Your cart is currently empty!
Maintenance and Troubleshooting of Venue Machinery
SayPro is a Global Solutions Provider working with Individuals, Governments, Corporate Businesses, Municipalities, International Institutions. SayPro works across various Industries, Sectors providing wide range of solutions.
Email: info@saypro.online Call/WhatsApp: Use Chat Button 👇
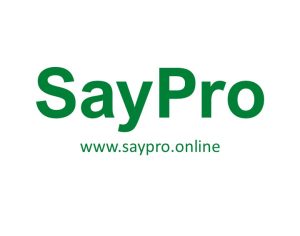
Maintenance and Troubleshooting of Venue Machinery
The proper maintenance and troubleshooting of venue machinery are critical for ensuring smooth operations, preventing unexpected breakdowns, and delivering high-quality service to guests. In the hospitality and event management industries, where downtime can result in significant operational disruptions, regular maintenance and proactive troubleshooting of machinery are essential to maintaining venue functionality and guest satisfaction. SayPro’s machinery solutions are designed to be robust, reliable, and easy to maintain, but even the most advanced systems require regular attention to stay in peak condition.
This detailed guide will explore the best practices for maintaining and troubleshooting venue machinery used in various aspects of event spaces, including audio-visual equipment, lighting, climate control systems, automated furniture and equipment movement systems, and more. By following these procedures, venues can ensure their machinery remains efficient, minimize the risk of failures, and extend the lifespan of their equipment.
1. Preventative Maintenance: Keeping Equipment in Top Condition
Preventative maintenance is a proactive approach to extending the lifespan of machinery, reducing the likelihood of breakdowns, and ensuring that the equipment is functioning optimally at all times. By scheduling regular inspections and maintenance tasks, venues can avoid costly repairs and disruptions to events. SayPro offers systems that help streamline preventative maintenance, ensuring nothing is overlooked.
Regular Inspections and System Checks
- Scheduled Inspections: SayPro’s integrated system allows venues to schedule regular maintenance for all machinery, whether it’s for the HVAC system, lighting equipment, or automated furniture transporters. A built-in calendar can alert staff to upcoming inspections based on usage frequency, manufacturer recommendations, or environmental factors (e.g., temperature or humidity).
- System Diagnostics: Modern venue machinery, including HVAC, AV, and lighting systems, often comes with built-in diagnostic tools that monitor performance. SayPro’s systems can perform automatic diagnostics to detect potential issues, such as abnormal temperature fluctuations, audio distortions, or failing lighting circuits. Diagnostics help pinpoint problems before they escalate into significant failures.
- Wear and Tear Checks: Equipment like automated trolleys, furniture handling systems, and conveyor belts undergo considerable wear during events. SayPro’s maintenance modules track usage data and notify venue management when specific components (such as wheels, motors, or hydraulic systems) require inspection or replacement due to wear and tear.
Cleaning and Calibration
- Routine Cleaning: Dust, debris, and general dirt can affect the performance of machinery, particularly in sensitive equipment like projectors, sound systems, and climate control units. Regular cleaning is essential to maintaining the efficiency of these systems. SayPro machinery offers self-cleaning functions for certain devices, such as air filters in HVAC systems, and guidelines for manual cleaning when necessary.
- Calibration: Some equipment, especially lighting and AV systems, may require periodic recalibration to ensure they provide the correct output. For example, lighting systems may need adjustments to ensure the right intensity and color temperature. SayPro’s automated calibration processes can help with these tasks, ensuring that all equipment operates according to the desired specifications.
Lubrication and Fluid Checks
- Mechanical Systems: Automated systems like chairs, tables, and other heavy equipment movers require lubrication to avoid friction and prevent wear. SayPro systems track the lubrication schedule, prompting maintenance staff to lubricate key components such as joints, motors, and wheels at regular intervals.
- Fluid and Pressure Monitoring: For hydraulic or pneumatic equipment, regular checks of fluid levels and pressure are essential. Low fluid levels or faulty pressure systems can cause malfunctions. SayPro can monitor fluid levels and pressure readings remotely, alerting staff when attention is required.
2. Troubleshooting Common Venue Machinery Issues
Even with preventative maintenance, machinery can encounter issues. Troubleshooting is essential for quickly identifying the root cause of a problem and minimizing any event disruptions. Below are common issues with venue machinery and how to troubleshoot them effectively.
Audio-Visual (AV) System Issues
- Problem: No Sound or Distorted Audio
- Cause: Loose cables, incorrect audio settings, or malfunctioning amplifiers.
- Solution: First, check all physical connections to ensure cables are securely plugged in. If the issue persists, use SayPro’s diagnostic tools to check for signal output. Adjust the audio settings through the central control system and check the audio levels. If the problem is related to equipment failure, replace the malfunctioning component.
- Problem: Poor Picture Quality on Projectors or Screens
- Cause: Dust on lenses, incorrect display settings, or malfunctioning projectors.
- Solution: Inspect the projector lens for dust or debris and clean it using the recommended method. Check the resolution settings and connection cables between the projector and the source device. Use SayPro’s diagnostic system to verify the projector’s internal status and replace any components that are showing signs of malfunction.
Lighting System Issues
- Problem: Flickering Lights
- Cause: Faulty bulbs, power supply fluctuations, or malfunctioning dimmer switches.
- Solution: Check the bulbs to ensure they are securely placed and properly installed. If flickering continues, use SayPro’s diagnostic system to check power supply levels and voltage consistency. If necessary, replace faulty dimmer switches or drivers.
- Problem: Lighting System Not Responding
- Cause: Control panel malfunction, faulty wiring, or software issues.
- Solution: Check the control panel or dimmer settings to ensure proper communication between the system and the lighting fixtures. Use SayPro’s software interface to reset the system and run a system diagnostic check. If software issues persist, consider updating or reinstalling the system firmware.
HVAC (Heating, Ventilation, and Air Conditioning) System Issues
- Problem: Uneven Temperature Distribution or Failure to Heat/Cool
- Cause: Blocked filters, faulty thermostats, or refrigerant leaks.
- Solution: Check HVAC filters for dust and debris and clean or replace them. Inspect thermostats to ensure they are functioning correctly, and calibrate if necessary. Use SayPro’s HVAC monitoring system to check refrigerant levels or any pressure anomalies. If leaks are detected, call a professional for repairs.
- Problem: Unpleasant Odors or Poor Air Quality
- Cause: Clogged ducts, outdated filters, or system malfunction.
- Solution: Check the air ducts for debris or blockages. Clean or replace filters as needed. Use SayPro’s air quality monitoring systems to assess CO2 levels or air composition. In extreme cases, professional cleaning may be required to remove buildup or mold within ducts.
Automated Furniture Movement Systems
- Problem: System Not Moving Equipment or Furniture
- Cause: Motor failure, sensor malfunction, or electrical issues.
- Solution: Inspect motors for overheating or damage. Check sensors and communication between the control system and the automated movement platform. If electrical issues are detected, test circuit connections and replace damaged wiring. Utilize SayPro’s diagnostics system to identify motor or actuator malfunctions.
- Problem: Equipment Moving Erratically or Slowing Down
- Cause: Friction due to lack of lubrication, misalignment, or low battery power.
- Solution: Check for any visible obstructions in the movement path and ensure proper alignment. Apply lubrication to moving parts. Test the battery levels if the system relies on battery power, and replace or recharge batteries as needed.
Event-Specific Equipment Issues (Catering, Audio, etc.)
- Problem: Catering Equipment Not Heating or Cooling
- Cause: Power supply issues, thermostat malfunctions, or system overloads.
- Solution: Check the power supply to the catering equipment to ensure proper voltage. Inspect thermostats for accuracy and recalibrate if necessary. If the issue persists, use SayPro’s diagnostic tools to check for internal faults or system overloads that may be preventing operation.
- Problem: Automated Registration or Ticketing Kiosks Not Functioning
- Cause: Software malfunction, connectivity issues, or hardware failure.
- Solution: Restart the kiosk system and ensure it is properly connected to the venue’s network. If the issue is software-related, update or reinstall the system’s firmware. For hardware issues, check the touchscreen, card readers, or printers for mechanical problems and replace faulty components.
3. Key Features of SayPro Machinery for Maintenance and Troubleshooting
SayPro machinery is equipped with a number of features designed to make maintenance and troubleshooting as easy as possible:
- Remote Diagnostics: SayPro offers remote monitoring and diagnostics for all connected machinery, allowing technicians to assess the health of systems from anywhere. This helps identify problems before they affect the event or guest experience.
- Automated Maintenance Scheduling: SayPro’s software allows for automated scheduling of maintenance tasks, including inspections, cleanings, and part replacements. This reduces the likelihood of missed maintenance and ensures that all systems are functioning optimally.
- Real-Time Alerts and Notifications: SayPro systems can send real-time alerts to maintenance teams whenever a problem is detected, allowing them to take immediate action. These alerts may include error codes, system failures, or performance abnormalities that need to be addressed quickly.
- User-Friendly Interfaces: SayPro’s machinery is designed with user-friendly interfaces, making it easy for non-technical staff to troubleshoot minor issues. Step-by-step troubleshooting guides and diagnostic reports are readily available within the system.
Conclusion
The maintenance and troubleshooting of venue machinery are essential for ensuring smooth operations and a high level of service quality. By following preventative maintenance schedules, conducting regular inspections, and utilizing SayPro’s diagnostic tools, venues can significantly reduce the risk of equipment failures and operational disruptions. Additionally, SayPro’s comprehensive troubleshooting features allow event managers and maintenance staff to quickly identify and resolve issues, ensuring that events run smoothly and guests have an exceptional experience. With the right maintenance strategy and troubleshooting techniques in place, SayPro machinery can provide reliable and efficient service for years to come.
Leave a Reply