Your cart is currently empty!
SayPro Course Facilitation Deliver the training course, ensuring clarity and thorough understanding of plastic chair manufacturing processes
SayPro is a Global Solutions Provider working with Individuals, Governments, Corporate Businesses, Municipalities, International Institutions. SayPro works across various Industries, Sectors providing wide range of solutions.
Email: info@saypro.online Call/WhatsApp: Use Chat Button 👇
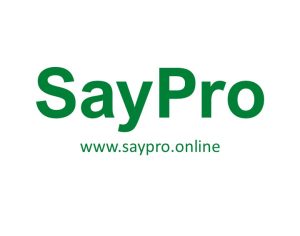
Course Facilitation Plan: SayPro Plastic Chair Manufacturing Process
Objective: The primary goal of this course is to provide participants with a comprehensive understanding of the plastic chair manufacturing process. By the end of the training, attendees should be able to grasp each step involved in manufacturing plastic chairs, from raw material selection to the final product assembly, with a focus on efficiency, quality, and safety.
1. Introduction to Plastic Chair Manufacturing (30 minutes)
- Overview of the Industry:
- Begin with a brief introduction to the global plastic chair manufacturing industry, highlighting its significance in various sectors such as residential, commercial, and industrial use.
- Discuss the evolution of plastic chair designs, materials, and technologies.
- Course Expectations:
- Outline what participants can expect to learn.
- Encourage interaction throughout the course by inviting questions and providing opportunities for hands-on practice.
- Safety Protocols:
- Emphasize safety guidelines, as manufacturing environments can involve the handling of heavy machinery and raw materials.
- Discuss protective gear and safety procedures, including the importance of following manufacturer instructions.
2. Materials and Components (45 minutes)
- Types of Plastics Used:
- Provide an in-depth look at the different types of plastics used in manufacturing chairs (e.g., polypropylene, polyethylene, PVC, etc.).
- Discuss the properties of these materials, such as durability, flexibility, and resistance to UV degradation.
- Additives and Reinforcements:
- Explain how additives like UV stabilizers, colorants, and flame retardants enhance the quality of the chairs.
- Discuss the use of fillers and reinforcements (like fiberglass) in ensuring strength and longevity.
- Other Components:
- Introduce other essential components in chair manufacturing, such as fasteners, screws, and connectors, and their role in the final product.
Interactive Activity:
- Have participants examine sample materials, identifying key differences in texture, weight, and flexibility.
3. The Manufacturing Process (1 hour)
- Design and Prototyping:
- Discuss the initial phase of design, including the creation of CAD (Computer-Aided Design) models and prototypes.
- Demonstrate how design influences chair comfort, aesthetic appeal, and ergonomics.
- Injection Molding Process:
- Provide a step-by-step explanation of the injection molding process, which is the most common method for producing plastic chairs.
- Break down each stage, including material heating, mold creation, injection, cooling, and ejection.
- Discuss the factors that affect the efficiency and quality of the process, such as mold design, temperature control, and cycle time.
- Other Manufacturing Methods:
- Mention other methods of production, such as blow molding and rotational molding, explaining when and why they are used.
- Highlight the advantages and disadvantages of each technique.
Visual Demonstration:
- If possible, show a short video or a live demonstration of the injection molding process in action to reinforce understanding.
4. Quality Control and Testing (45 minutes)
- Inspection Techniques:
- Explain the quality control measures in place to ensure that each chair meets the required standards.
- Discuss techniques like visual inspection, dimensional checks, and structural tests.
- Mechanical Testing:
- Review the types of mechanical tests used to ensure durability, such as weight tolerance, stress tests, and impact resistance.
- Discuss the importance of environmental testing to simulate exposure to sunlight, heat, and moisture.
- Product Certification:
- Describe the certifications that plastic chairs may need to achieve (e.g., ISO, BIFMA for commercial products).
- Emphasize the importance of meeting industry standards for safety and quality.
Interactive Activity:
- Organize a small hands-on session where participants can inspect sample chairs, identifying potential issues or defects, and suggesting solutions.
5. Final Assembly and Packaging (30 minutes)
- Assembly Process:
- Walk through the final steps of the production process, including how components (like legs, armrests, and seatbacks) are assembled.
- Discuss automation vs. manual labor in the final assembly process.
- Packaging and Shipping:
- Explain the role of packaging in protecting the chairs during transit and storage.
- Discuss eco-friendly packaging options and the importance of reducing environmental impact.
Hands-On Demonstration:
- If possible, allow participants to assemble a simple chair or component to better understand the assembly line.
6. Troubleshooting and Common Issues (30 minutes)
- Identifying Defects:
- Discuss common defects in plastic chair manufacturing, such as warping, discoloration, or cracks.
- Provide guidance on troubleshooting these issues during the production process.
- Preventive Measures:
- Share strategies for minimizing defects, including proper mold maintenance, temperature control, and material handling.
Q&A and Troubleshooting Exercise:
- Open the floor to questions and have participants work through case studies or examples of common manufacturing problems.
7. Sustainability and Future Trends (30 minutes)
- Eco-Friendly Manufacturing:
- Discuss current trends in sustainable plastic chair manufacturing, such as the use of recycled plastics and biodegradable materials.
- Explore innovations aimed at reducing the environmental impact of plastic chair production.
- Future of Plastic Chair Design:
- Speculate on future trends in plastic chair design, such as smart furniture, multi-functional designs, and the role of automation.
Interactive Discussion:
- Encourage participants to brainstorm ways to improve the sustainability of plastic chair manufacturing, considering materials, processes, and energy use.
8. Conclusion and Review (15 minutes)
- Recap Key Takeaways:
- Summarize the key points covered in the course, reinforcing the importance of each phase of the plastic chair manufacturing process.
- Encourage participants to continue exploring the topic through additional research or practical experience.
- Feedback and Evaluation:
- Provide a feedback form or conduct a quick survey to gauge the effectiveness of the course and areas for improvement.
- Certification:
- If applicable, issue certificates of completion and congratulate participants on their learning.
Course Delivery Methods:
- Lecture and Presentation: Use slides to present key concepts, supported by real-life examples and visuals.
- Demonstrations and Videos: Visual aids like videos or live demonstrations will help reinforce the theoretical aspects of the course.
- Interactive Sessions: Encourage hands-on activities, group discussions, and problem-solving exercises to keep the learning engaging.
Materials Needed:
- Projector or screen for presentations
- Samples of raw materials and finished products
- Tools for assembly exercises
- Safety equipment for practical demonstrations
- Feedback forms for post-course evaluation
Leave a Reply