Your cart is currently empty!
Author: Tumelo Seilaneng Mogorosi
SayPro is a Global Solutions Provider working with Individuals, Governments, Corporate Businesses, Municipalities, International Institutions. SayPro works across various Industries, Sectors providing wide range of solutions.
Email: info@saypro.online Call/WhatsApp: Use Chat Button ๐
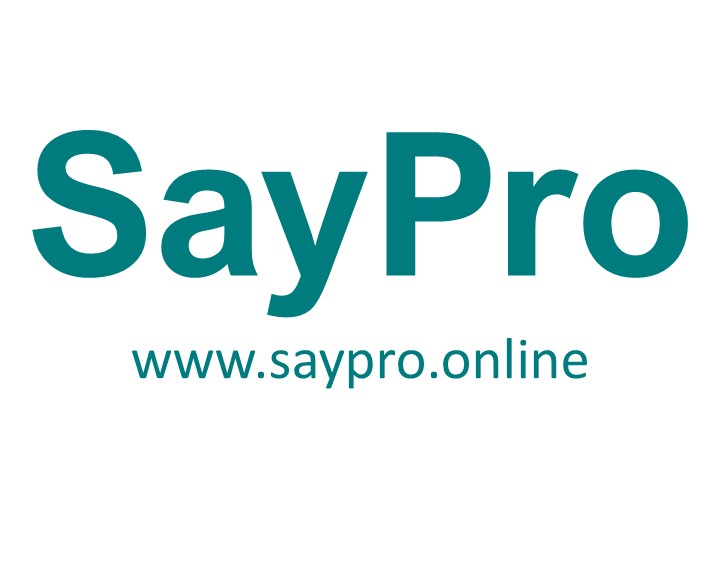
-
SayPro Supplemental learning materials
SayPro Monthly January SCSPR-98: Creating Supplemental Learning Materials and Quizzes
In the SayPro Monthly January SCSPR-98 role, creating supplemental learning materials and quizzes is essential for reinforcing the course content, enhancing participant understanding, and ensuring long-term retention of key concepts. These materials and assessments not only support the main course material but also encourage active engagement and provide a way to assess learners’ progress.
Below is a detailed outline of how to effectively create supplemental learning materials and quizzes to complement the Plastic Chairs Training Course.
1. Creating Supplemental Learning Materials
Supplemental learning materials go beyond the core course content and serve as additional resources to deepen participants’ knowledge, reinforce key points, and provide practical examples.
Key Responsibilities:
- Glossary of Key Terms:
Create a glossary that defines important terms used in plastic chair manufacturing, such as “injection molding,” “extrusion,” “blow molding,” “thermoplastics,” and “quality control.”- Example: A glossary entry for “Injection Molding” might explain the process of injecting molten plastic into a mold to form a chair component.
- Case Studies:
Develop real-world case studies that demonstrate how various manufacturing challenges were addressed, such as optimizing production lines or improving product durability.- Example: A case study might describe a company that successfully implemented an automated production system to reduce costs and increase throughput, including the lessons learned.
- Step-by-Step Guides:
Create detailed step-by-step guides that explain specific processes within plastic chair manufacturing. These can be useful for hands-on learning and reference material after the training.- Example: A step-by-step guide for setting up and operating an injection molding machine, including pre-production checks, loading material, and post-production cleaning.
- Infographics and Diagrams:
Design infographics and diagrams to visually explain complex processes. These can help learners better understand the flow of production and the relationship between different stages of manufacturing.- Example: An infographic of the plastic chair manufacturing process, from raw material selection to final assembly, showing key stages such as injection molding, cooling, and inspection.
- Instructional Videos:
Develop or curate short instructional videos that demonstrate the machinery and processes used in plastic chair manufacturing. These videos can show equipment in operation, explain troubleshooting steps, or illustrate safe machine handling techniques.- Example: A video showing the injection molding process, highlighting key points such as temperature control, mold setup, and material flow.
- Industry Articles and Research:
Share articles, research papers, or whitepapers related to the plastic chair manufacturing industry. These materials can provide insight into emerging technologies, market trends, or innovations in sustainability.- Example: A research article on the impact of biodegradable plastics in furniture manufacturing, discussing the challenges and opportunities they present.
- Practical Examples and Exercises:
Provide practical examples and exercises that encourage participants to apply what they have learned. These could include problem-solving scenarios, such as identifying the cause of production delays or improving a quality control system.- Example: A scenario-based exercise asking participants to assess the efficiency of a given plastic chair production line and suggest improvements.
2. Designing Quizzes to Reinforce Learning
Quizzes are an excellent way to assess knowledge retention and reinforce learning. They can be integrated into each section of the training or used as a final assessment.
Key Responsibilities:
- Types of Quizzes:
Design various types of quizzes to test different levels of knowledge:- Multiple-Choice Questions (MCQs): Great for testing factual knowledge and understanding of key concepts.
- True/False Questions: Useful for quick checks of fundamental principles.
- Fill-in-the-Blank Questions: Tests participantsโ ability to recall key terms and concepts.
- Matching Exercises: Useful for assessing knowledge of relationships between terms, processes, and components.
- Scenario-Based Questions: These assess the application of knowledge in real-world situations.
Example Questions:
- Multiple-Choice:
- Question: What is the primary advantage of injection molding in plastic chair manufacturing?
- A) Faster production time
- B) Lower material cost
- C) Ability to create complex shapes
- D) All of the above
- Answer: D) All of the above
- Question: What is the primary advantage of injection molding in plastic chair manufacturing?
- True/False:
- Question: Blow molding is commonly used for producing plastic chair frames.
- Answer: False (Injection molding is more commonly used for chair frames)
- Fill-in-the-Blank:
- Question: The process of shaping plastic using high-pressure air to form hollow objects is called __________.
- Answer: Blow molding
- Matching Exercise:
- Match the manufacturing process to its description:
- A) Injection Molding โ Produces solid, complex parts by injecting material into a mold.
- B) Extrusion โ Forms continuous shapes, like chair legs, by forcing plastic through a mold.
- C) Blow Molding โ Creates hollow objects by inflating softened plastic inside a mold.
- Answer:
- A) Injection Molding โ Produces solid, complex parts by injecting material into a mold.
- B) Extrusion โ Forms continuous shapes, like chair legs, by forcing plastic through a mold.
- C) Blow Molding โ Creates hollow objects by inflating softened plastic inside a mold.
- Match the manufacturing process to its description:
- Scenario-Based Question:
- Question: You notice that chairs produced on an injection molding machine are experiencing cracks in the seat. What would you do to troubleshoot this issue?
- A) Lower the molding temperature
- B) Check the mold design and material quality
- C) Increase the cooling time
- D) All of the above
- Answer: D) All of the above
- Question: You notice that chairs produced on an injection molding machine are experiencing cracks in the seat. What would you do to troubleshoot this issue?
3. Creating Assessments for Knowledge Retention
Assessments allow trainers to gauge whether the material has been effectively understood and retained by participants.
Key Responsibilities:
- Pre-Training Assessment:
Conduct a pre-training quiz to assess participants’ baseline knowledge of plastic chair manufacturing. This helps to tailor the training content to their needs and identify areas that may require more focus. - Mid-Course Quizzes:
Implement mid-course quizzes that break down the content into smaller segments. This helps reinforce key concepts and gauge whether the participants are grasping the material effectively. - Final Assessment:
Create a final exam that evaluates the participant’s overall understanding of the course material. The final assessment can include a mix of multiple-choice questions, scenario-based exercises, and practical applications.- Example: A comprehensive final exam covering everything from material selection and machine operation to quality control and troubleshooting.
4. Continuous Improvement and Updates
After each course or training session, evaluate the performance of participants through their quiz results, feedback, and overall learning outcomes. Use this data to:
- Refine Quizzes: Update quizzes to ensure they are aligned with the course material and participant learning needs.
- Incorporate Feedback: Use participant feedback to adjust the difficulty level, format, and content of future quizzes and supplemental materials.
- Adapt Content: If trends or gaps are identified in quiz results, update training materials to fill those gaps and enhance understanding.
Conclusion
Creating supplemental learning materials and quizzes as part of the SayPro Monthly January SCSPR-98 role ensures that participants are not only exposed to new information but also engage with the material in meaningful ways. These resources help reinforce the content, encourage active participation, and assess knowledge retention. By providing a variety of learning materialsโsuch as glossaries, case studies, videos, and quizzesโSayPro ensures a comprehensive, dynamic, and effective training program that caters to different learning styles and maximizes knowledge transfer.
- Glossary of Key Terms:
-
SayPro Course Content Creation
SayPro Monthly January SCSPR-98: Course Content Creation and Update
In the SayPro Monthly January SCSPR-98 role, Course Content Creation and Update is a vital responsibility that ensures the training program remains up-to-date, relevant, and aligned with the latest industry standards. The content needs to be dynamic, incorporating new advancements in technology, manufacturing techniques, and best practices to provide participants with a comprehensive and effective learning experience. Below is an outline of the key responsibilities and processes involved in creating and maintaining high-quality training materials for the Plastic Chairs Training Course.
1. Developing Training Materials
Key Responsibilities:
- Creating Presentations:
Develop well-structured, visually appealing, and informative PowerPoint slides or other presentation formats for use during both virtual and in-person sessions.- Content Structure: Ensure the presentations have a clear flow, starting with basic concepts and gradually progressing to more advanced topics like machinery, quality control, and troubleshooting.
- Engaging Visuals: Use diagrams, infographics, photos, and videos to illustrate key processes such as injection molding, extrusion, and blow molding.
- Real-World Examples: Incorporate industry-specific examples and case studies to demonstrate the practical application of training content in the manufacturing environment.
- Developing Video Content:
Create or curate short, instructional videos that cover critical aspects of the plastic chair manufacturing process.- Video Tutorials: Produce how-to videos for machine operation, troubleshooting, maintenance, and quality checks, ensuring the content is easy to follow and offers step-by-step guidance.
- Simulation Videos: Where possible, use simulated environments to demonstrate complex processes that are difficult to replicate in a live training environment.
- Writing Manuals and Guides:
Produce comprehensive manuals and training guides that can be distributed to participants before or after the training session.- Printed and Digital Versions: Create both printed and digital copies, ensuring that manuals are accessible for future reference and use in real-world applications.
- Clear and Concise Language: Write in simple, jargon-free language to ensure accessibility to participants of all experience levels, including those new to the manufacturing industry.
- Detailed Instructions: Include detailed instructions on using machinery, setting up production lines, quality control procedures, and troubleshooting common issues.
- Practical Examples:
Develop hands-on examples and activities that reinforce theoretical concepts and enhance the practical learning experience.- Hands-On Exercises: Include step-by-step instructions for participants to engage in machine operation, assembly processes, or testing of plastic chairs.
- Problem-Solving Activities: Create challenges and case studies where participants must use their knowledge to resolve real-world manufacturing issues, such as production delays or quality control failures.
2. Updating Existing Content
Key Responsibilities:
- Monitoring Industry Trends:
Regularly review the latest developments in the plastic chair manufacturing industry, including new machinery, materials, processes, and technologies.- Research: Stay up-to-date with advancements in molding techniques (e.g., 3D printing in plastic chair design), environmental concerns (e.g., biodegradable plastics), and sustainability practices.
- Technology Integration: Incorporate new technologies, such as automated systems and smart machinery, into the content, demonstrating their potential impact on production efficiency and quality.
- Reviewing and Revising Training Materials:
Periodically review and revise the training content to reflect any changes in industry practices, emerging technologies, and participant feedback.- Content Relevance: Ensure that all materials remain relevant by updating examples, statistics, and case studies to align with current industry standards.
- Incorporating Feedback: Take into account the feedback received from previous training sessions to identify areas for improvement or additional topics that need to be covered.
- Machine and Process Updates: When new machinery or updated manufacturing techniques are introduced in the industry, update the content to include these advancements, ensuring the training reflects the most current practices.
- Engagement with Experts:
Collaborate with industry experts, machine manufacturers, and technology providers to gain insights into the latest innovations and best practices in plastic chair manufacturing.- Expert Contributions: Invite guest experts to review and contribute to training content, ensuring it aligns with industry trends and provides authoritative insights.
3. Enhancing the Learning Experience
Key Responsibilities:
- Interactive Learning Tools:
Integrate interactive tools, such as quizzes, surveys, and simulations, into the training materials to help reinforce concepts and assess knowledge retention.- Quizzes and Tests: Develop short quizzes or assessments after each module to measure understanding and provide instant feedback.
- Simulation Software: Use virtual training simulators where participants can safely interact with digital models of manufacturing processes or machinery, gaining practical experience without the risk of equipment damage.
- Visual and Practical Content:
Ensure that all training materials, such as slides and videos, use high-quality visuals and demonstrate practical, real-world applications of the concepts.- Before and After Comparisons: Use visual comparisons to show the impact of different manufacturing techniques, such as how design changes influence chair stability or cost-efficiency.
- Step-by-Step Visuals: Create visual step-by-step breakdowns of complex processes like injection molding, including mold preparation, material injection, cooling, and final inspection.
4. Ensuring Content Accessibility
Key Responsibilities:
- Multilingual Support:
If applicable, develop training materials in multiple languages to support international participants, ensuring that all learners can engage with the content comfortably.- Translations: Work with professional translators to create versions of training manuals, videos, and presentations in other languages as needed.
- Online Accessibility:
Ensure that training materials are available on SayProโs online platform and are accessible across various devices (laptops, tablets, and smartphones).- Cloud Storage: Store and organize all training materials in an easy-to-access cloud-based system where participants can access content before, during, and after training sessions.
- Interactive Features: Ensure that online resources are interactive and easy to navigate, offering participants the ability to pause, rewind, or explore content at their own pace.
- Incorporating Feedback and Continuous Improvement:
- Surveys for Improvement: Collect feedback from participants after each training session to understand which aspects of the content worked well and which need improvement. This feedback loop helps refine training materials for future courses.
- Updating Content Based on Learner Needs: Continuously adapt the content to the evolving needs of the learners, particularly as manufacturing technologies change and new challenges emerge in the industry.
5. Integrating Sustainability and Innovation
Key Responsibilities:
- Sustainability Practices:
As sustainability becomes increasingly important in manufacturing, update the training materials to reflect eco-friendly practices in the plastic chair manufacturing process.- Material Sourcing: Include information about sourcing sustainable materials, such as recycled plastics, and the benefits of using them.
- Energy-Efficient Technologies: Highlight energy-efficient machines and processes that reduce carbon footprints and increase production efficiency.
- Emerging Technologies:
Integrate emerging technologies that could shape the future of plastic chair manufacturing, such as additive manufacturing (3D printing) or AI-driven production lines.- Innovation in Design and Production: Discuss how new innovations are revolutionizing the design, production, and cost-effectiveness of plastic chairs, ensuring participants are aware of the latest trends.
Conclusion
The SayPro Monthly January SCSPR-98 role requires a proactive and adaptive approach to Course Content Creation and Update. By regularly developing and refreshing training materials, such as presentations, videos, manuals, and practical exercises, the training program ensures that participants are equipped with the latest knowledge and skills relevant to the dynamic field of plastic chair manufacturing. This role plays a pivotal part in maintaining the trainingโs quality and relevance, contributing to the development of skilled professionals capable of implementing industry-leading manufacturing practices.
- Creating Presentations:
-
SayPro Online and In-person
SayPro Monthly January SCSPR-98: Hosting Webinars, Virtual Sessions, and In-Person Training
As part of the SayPro Monthly January SCSPR-98 role, hosting and facilitating both online and in-person training sessions is an essential responsibility. These training methods ensure that a wide audience can access the course material in a flexible manner, while also providing opportunities for hands-on experience and in-depth discussions when needed. Below are the key responsibilities and best practices for leveraging SayProโs online platform for webinars and virtual sessions, as well as facilitating in-person training at SayProโs headquarters or external locations.
1. Hosting Webinars and Virtual Training Sessions on SayProโs Online Platform
Key Responsibilities:
- Platform Setup and Configuration:
- Ensure the platform is ready: Before the session, verify that SayProโs online platform is set up correctly, including all necessary configurations for video, audio, and interactive tools (chat, polls, breakout rooms).
- Test Technology: Conduct a technology check to ensure that all tools, like screen sharing, virtual whiteboards, and multimedia features, are functioning properly.
- Scheduling and Invitations: Set up webinars or virtual sessions in advance, sending out invitations to the participants with detailed instructions for accessing the session, including links and login information.
- Course Delivery via Webinars:
- Engage Participants Virtually: During the session, use engaging content, such as slides, videos, and live demonstrations, to explain the plastic chair manufacturing process clearly and effectively.
- Interactive Features: Incorporate interactive elements like Q&A sessions, polls, and quizzes to keep the participants engaged and assess their understanding in real time.
- Breakout Sessions: Use breakout rooms for small group discussions or hands-on activities if applicable, allowing participants to collaborate, solve problems, or review key points together.
- Real-time Problem Solving: Be available for live Q&A sessions where participants can ask questions and seek clarification on any parts of the training.
- Technical Support:
- Troubleshooting Issues: Provide troubleshooting assistance during the webinar for participants who may experience technical difficulties with connectivity, audio, or video. Ensure that these issues are resolved quickly so the session can continue smoothly.
- Recording the Session: Record the webinar for future reference or for participants who were unable to attend the live session. This allows individuals to revisit the material at their own pace.
- Post-Webinar Follow-up:
- Provide Materials: After the session, share session recordings, presentations, supplementary resources, and any additional reading materials that might benefit the participants.
- Feedback Collection: Send a post-session survey to collect feedback on the webinar, helping improve future virtual training sessions.
- Answer Outstanding Questions: Follow up with answers to any questions that were not addressed during the webinar, ensuring participants receive complete responses to their inquiries.
2. Facilitating In-Person Training at SayProโs Headquarters or External Locations
Key Responsibilities:
- Coordination and Logistics:
- Venue Selection: If training is held at SayProโs headquarters, coordinate with the administrative team to secure an appropriate space that can accommodate all participants and is equipped with the necessary technology (projectors, screens, etc.).
- External Location Arrangements: If the training needs to be held at an external location, ensure all logistics are covered, including transportation, lodging (if necessary), and facility arrangements.
- Scheduling and Invitations: Send out detailed invitations with the training agenda, location information, and any preparatory instructions that participants need ahead of the in-person session.
- On-Site Setup:
- Training Equipment: Ensure all required training materials and equipment are prepared, such as printed manuals, machines for demonstrations, safety gear, and any props or tools needed for hands-on activities.
- Room Setup: Prepare the training room by arranging seating, ensuring a clear view of presentation materials, and setting up any necessary audiovisual tools (microphones, speakers, etc.).
- Participant Registration: Greet attendees, handle on-site registration, and provide materials like training handouts, name tags, and access to any online resources that will be used during the session.
- Delivering In-Person Training:
- Presentation: Deliver the training content in an engaging and interactive manner, using multimedia, live demonstrations, and practical activities to help participants understand the plastic chair manufacturing process.
- Group Interaction: Encourage questions, discussions, and collaboration among participants. Foster a learning environment where participants feel comfortable sharing insights and asking questions about real-world applications of the material.
- Hands-On Learning: Conduct practical, hands-on demonstrations where participants can engage with machinery or participate in mock exercises such as the molding process, quality control procedures, or machine maintenance.
- Participant Engagement:
- Interactive Learning: Use role-playing, group exercises, and collaborative problem-solving to deepen participants’ understanding and enhance their skills in a practical setting.
- Facilitate Discussions: Encourage small group discussions and brainstorming sessions to help participants engage with the content actively and learn from each otherโs experiences.
- Monitor Progress: Walk around the room to offer assistance to participants who may need additional guidance, making sure they are on track and grasping the key concepts.
- Safety and Compliance:
- Ensure Safety Protocols Are Followed: If the in-person training involves machinery or other potential hazards, ensure that all participants are wearing proper PPE (Personal Protective Equipment) and are following safety guidelines.
- Environmental Compliance: Ensure that the training environment adheres to all environmental and workplace regulations, maintaining a safe and compliant space for all activities.
- Post-Training Activities:
- Provide Follow-Up Resources: After the in-person training, distribute additional learning materials and resources, such as detailed guides or recorded demonstrations, to reinforce the training content.
- Feedback and Evaluation: Conduct an evaluation of the training session through feedback forms or surveys to assess participant satisfaction and identify areas for improvement in future in-person training events.
3. Hybrid Training Approach (Combining Virtual and In-Person)
For larger or more complex training programs, consider offering a hybrid training model, combining the benefits of both virtual and in-person formats.
Hybrid Model Benefits:
- Accessibility: This approach allows participants to access online content at their convenience and participate in live, interactive sessions in person if they are available or prefer hands-on learning.
- Flexibility: Hybrid training accommodates various learning styles and schedules, providing an opportunity for remote participants to join virtual sessions while still offering the deep engagement of in-person training.
- Continuous Engagement: Utilize online platforms for ongoing discussions, post-session forums, and group activities while maintaining the in-person experience for critical hands-on learning.
4. Continuous Improvement and Adaptation
Key Responsibilities:
- Evaluate Learning Outcomes: After both virtual and in-person sessions, assess the effectiveness of the training delivery through quizzes, assessments, or one-on-one discussions with participants.
- Adapt Based on Feedback: Use participant feedback and performance metrics to continually refine the training experience, adjusting the delivery methods, content, and technologies used for better engagement and understanding.
- Keep Up with Trends: Stay updated on new training technologies and methods that can enhance the online and in-person learning experience, integrating these innovations to keep the training program relevant and effective.
Conclusion
The SayPro Monthly January SCSPR-98 role encompasses a variety of responsibilities, from facilitating engaging and informative webinars and virtual training sessions on SayProโs online platform to organizing and delivering in-person training sessions at SayProโs headquarters or external venues. By effectively leveraging both online and in-person training options, this role ensures that participants gain comprehensive knowledge and practical skills in the plastic chair manufacturing process. The flexibility of hosting these sessions allows SayPro to reach a wide audience, ensuring that training is accessible, effective, and adaptable to diverse learning preferences.
- Platform Setup and Configuration:
-
SayPro Plastic Chairs Training Course
SayPro Monthly January SCSPR-98: Role and Key Responsibilities
The role associated with SayPro Monthly January SCSPR-98 involves the facilitation of a comprehensive Plastic Chairs Training Course. This responsibility is pivotal in ensuring participants gain an in-depth understanding of the plastic chair manufacturing process. The main focus of this role is course facilitation, ensuring that participants grasp key concepts, processes, and technical details effectively.
Below is a breakdown of the key responsibilities tied to this role:
1. Course Facilitation
Key Responsibilities:
- Delivering Training Content:
Present the training materials in a structured and engaging manner, ensuring the participants understand each step in the plastic chair manufacturing process. This includes everything from raw material selection to the final assembly of the chairs.- Presentation Style: Utilize various methods (lectures, demonstrations, and hands-on practice) to accommodate different learning styles and ensure active participation.
- Clarifying Concepts: Address any questions or concerns from the participants and explain complex processes clearly, ensuring everyone can follow along and comprehend the material.
- Promoting Engagement:
Encourage active participation by incorporating interactive elements into the training, such as quizzes, discussions, group activities, and case studies related to real-world plastic chair manufacturing challenges.- Workshops and Exercises: Organize practical sessions where trainees can observe or engage in hands-on tasks, like machine operation or troubleshooting, to reinforce theoretical concepts.
- Assessing Learning Progress:
Regularly assess participants’ understanding through quizzes, practical assessments, or group discussions. Provide constructive feedback on areas needing improvement and guide further study if necessary.- Monitoring Performance: Track the progress of each participant to identify those who may need additional help or clarification, offering support to ensure no one falls behind.
- Adjusting Content for Audience Needs:
Tailor the course content based on the skill levels and specific interests of the participants. For example, if the audience consists of beginners, provide foundational knowledge, while for more advanced learners, focus on specialized topics such as advanced machine maintenance or quality control techniques.
2. Ensuring Course Materials and Resources Are Well-Prepared
Key Responsibilities:
- Developing Course Materials:
Ensure that all training materials (slides, handouts, manuals, videos, and interactive exercises) are up to date, informative, and aligned with industry standards.- Content Accuracy: Regularly review and update the content to reflect the latest trends, technologies, and best practices in the plastic chair manufacturing industry.
- Visual Aids: Use visual aids like diagrams, flowcharts, and videos to enhance understanding of complex processes, especially when explaining technical concepts or machinery operations.
- Organizing Training Equipment:
Ensure that all necessary tools, machines, and equipment for practical demonstrations or exercises are available and in good working condition. This includes making sure that any plastic chair manufacturing machines used in training are operational and safe for use.- Hands-On Demonstrations: Coordinate practical demonstrations of machine operations, such as the injection molding process, extrusion, and quality control testing.
3. Providing Support and Guidance to Participants
Key Responsibilities:
- Individual Assistance:
Offer one-on-one support to participants who may need extra help in understanding specific aspects of the plastic chair manufacturing process. This could involve offering additional resources or providing practical examples to illustrate key concepts.- Troubleshooting Assistance: Be available to help participants troubleshoot issues that arise during hands-on exercises or machine operation sessions.
- Fostering Collaboration:
Encourage collaboration among participants by facilitating group discussions, problem-solving activities, or team-based exercises. This promotes peer learning and allows participants to share their insights and experiences.- Group Projects: Assign group tasks, such as developing a production plan or conducting a quality inspection, to allow participants to work together and apply what they’ve learned.
4. Evaluating the Effectiveness of the Training Program
Key Responsibilities:
- Feedback Collection:
After the training, collect feedback from participants to evaluate the effectiveness of the course. This feedback could include areas of improvement, suggestions for additional topics, or aspects that were particularly helpful.- Post-Training Survey: Administer a post-training survey or hold a debriefing session to understand the participants’ overall experience and assess whether the objectives of the course were met.
- Continuous Improvement:
Use participant feedback to make improvements to the course content and delivery methods. Identify areas where participants struggled and adjust future training programs accordingly to address any gaps in knowledge.- Reviewing Learning Outcomes: Assess whether participants have gained the necessary skills and knowledge to apply in a real-world setting, ensuring the training delivers tangible value.
5. Administrative Duties and Reporting
Key Responsibilities:
- Attendance and Record Keeping:
Maintain accurate records of attendance, participation, and performance throughout the training course. This information helps track each participant’s progress and attendance for certification purposes. - Reporting:
Prepare reports on the outcomes of the training sessions, including overall participation, feedback, and any recommendations for future training initiatives. These reports should highlight successes and areas for improvement.- Training Reports: Submit regular progress reports to the relevant stakeholders (such as the SayPro Bulk Manufacturing Machine Strategic Partnerships Office) about the course’s effectiveness and any issues encountered during the training.
6. Maintaining Knowledge and Staying Updated
Key Responsibilities:
- Continuous Learning:
Stay updated on the latest trends, technologies, and best practices in the plastic chair manufacturing industry to ensure the training material remains relevant and of high quality.- Attending Industry Events: Participate in industry workshops, webinars, and conferences to stay abreast of new developments in manufacturing processes and technology.
- Networking and Knowledge Sharing:
Collaborate with other industry experts or training professionals to exchange knowledge and learn about new training techniques or production processes that can enhance future training sessions.
Conclusion
The role associated with SayPro Monthly January SCSPR-98 requires a dynamic and hands-on approach to training. As the course facilitator, you will deliver valuable insights into the plastic chair manufacturing process, ensuring that all participants gain a deep understanding of essential concepts. By fostering a supportive, engaging learning environment, you help ensure the success of the training program and the continued growth of the manufacturing industry. Through regular assessments, practical demonstrations, and constant feedback loops, you play a crucial role in shaping the knowledge base of future plastic chair manufacturing professionals.
- Delivering Training Content:
-
SayPro Safety Protocols in Plastic Chair Manufacturing
SayPro: Safety Protocols in Plastic Chair Manufacturing
Ensuring a safe working environment and complying with environmental regulations is essential in any manufacturing facility, including plastic chair production. Adopting robust safety protocols helps protect workers, minimizes operational risks, and supports compliance with industry regulations. Below are comprehensive safety measures that should be implemented in a plastic chair manufacturing facility to ensure both worker safety and environmental sustainability.
1. Worker Safety Protocols
Overview:
Worker safety is paramount in the plastic chair manufacturing process, where employees are exposed to various hazards such as machinery, chemicals, heat, and heavy lifting. Establishing strict safety protocols minimizes the risk of accidents, injuries, and long-term health issues.Best Practices:
- Personal Protective Equipment (PPE):
Ensure that all workers wear the necessary PPE to protect themselves from workplace hazards. This includes:- Gloves: To protect hands from cuts, burns, and contact with hot surfaces or chemicals.
- Safety Glasses or Face Shields: To protect eyes from flying debris, chemicals, or molten plastic.
- Hearing Protection: For workers exposed to loud machinery, such as injection molding or blow molding machines.
- Safety Boots: To protect feet from heavy objects and prevent slips and falls.
- Respirators: In areas with high concentrations of dust or fumes, workers should use respirators to avoid inhaling harmful particles.
- Machine Safety:
- Safety Guards: Install protective guards on machines to prevent accidental contact with moving parts. This includes guards on injection molding machines, extrusion machines, and other high-risk equipment.
- Emergency Stop Buttons: Ensure that emergency stop buttons are easily accessible on all machinery. These should be clearly marked and maintained in a functional state.
- Lockout/Tagout (LOTO) Procedures: Implement strict lockout/tagout procedures when performing maintenance or repairs on machines. This ensures that machinery is properly de-energized to prevent accidental startups.
- Training and Awareness:
- Employee Training: All workers should receive comprehensive training on safety protocols, emergency procedures, and proper equipment usage. Training should be provided regularly to ensure workers are up-to-date on best safety practices.
- Safety Signage: Place clear and visible safety signs throughout the facility to remind workers of potential hazards, safety zones, and emergency exits.
- First Aid: Ensure that employees are trained in basic first aid and CPR. Additionally, the facility should be equipped with first-aid kits, and staff should know the location of medical supplies.
- Ergonomics and Manual Handling:
- Lifting Procedures: Train workers on proper lifting techniques to prevent strain injuries, particularly when handling heavy or bulky materials, like large molds or stacks of plastic chairs.
- Workstation Design: Ensure that workstations are ergonomically designed to reduce strain on workers. Adjustable tables, chairs, and equipment should be provided to accommodate various worker heights and preferences.
- Fire Safety:
- Fire Extinguishers and Sprinklers: Place fire extinguishers at strategic locations throughout the facility, especially near machines that may overheat or pose a fire risk. Ensure that sprinklers are installed and operational.
- Fire Safety Training: Conduct regular fire drills and provide fire safety training for all employees, focusing on safe evacuation procedures and the use of fire extinguishers.
2. Environmental Compliance Protocols
Overview:
Manufacturing facilities must comply with local, state, and federal environmental regulations to minimize their impact on the environment. This includes managing waste, controlling emissions, and ensuring proper disposal of hazardous materials.Best Practices:
- Waste Management:
- Plastic Waste Reduction: Implement processes to minimize waste during production. This includes optimizing material usage and reusing scrap plastic in the production of new parts or as recycled raw material.
- Recycling Program: Establish a comprehensive recycling program for plastic scraps, defective parts, and packaging materials. Partner with recycling companies to ensure that materials are properly processed and reused.
- Waste Segregation: Separate hazardous waste (such as solvents, chemicals, or contaminated materials) from non-hazardous waste to ensure safe disposal and compliance with regulations.
- Air Quality Control:
- Ventilation Systems: Install adequate ventilation systems to reduce the concentration of fumes, vapors, or dust generated during the production process, such as from the heating of plastics or chemical additives.
- Emission Control: Monitor and control emissions from equipment such as injection molding machines or extruders. Ensure that machines are properly maintained and comply with air quality regulations.
- Dust Management: Use dust collection systems to reduce the presence of fine plastic particles in the air, which can be harmful to workers’ respiratory health.
- Chemical Handling and Storage:
- Hazardous Material Handling: Properly label, store, and dispose of any chemicals used in the manufacturing process, including lubricants, solvents, or flame retardants. Follow Material Safety Data Sheet (MSDS) guidelines for each chemical.
- Chemical Spill Response: Implement protocols for quickly and safely dealing with chemical spills. This includes having spill kits readily available and training workers on how to use them.
- Proper Labeling and Storage: Store chemicals in designated, clearly marked areas that meet safety and environmental standards. Containers should be tightly sealed to prevent leaks or contamination.
- Energy Efficiency and Waste Reduction:
- Energy Consumption Monitoring: Monitor energy consumption across the facility and identify opportunities to reduce energy usage. Invest in energy-efficient machinery and lighting systems.
- Sustainable Materials: Whenever possible, choose environmentally friendly raw materials, such as recycled plastics or biodegradable alternatives. This helps reduce the environmental impact of manufacturing operations.
3. Emergency Protocols
Overview:
In addition to daily safety measures, it is crucial to have emergency protocols in place to address unexpected incidents, such as fires, chemical spills, or equipment failures. These protocols must be clearly communicated and rehearsed regularly.Best Practices:
- Emergency Response Team: Designate and train a team of employees to respond to emergencies. The team should be well-versed in first aid, fire response, spill containment, and evacuation procedures.
- Evacuation Plan: Develop and display a clear evacuation plan with designated exits and assembly points. Conduct regular evacuation drills to ensure that all employees know what to do in case of an emergency.
- Incident Reporting: Establish a system for reporting and documenting workplace accidents, near-misses, and environmental incidents. This helps identify hazards and implement corrective actions.
4. Regulatory Compliance and Audits
Overview:
To ensure compliance with environmental and safety regulations, regular audits and inspections are necessary. This includes both internal assessments and external inspections by regulatory bodies.Best Practices:
- Regular Safety Audits: Conduct periodic safety audits to assess adherence to safety protocols and identify any gaps in training or equipment maintenance.
- Environmental Audits: Perform environmental audits to verify compliance with waste management, emissions, and chemical handling regulations. This ensures that the facility is operating within the bounds of environmental laws.
- Third-Party Inspections: Engage with external safety and environmental consultants to review practices and recommend improvements. This provides an independent assessment of your facilityโs compliance.
Conclusion
Implementing comprehensive safety protocols and environmental compliance measures in a plastic chair manufacturing facility is essential for ensuring worker well-being and meeting regulatory standards. From worker protection through proper PPE, machine safety, and ergonomics, to environmental measures like waste management, energy efficiency, and air quality control, these protocols are vital for a safe and sustainable operation. Regular training, audits, and improvements will help maintain high safety standards while reducing environmental impact, ensuring that the manufacturing facility remains compliant and responsible.
- Personal Protective Equipment (PPE):
-
SayPro Machine Maintenance in Plastic Chair Manufacturing
SayPro: Machine Maintenance in Plastic Chair Manufacturing
Maintaining manufacturing machines is crucial for ensuring smooth production, minimizing downtime, and maximizing the efficiency and lifespan of the equipment. In plastic chair manufacturing, machines such as injection molding machines, blow molding machines, and extrusion machines play a pivotal role in creating high-quality products. Regular maintenance and troubleshooting practices help prevent breakdowns and extend the life of these machines. Below are some best practices for maintaining and troubleshooting plastic manufacturing machines.
1. Routine Preventive Maintenance
Overview:
Preventive maintenance involves regular, scheduled checks and servicing to ensure that equipment continues to operate efficiently and reduce the risk of unexpected failures. This proactive approach helps to identify and fix issues before they result in costly downtime.Best Practices:
- Scheduled Inspections: Set a maintenance schedule based on the manufacturerโs recommendations and production requirements. Machines should be inspected daily, weekly, or monthly depending on usage. Key components to check include:
- Hydraulic systems
- Cooling systems
- Drive motors
- Hopper and feed mechanisms
- Lubrication: Regularly lubricate moving parts such as screws, bearings, and gears to reduce friction and prevent premature wear. Proper lubrication also helps maintain smooth machine operation.
- Tip: Use the correct type and amount of lubricant specified in the machineโs manual to avoid overuse or contamination.
- Cleaning: Keeping machines clean is essential for preventing dust, debris, and plastic residue from affecting performance. Cleaning should be done regularly to remove material build-up from the molding or extrusion processes, which can cause clogs, inconsistencies, and damage to the machine.
- Tip: Clean all vents, molds, and cooling systems after every production run.
- Filter Replacement: Regularly replace filters in hydraulic, cooling, and air systems to ensure efficient operation. Clogged filters can reduce performance and lead to overheating.
2. Calibration and Alignment
Overview:
Proper calibration and alignment of the machine ensure that the molds, heating elements, and other components are functioning at optimal performance, which is critical for producing high-quality plastic chair parts.Best Practices:
- Mold Alignment: Check the alignment of molds to ensure even pressure distribution during molding. Misalignment can lead to defects such as uneven parts or flash (excess plastic).
- Tip: Use a dial indicator or laser alignment tool to check mold alignment and adjust accordingly.
- Temperature Calibration: Ensure that the temperature controllers are calibrated and maintain the correct temperature settings for the material being used (e.g., for injection molding, blow molding, and extrusion).
- Tip: Regularly verify the accuracy of temperature gauges to prevent overheating or underheating, which can affect product quality.
- Pressure and Speed Settings: Review the pressure and speed settings for molding and extrusion processes to maintain consistency in material flow and part production. Misconfigured settings can cause defects in the final product or machine malfunctions.
- Tip: Regularly check the machineโs pressure gauges and adjust to maintain optimal performance.
3. Wear and Tear Management
Overview:
All manufacturing machines experience wear and tear over time, especially with components such as screws, nozzles, molds, and seals. Timely replacement of worn-out parts is critical for preventing costly repairs and maintaining consistent production quality.Best Practices:
- Monitor High-Wear Components: Components like injection molding screws, mold cavities, and nozzle tips are prone to wear. Regularly inspect these parts for signs of damage such as cracks, wear marks, or material erosion.
- Tip: Keep an inventory of critical spare parts for quick replacement to minimize downtime.
- Replace Worn Seals: Seals and gaskets in machines can wear out over time, leading to air or fluid leaks. Replace seals as part of routine maintenance to maintain proper pressure and prevent material contamination.
- Tip: Use high-quality seals to reduce the frequency of replacements.
- Check and Replace Filters and O-Rings: Filters and O-rings should be checked regularly for damage and replaced as needed to ensure a clean, smooth operation. Damaged seals can lead to contamination of materials or hydraulic fluid, affecting product quality and machine efficiency.
4. Troubleshooting Common Issues
Overview:
Even with regular maintenance, issues can still arise with manufacturing machines. Knowing how to troubleshoot common problems quickly can prevent prolonged downtime and reduce repair costs. Below are some common issues that may arise and how to address them.Common Issues and Solutions:
- Machine Not Starting:
- Possible Causes: Electrical issues, tripped circuit breaker, or malfunctioning power supply.
- Solutions:
- Check the electrical connections and ensure the circuit breaker is not tripped.
- Inspect the power supply and control panel for signs of damage or malfunction.
- Inconsistent Injection Pressure (for Injection Molding Machines):
- Possible Causes: Blocked or worn-out nozzles, clogged heating elements, or incorrect machine settings.
- Solutions:
- Clean and inspect the nozzle and heating elements for blockages.
- Verify that pressure settings are calibrated correctly.
- Check for worn-out seals or damaged valves in the injection system.
- Plastic Overflow or Flashing:
- Possible Causes: Excessive pressure, improper mold alignment, or damaged mold components.
- Solutions:
- Check mold alignment and adjust to ensure even pressure distribution.
- Ensure the machine is not over-pressurizing, and adjust the pressure settings if needed.
- Inspect the mold for wear and tear, and replace worn components.
- Uneven Cooling (for Blow Molding):
- Possible Causes: Clogged cooling channels, incorrect cooling temperature settings, or uneven mold temperature.
- Solutions:
- Inspect and clean cooling channels to ensure there is no blockage.
- Adjust cooling settings to ensure uniform temperature distribution across the mold.
- Check that the mold is evenly heated and cooled to prevent warping.
- Extrusion Problems (for Extrusion Machines):
- Possible Causes: Material inconsistency, blocked die, or damaged drive motors.
- Solutions:
- Ensure that the raw material is free of contaminants and has the correct composition.
- Clean the extrusion die to remove any blockages or build-up.
- Inspect drive motors for proper operation, and replace any faulty parts.
5. Record Keeping and Data Analysis
Overview:
Accurate record-keeping of maintenance activities, machine performance, and any troubleshooting interventions is essential for tracking machine health and improving efficiency over time.Best Practices:
- Maintenance Logs: Keep detailed logs of all preventive maintenance tasks performed, including inspections, lubrication, parts replacements, and calibrations. This ensures consistency and helps identify patterns of wear or recurring issues.
- Tip: Use digital platforms or software to track maintenance schedules and machine performance.
- Performance Data Analysis: Collect data on machine performance, such as production rates, downtime, and defect rates. Analyzing this data can identify recurring problems or areas where maintenance needs to be improved.
- Tip: Use predictive maintenance software that can monitor machine conditions in real-time and provide alerts for potential issues before they occur.
Conclusion
Effective machine maintenance is critical to ensuring long-term efficiency and minimizing downtime in plastic chair manufacturing. By implementing best practices such as regular preventive maintenance, calibration, monitoring wear and tear, troubleshooting common issues, and keeping detailed records, manufacturers can keep their equipment running smoothly. With these practices, they can maximize machine lifespan, improve production efficiency, and consistently produce high-quality plastic chairs.
- Scheduled Inspections: Set a maintenance schedule based on the manufacturerโs recommendations and production requirements. Machines should be inspected daily, weekly, or monthly depending on usage. Key components to check include:
-
SayPro Quality Control in Plastic Chair Manufacturing
SayPro: Quality Control in Plastic Chair Manufacturing
Ensuring product quality is critical in plastic chair manufacturing. High-quality plastic chairs must meet specific standards for durability, safety, comfort, and appearance. Quality control (QC) techniques throughout the production process help identify potential defects and prevent subpar products from reaching the market. This involves rigorous control of factors such as mold design, material selection, and inspections at various stages of production.
1. Mold Design
Overview: The design of the mold is a critical factor in ensuring that the plastic chair components have precise dimensions and surface finishes. Poor mold design can lead to defects such as warping, dimensional inconsistencies, or weak points in the product.
Techniques:
- Precision in Mold Design: A high-quality mold should be designed to ensure uniform material distribution, minimize stress on the plastic, and accommodate any necessary cooling channels for consistent solidification. This minimizes the risk of warping or other defects.
- Material Flow Simulation: Before manufacturing the mold, computer-aided design (CAD) software and mold flow simulation tools are used to predict how the molten plastic will flow into the mold, allowing manufacturers to optimize the design for efficiency and quality.
- Mold Maintenance: Regular maintenance of molds, including cleaning, sharpening, and recalibration, ensures that they continue to produce parts with consistent quality.
Benefits:
- Reduces defects such as sink marks, flashing, or air pockets.
- Ensures accurate dimensions and smooth surface finishes.
- Increases the mold’s lifespan and maintains production efficiency.
2. Material Selection
Overview: The quality of the material used in plastic chair manufacturing directly affects the productโs strength, durability, flexibility, and overall performance. High-quality raw materials will result in products that meet the required standards and exceed customer expectations.
Techniques:
- Material Grade Selection: Choosing the correct grade of plastic is vital. Common materials for plastic chairs include polypropylene (PP), polyethylene (PE), and ABS. The material should be selected based on the required characteristics, such as:
- Strength: To ensure the chair can support weight without breaking.
- UV Resistance: To prevent degradation from prolonged exposure to sunlight.
- Impact Resistance: To prevent cracking from bumps or falls.
- Aesthetic Qualities: The material should be easy to color, texture, and finish for appealing designs.
- Material Testing: Before full-scale production, raw materials undergo rigorous testing to ensure they meet quality standards. This can include:
- Tensile Testing: To determine the strength and elasticity of the material.
- Impact Testing: To assess how the material reacts to sudden force or stress.
- UV Stability Testing: To ensure the material will not degrade or lose color over time when exposed to sunlight.
- Additives and Recycled Materials: Sometimes, manufacturers use additives to improve performance, such as flame retardants, stabilizers, or anti-scratch agents. When using recycled plastic, it is essential to ensure it meets quality standards through proper sorting and testing.
Benefits:
- Ensures product durability and longevity.
- Reduces risk of failure due to material weaknesses.
- Promotes sustainability by selecting eco-friendly or recyclable materials.
3. Process Control and Inspections
Overview: Process control ensures that every step in the manufacturing process is performed consistently and to the highest standard. Continuous inspection at each stage helps identify defects early and reduces waste.
Techniques:
- In-Process Inspections:
- Visual Inspection: Workers inspect molded parts for visible defects such as cracks, discolorations, or surface imperfections during and after production.
- Dimensional Inspection: Using precision tools such as calipers, micrometers, and laser measurement systems, the dimensions of the molded parts are checked to ensure they meet the exact specifications.
- Weight Checks: Checking the weight of the molded parts helps ensure that the correct amount of material is used and that no over- or under-molding occurs, which can lead to defects or weak areas in the chair.
- Post-Molding Testing:
- Strength and Durability Testing: Plastic chairs undergo strength tests to simulate real-life use. These tests include load-bearing tests to verify the chairโs capacity to withstand pressure or weight.
- Stability Testing: Chairs are tested for stability to ensure they do not tip over easily. This includes checking the alignment of the legs and structure.
- Ergonomics Testing: Ergonomics is a key factor in the quality of a chair. During testing, manufacturers check if the seat and backrest provide proper comfort and support for users, ensuring user satisfaction and minimizing the risk of discomfort or injury.
- End-of-Line Quality Control:
- Final Assembly Checks: When the chair is fully assembled, final inspections ensure that all parts fit together properly, and the chair operates smoothly. Any loose screws or unaligned parts can be rectified.
- Functional Testing: A sample of chairs may undergo functional tests such as stacking, sitting, and maneuvering to ensure the final product meets performance expectations.
- Safety Inspections: Compliance with safety standards is verified, including ensuring the chair does not have sharp edges, defects that could cause injury, or instability.
Benefits:
- Helps detect defects early in the process, reducing scrap and rework.
- Ensures that each chair meets strict quality standards.
- Improves customer satisfaction by guaranteeing a product that is safe, durable, and functional.
4. Post-Production and Packaging Inspections
Overview: After manufacturing is completed, additional inspections ensure that the final product is fully functional and free of defects before it reaches the consumer.
Techniques:
- Final Product Inspection: Each chair is inspected for minor cosmetic defects and functional issues. This includes checks for smoothness of finishes, color consistency, and overall appearance.
- Packaging Inspections: To avoid damage during shipping, packaging is tested for strength and durability. Chairs are checked to ensure they are correctly packed with sufficient padding, and the packaging is properly labeled with product details.
Benefits:
- Prevents shipping damaged goods.
- Ensures the product reaches the customer in perfect condition.
- Confirms compliance with packaging and labeling requirements.
5. Continuous Improvement and Feedback
Overview: Quality control doesnโt stop once the product is manufactured. Continuous improvement efforts are essential to maintaining high standards and adapting to changes in customer preferences or technological advancements.
Techniques:
- Customer Feedback: Collecting and analyzing customer feedback helps identify any recurring product issues or areas for improvement. Manufacturers can use this data to make design or material adjustments.
- Lean Manufacturing and Six Sigma: These methodologies help optimize the manufacturing process by identifying inefficiencies, reducing waste, and improving overall product quality through data-driven decision-making.
- Employee Training: Continuous training for employees in quality control techniques ensures that the entire workforce is engaged in maintaining product quality at every stage.
Benefits:
- Promotes ongoing product refinement.
- Enhances customer satisfaction through continuous improvements.
- Increases manufacturing efficiency and reduces waste.
Conclusion
Quality control in plastic chair manufacturing is a multi-faceted approach that involves careful mold design, meticulous material selection, and thorough inspections at every stage of production. By employing these techniques, manufacturers can ensure that each plastic chair produced is of the highest quality, durable, and safe for consumers. From the initial design phase to final packaging, a commitment to quality control is essential for maintaining a strong brand reputation and meeting customer expectations.
-
SayPro Plastic Chair Manufacturing Process
SayPro: Plastic Chair Manufacturing Process
The plastic chair manufacturing process involves several steps, each designed to ensure the production of durable, high-quality chairs. From selecting the raw materials to final assembly, each stage plays a crucial role in the creation of a functional and aesthetically pleasing product. Below is a detailed, step-by-step breakdown of the typical plastic chair manufacturing process.
1. Raw Material Selection and Processing
Overview: The first step in the production of plastic chairs is selecting the appropriate raw materials. The most commonly used plastics in chair manufacturing are polypropylene (PP), polyethylene (PE), and acrylonitrile butadiene styrene (ABS). These materials are known for their strength, durability, and versatility, making them ideal for chair manufacturing.
Steps:
- Material Selection: Manufacturers select high-quality plastic pellets or granules, which are available in various grades, depending on the desired characteristics (e.g., strength, flexibility, UV resistance).
- Additives: Depending on the requirements, additives such as stabilizers, UV inhibitors, colorants, or flame retardants may be mixed with the plastic to enhance performance.
- Drying: The raw plastic material is often dried to remove any moisture, as moisture can cause defects in the finished product during the molding process.
2. Material Heating and Melting
Overview: The selected plastic material is then heated to its melting point, so it can be easily molded into the desired shape. This is typically done using an extruder (for extrusion molding) or an injection molding machine (for injection molding processes).
Steps:
- Melting: Plastic pellets are fed into an extruder or injection molding machine where they are subjected to controlled heating. The material is heated until it reaches a molten state (typically 180โ250ยฐC depending on the plastic).
- Mixing: In some cases, the molten plastic is mixed with other materials, such as reinforcements or colorants, to ensure uniformity in the composition.
3. Molding Process (Injection Molding, Blow Molding, or Extrusion)
The molding process is where the plastic is shaped into the specific parts of the chair, like the seat, backrest, and legs. Different machines are used for different molding techniques.
Injection Molding (for complex parts like armrests, backrests, etc.)
- Process:
- The molten plastic is injected into a mold cavity under high pressure.
- The mold is typically made from metal and has a cavity shaped like the desired chair part.
- Once the mold is filled, the plastic is allowed to cool and solidify.
- The mold is then opened, and the molded part is ejected.
- Products: This process is used for detailed and intricate parts of the chair, such as armrests, backrests, and decorative accents.
Blow Molding (for hollow parts like the seat and backrest)
- Process:
- A hollow tube (called a parison) is extruded and placed into a mold.
- The parison is inflated using air pressure, forcing it to take the shape of the mold cavity.
- After cooling, the mold opens, and the hollow chair part is removed.
- Products: This process is ideal for producing lightweight, hollow parts like the seat or backrest of a chair.
Extrusion Molding (for frames and legs)
- Process:
- The plastic material is continuously fed through an extruder, where it is heated and forced through a die.
- The die shapes the molten plastic into a continuous profile (e.g., legs or frames).
- The extruded shape is cooled and cut into the required lengths.
- Products: This process is used to create long, continuous parts, such as legs, frames, or other structural components of the chair.
4. Cooling and Solidification
Overview: After the plastic is molded into its shape, it must be cooled to solidify and retain its form. Cooling is an essential part of the process, as it ensures that the plastic maintains its shape and dimensional accuracy.
Steps:
- Cooling Time: The time required for cooling depends on the size and thickness of the part being molded. Smaller parts cool quickly, while larger parts take longer.
- Cooling Method: Parts may be cooled using air or water, depending on the type of plastic and the molding method. In injection molding, cooling is often facilitated by water channels inside the mold.
5. Trimming and Finishing
Overview: Once the molded parts have cooled and solidified, they often require additional processing to remove excess material and ensure a clean, finished product.
Steps:
- Trimming: Flash (excess material) left from the molding process is trimmed off. This could include trimming excess plastic from the edges or parts of the mold.
- Deburring: In some cases, the molded parts may have rough edges that need to be smoothed out.
- Polishing/Surface Treatment: If necessary, parts may undergo additional surface treatments such as polishing, sanding, or painting to improve the final appearance.
6. Assembly
Overview: After all the individual parts have been molded and finished, they are ready for assembly. This is the stage where the plastic chair is put together, often using screws, clips, or snaps to attach the various parts.
Steps:
- Part Inspection: Each part is inspected for defects and quality before assembly.
- Assembly: Components such as the seat, backrest, legs, and armrests are carefully assembled into a final chair. This can be done manually or with the help of automated systems, depending on the production scale.
- Attachment: Depending on the design, different joining methods may be used, such as bolting, snapping, or welding plastic parts together.
7. Quality Control and Testing
Overview: Quality control is crucial to ensuring that each plastic chair meets industry standards for durability, comfort, and safety. This process involves various tests and inspections to identify defects before the chairs are shipped to customers.
Steps:
- Visual Inspection: Inspect for any visible defects such as cracks, discoloration, or uneven surfaces.
- Dimensional Testing: Verify that the chair parts meet the required dimensions and tolerances.
- Strength Testing: Perform tests to ensure the chair can withstand weight and pressure, ensuring that itโs safe for use.
- Compliance Testing: Ensure the chair meets safety standards and regulatory requirements (e.g., ISO, ASTM).
8. Packaging and Shipping
Overview: Once the chairs have passed quality control, they are ready for packaging and distribution.
Steps:
- Packaging: Chairs are carefully packaged, often in flat-pack form, to reduce shipping costs. Protective materials such as foam, plastic wrapping, or cardboard are used to prevent damage during transportation.
- Labeling: Each package is labeled with the necessary information, including product details, manufacturer information, and shipping instructions.
- Shipping: The packaged chairs are then shipped to retailers, distributors, or directly to customers.
Conclusion
The plastic chair manufacturing process involves a series of intricate steps to transform raw materials into durable and functional seating products. From material selection and heating to molding, cooling, and final assembly, each stage ensures that the end product meets the highest standards of quality, comfort, and safety. By optimizing these processes and employing advanced manufacturing technologies, manufacturers can produce high-quality plastic chairs efficiently and cost-effectively, catering to a wide range of customer needs.
-
SayPro Understanding Plastic Manufacturing Machines
SayPro: Understanding Plastic Manufacturing Machines
Plastic chair manufacturing involves several specialized machines that are key to producing high-quality, durable products efficiently. These machines utilize various molding and shaping techniques to transform raw materials into finished plastic chairs. In this section, we will provide an in-depth explanation of the three main machines used in plastic chair manufacturing: injection molding machines, blow molding machines, and extrusion machines.
Each of these machines serves a specific function and has its own advantages and applications in the manufacturing process of plastic chairs.
1. Injection Molding Machines
Overview: Injection molding is one of the most common and versatile methods for producing plastic components, including plastic chairs. In this process, plastic pellets or granules are heated and then injected into a mold under high pressure to form the desired shape.
Key Components:
- Hopper: A container where plastic granules are stored before being fed into the machine.
- Barrel and Screw: The screw inside the barrel melts and pushes the plastic material through the nozzle into the mold.
- Mold: A metal cavity where the melted plastic is injected and cooled to form the shape of the chair part (e.g., backrest, seat).
- Clamping Unit: Holds the mold in place during the injection process.
How It Works:
- Plastic pellets are loaded into the hopper, where they are heated by the barrel to become molten.
- The molten plastic is then injected into a precisely designed mold under high pressure.
- The mold cools and solidifies the plastic into the shape of the chair part.
- The mold is then opened, and the finished part is ejected.
Applications in Chair Manufacturing:
- Injection molding machines are widely used for producing intricate chair parts, such as armrests, backrests, and legs.
- The method allows for high precision and consistency, producing parts with excellent dimensional accuracy and surface finishes.
- It’s also ideal for manufacturing large quantities of identical parts efficiently.
Advantages:
- High precision and repeatability.
- Complex shapes can be achieved, including hollow designs and intricate details.
- Fast production speeds, especially for large volumes.
2. Blow Molding Machines
Overview: Blow molding is another widely used manufacturing process for creating plastic chair components, particularly for parts that need to be hollow, such as the seat of a plastic chair. This method is ideal for producing lightweight, durable, and ergonomic plastic seating solutions.
Key Components:
- Extruder: Used to heat and shape the plastic into a tube, known as the parison.
- Mold: A cavity in which the parison is inflated to take its final shape.
- Blow Pin: The tool used to inflate the parison by blowing air into it to mold the plastic into the shape of the chair.
How It Works:
- Plastic is fed into the extruder, where it is heated and formed into a hollow tube (the parison).
- The parison is then clamped into a mold that matches the shape of the chair seat (or other parts).
- Air is blown into the parison, inflating it and forcing it to conform to the moldโs shape.
- The plastic is cooled and solidified, and the mold is opened to release the finished component.
Applications in Chair Manufacturing:
- Blow molding is used primarily for creating hollow chair parts such as the seat, backrest, or bases.
- The process is ideal for lightweight designs while maintaining the strength and durability of the chair.
- It can be used to create ergonomic designs with a smooth, seamless finish.
Advantages:
- Efficient for producing hollow and large parts with a uniform wall thickness.
- Suitable for lightweight designs.
- High production speed with low material waste.
3. Extrusion Machines
Overview: Extrusion is a continuous manufacturing process used to shape plastic materials into long profiles, which can then be cut to specific lengths or used in further assembly. In the context of plastic chair manufacturing, extrusion is often used to create plastic parts like chair legs, supports, or frames.
Key Components:
- Extruder: A machine that melts the plastic and forces it through a die to create a continuous profile.
- Die: A mold that determines the shape of the extruded plastic profile (e.g., round, square, or custom shapes).
- Cooling System: The extruded material is cooled and hardened as it exits the die.
- Cutter: The extruded material is cut into specific lengths or shapes as needed for assembly.
How It Works:
- Plastic pellets or granules are loaded into the extruder and heated until they become a molten state.
- The molten plastic is forced through a die that shapes it into the desired profile.
- The extruded plastic is cooled, either by air or water, to solidify the shape.
- The cooled extrusions are then cut to the required lengths or processed further.
Applications in Chair Manufacturing:
- Extrusion is commonly used to produce long chair components, such as the frames, legs, or crossbars that provide structural support for the chair.
- The process is ideal for creating uniform, straight profiles that can be used in various chair designs.
Advantages:
- Ideal for continuous production of long, straight components.
- Cost-effective for large-scale production runs.
- Allows for flexibility in designing profiles for chair frames and supports.
Conclusion: The Role of Machines in Plastic Chair Manufacturing
Each of the machines mentioned above plays a critical role in the overall manufacturing process of plastic chairs. While injection molding machines are essential for producing intricate, detailed parts with high precision, blow molding machines are optimal for creating lightweight, hollow parts like seats and backrests. Meanwhile, extrusion machines provide the necessary means for producing continuous profiles, such as the structural components of a chair.
Understanding the functions, benefits, and applications of these machines is crucial for manufacturers to optimize production processes, reduce costs, and maintain high-quality standards in the plastic chair industry. By utilizing these machines effectively, manufacturers can create functional, durable, and ergonomic plastic chairs to meet the demands of a wide variety of customers.
-
SayPro Monthly Plastic Chairs Training Course
SayPro Monthly January SCSPR-98: SayPro Monthly Plastic Chairs Training Course
Course Overview: The SayPro Monthly Plastic Chairs Training Course is a comprehensive educational program designed to provide in-depth knowledge and practical insights into the plastic chair manufacturing process. This course is hosted by the SayPro Bulk Manufacturing Machine Strategic Partnerships Office under the SayPro Strategic Partnerships Royalty Program. As part of this initiative, attendees will gain expertise on a wide range of key topics necessary for success in the plastic chair production sector.
The course will be divided into several modules that delve into the intricacies of the plastic chair industry, its manufacturing techniques, and the critical role of strategic partnerships. By the end of the course, participants will have a solid understanding of both the operational and business aspects of plastic chair manufacturing.
Course Topics:
1. Introduction to Plastic Chair Manufacturing:
- Overview of the Plastic Chair Industry: Gain a comprehensive understanding of the plastic chair industry, including its historical development, current position, and future prospects. This module will introduce the primary sectors involved in the plastic chair production, such as design, manufacturing, and distribution.
- Production Trends: Learn about current trends in the plastic chair manufacturing process. This includes technological innovations, sustainable practices, and evolving consumer preferences. The module will cover how automation, material improvements, and eco-friendly designs are reshaping the industry.
- Market Demands: Understand the changing consumer demands for plastic chairs in various markets, such as residential, commercial, and institutional sectors. This module will also explore how companies can adapt to meet the growing need for lightweight, durable, and aesthetically pleasing plastic seating solutions.
2. Manufacturing Process and Technology:
- Materials Selection: Dive into the types of plastics commonly used in chair manufacturing, such as polypropylene, polyethylene, and ABS, as well as the properties of these materials that make them suitable for seating solutions.
- Production Techniques: Explore the different manufacturing techniques used in the production of plastic chairs, including injection molding, blow molding, and rotational molding. Learn how each technique influences the quality, durability, and cost-effectiveness of the final product.
- Automation and Efficiency: Understand the role of automated systems in plastic chair manufacturing. Participants will gain insight into how bulk manufacturing machines are integrated into the production line to streamline processes, increase productivity, and reduce human error.
3. Design and Ergonomics:
- Chair Design Principles: Learn the essential principles of designing plastic chairs that are both functional and aesthetically pleasing. This includes considerations such as style, comfort, and usability.
- Ergonomic Considerations: Focus on designing chairs that promote good posture, comfort, and support for users. This module will highlight the importance of ergonomics in the plastic chair industry and its impact on customer satisfaction and product performance.
4. Quality Control and Safety Standards:
- Ensuring Product Quality: Learn the methods and standards for ensuring that plastic chairs meet the highest quality requirements. This includes both aesthetic quality and durability, such as resistance to wear, UV light exposure, and weather conditions.
- Compliance with Safety Standards: Understand the international and local safety standards that apply to plastic chairs. The course will provide insights into regulations and certifications, such as ISO standards, ensuring that manufacturers comply with safety requirements to avoid liability and maintain consumer trust.
5. Market Strategies and Strategic Partnerships:
- Developing Market Strategies: Explore strategies to successfully market plastic chairs, including product differentiation, branding, and targeting specific demographics. Learn how manufacturers can position themselves effectively in the competitive market.
- Building Strategic Partnerships: Discover how to build strategic partnerships with suppliers, distributors, and retailers to enhance the business’s reach and profitability. This section will cover the key factors to consider when establishing long-term partnerships within the plastic chair manufacturing ecosystem.
6. Sustainability and Environmental Impact:
- Sustainable Manufacturing Practices: Learn about the importance of sustainability in plastic chair production. This includes exploring eco-friendly materials, recycling programs, and energy-efficient production methods that reduce the environmental impact of manufacturing.
- Circular Economy in Plastic Manufacturing: Understand the concept of a circular economy in the plastic industry, including how companies can contribute to reducing plastic waste by designing for recyclability and implementing take-back schemes.
7. The Future of Plastic Chair Manufacturing:
- Innovative Trends and Technologies: Get a glimpse of the future of plastic chair manufacturing, including upcoming technologies such as 3D printing, smart materials, and robotic manufacturing. Learn how the industry is evolving to meet the needs of an ever-changing market.
- Global Market Outlook: Explore the global trends and expansion opportunities in emerging markets. This module will help manufacturers understand the global demand and opportunities for plastic chairs in different regions.
Conclusion: By participating in the SayPro Monthly Plastic Chairs Training Course, attendees will be equipped with the critical knowledge and skills necessary to thrive in the competitive world of plastic chair manufacturing. The course will also provide valuable insights into how strategic partnerships and the adoption of advanced technologies can elevate business performance and market position.
Certification: Upon completion of the course, participants will receive a certification that validates their understanding of the plastic chair manufacturing industry and their ability to apply this knowledge in a practical setting.