugs.
Parts Replaced:
- Fuel filter (Part No. 33452) – 1 unit
- Spark plugs (Part No. 112233) – 2 units
Test Results & Outcome:
- Generator started without issue.
- Load tests successful with no overheating.
Recommendations for Future Maintenance:
- Replace fuel filter every 6 months to avoid future clogs.
Technician’s Comments:
- Repair completed as per protocol. No further issues identified.
Signatures:
Technician: John Doe
Supervisor: Jane Smith
Conclusion
By the end of this training, participants should have a strong understanding of the repair documentation process and be able to create clear, comprehensive repair reports. These skills are crucial to ensuring that SayPro’s generator maintenance is conducted efficiently and in compliance with company standards.
Leave a Reply