Your cart is currently empty!
SayPro Conduct the Workshop Lead the session and walk
SayPro is a Global Solutions Provider working with Individuals, Governments, Corporate Businesses, Municipalities, International Institutions. SayPro works across various Industries, Sectors providing wide range of solutions.
Email: info@saypro.online Call/WhatsApp: Use Chat Button 👇
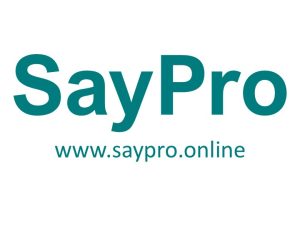
SayPro Workshop: Conducting the Generator Repair Report Training Session
The main goal of this session is to ensure participants understand the process of documenting generator repairs in a clear and detailed manner. By the end of the session, participants should be able to independently create accurate and comprehensive repair reports for any generator maintenance, troubleshooting, or repair work they perform.
Below is a detailed guide for conducting the workshop and leading the session effectively. The workshop will include demonstrations, discussions, and hands-on practice where participants will walk through the repair report process step-by-step.
Workshop Structure and Agenda
1. Introduction (15 minutes)
- Welcome and Icebreaker (5 minutes)
Begin the session by introducing yourself and welcoming the participants. Ask them to briefly introduce themselves (name, role, and experience) to set a comfortable tone for the workshop. Sample Icebreaker Prompt:
“Tell us your name, role, and one thing you hope to learn from this session.” - Overview of the Session (10 minutes)
Provide a clear outline of the workshop’s objectives and agenda:- Understanding the importance of detailed repair documentation.
- Key components of a repair report.
- Step-by-step walkthrough of creating a generator repair report.
- Troubleshooting tips and best practices for repair documentation.
2. Understanding Repair Documentation (20 minutes)
- Why Repair Reports Matter (5 minutes)
Start by explaining why detailed repair documentation is crucial:- Ensures that repairs are properly tracked and auditable.
- Provides a reference for future repairs and troubleshooting.
- Helps maintain transparency and accountability with customers or management.
- Protects both the technician and the organization by documenting the repairs performed.
- Key Components of a Generator Repair Report (15 minutes)
Walk through the main sections of a standard generator repair report. Each participant should have a template in front of them (whether printed or digital), and you should use a sample repair case to demonstrate how each section is completed. Key Components to Highlight:- Repair Report Header: Includes basic details like date, technician name, job number, and client information.
- Generator Details: Serial number, make, model, and any specific identifying information.
- Problem Description: A clear and concise description of the issue reported or observed with the generator.
- Diagnosis/Inspection: Document the diagnostic steps, tools used, and findings.
- Repair Work Performed: Detailed steps of the repair work performed, including parts replaced, repairs made, and any procedures followed.
- Parts and Materials Used: List all parts, materials, and consumables used during the repair.
- Time Spent: Total time spent on the repair (can include labor hours, troubleshooting time, etc.).
- Conclusion & Recommendations: A summary of the repair outcome and any recommendations for further maintenance or observation.
- Sign-Off and Client Confirmation: The technician’s and client’s signature to confirm the repair was completed and meets expectations.
3. Step-by-Step Walkthrough: Creating a Generator Repair Report (40 minutes)
This is the most crucial section of the workshop, where you guide participants through creating a repair report from start to finish. For this activity, you can use a real-world repair scenario that the participants can relate to.
Sample Scenario:
The generator in question is a 100kW diesel-powered unit, and the reported issue is that the generator won’t start. After inspection, it’s found that the fuel filter is clogged, and the battery is dead.
Step 1: Filling in the Header Section (5 minutes)
- Start by completing the repair report header: Name, date, customer, job number, etc.
- Ask the participants to fill in their own template header.
Step 2: Documenting the Problem (5 minutes)
- Walk through how to document the problem description: A clear, concise statement of the issue. Use the example:
“The generator fails to start when the ignition is turned on. The engine turns over, but there’s no fuel delivery.” - Ask participants to describe the problem for their generator repair scenario.
Step 3: Diagnosis and Inspection Process (10 minutes)
- Demonstrate the diagnosis and inspection process, explaining the tools used, the steps taken, and the key observations. For example:
- Diagnostic Steps: Check battery voltage, inspect fuel lines, test fuel injectors, check the fuel filter, etc.
- Inspection Results: “Battery voltage is 9.8V (low), fuel filter is clogged, fuel delivery system is compromised.”
- Ask participants to document their diagnostic findings based on the scenario you provided.
Step 4: Repair Work Performed (10 minutes)
- Go into detail about the repair process. Demonstrate how to document each step of the repair, including:
- Parts replaced (e.g., fuel filter, battery).
- Procedures followed (e.g., draining the fuel, replacing the fuel filter, charging/replacing the battery).
- Have participants document the repair steps for their own scenario.
Step 5: Parts and Materials Used (5 minutes)
- List and document all parts and materials used during the repair, including part numbers, quantities, and supplier details if applicable.
- Example: “Battery (Part #12345), Fuel Filter (Part #67890)”
- Ask participants to document the parts used in their repair.
Step 6: Time Spent (5 minutes)
- Explain how to document the time spent on each task, such as:
- Time spent diagnosing the problem.
- Time spent performing the repair work.
- Total time.
- Have participants estimate and record the time spent for their repair scenario.
Step 7: Conclusion and Recommendations (5 minutes)
- Demonstrate how to write a clear conclusion that summarizes the repair work and suggests any follow-up actions, such as:
- “Generator successfully repaired, and running at full capacity. Recommend regular maintenance every 6 months, including fuel system inspection.”
- Have participants write their conclusion and recommendation for their scenario.
Step 8: Sign-Off (Optional) (5 minutes)
- Explain the sign-off process, where both the technician and client sign to confirm that the repair has been completed and is satisfactory.
- Show how to include client feedback (if any), including additional work requests or observations.
4. Breakout Session: Hands-On Practice (20 minutes)
- Group Activity: Divide the participants into small groups (if applicable, based on session size). Each group will be given a different repair scenario or real-world case study.
- Objective: Each group will fill out a repair report based on their assigned scenario, following the steps they’ve learned in the workshop.
- Facilitator Role: Walk around and assist groups as needed, answering questions, clarifying points, and providing guidance where necessary.
Sample Scenarios for Breakout Groups:
- Generator failure due to low coolant levels.
- Generator not running due to fuel line blockage.
- Generator failing to start due to an electrical short.
After the activity, bring everyone back together to discuss their reports and share insights.
5. Q&A and Troubleshooting Tips (15 minutes)
- Open the floor for questions and discussions. Encourage participants to ask about specific challenges they face in the repair documentation process.
- Troubleshooting Tips: Share practical advice on how to approach common issues when documenting repairs:
- Dealing with incomplete information.
- How to handle multiple repairs in one report.
- Best practices for documenting electrical or mechanical repairs that are difficult to describe.
6. Conclusion & Wrap-Up (10 minutes)
- Summary: Briefly review the key takeaways from the session:
- Importance of accurate repair documentation.
- How to structure and document repairs step by step.
- Common challenges and best practices for troubleshooting.
- Closing Remarks: Thank everyone for participating. Provide any additional resources, such as repair documentation templates, troubleshooting guides, or relevant articles.
- Next Steps: Encourage participants to apply what they’ve learned in their daily work. Invite them to share feedback on the session through the post-training evaluation form.
Post-Workshop Actions
- Send out the post-training evaluation to collect participant feedback.
- Share the training materials (slides, templates, case studies) for future reference.
- Offer follow-up support via email or online forum for any questions or issues participants may face after applying the workshop’s content.
By following this structured approach, you will ensure that participants walk away with a clear understanding of how to document generator repairs accurately and effectively, equipping them with practical tools they can use in their daily work.
Leave a Reply