Your cart is currently empty!
Author: Tumelo Seilaneng Mogorosi
SayPro is a Global Solutions Provider working with Individuals, Governments, Corporate Businesses, Municipalities, International Institutions. SayPro works across various Industries, Sectors providing wide range of solutions.
Email: info@saypro.online Call/WhatsApp: Use Chat Button ๐
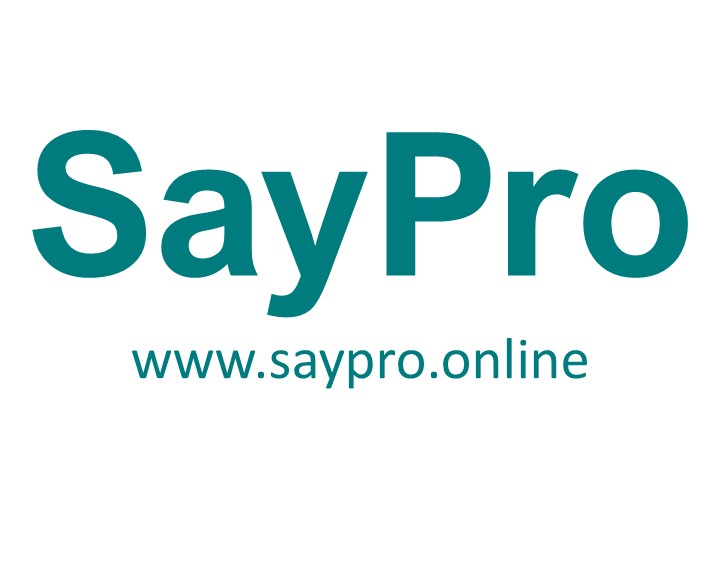
-
SayPro Certificate of Completion Template
SayPro Plastic Chair Manufacturing Training Course – Certificate of Completion Template
Certificate of Completion
SayPro Logo (Place logo here)
This is to certify that
[Participant Full Name]
(Participant ID: [ID Number])
Has successfully completed the
SayPro Plastic Chair Manufacturing Training Course
Course Overview:
This course provided in-depth knowledge and practical experience in the plastic chair manufacturing process. The participant has demonstrated proficiency in the key concepts, machinery, production processes, quality control, troubleshooting, and safety protocols necessary for successful operation in the plastic chair manufacturing industry.
Course Duration:
Start Date: [Start Date]
End Date: [End Date]
Instructor:
[Instructor Name]
[Instructor Title]
Course Modules Completed:
- Introduction to Plastic Chair Manufacturing
- Understanding Plastic Manufacturing Machines
- Raw Materials and Material Selection
- The Plastic Chair Manufacturing Process
- Quality Control and Assurance
- Machine Maintenance and Troubleshooting
- Safety Protocols and Environmental Compliance
- Post-Manufacturing Packaging and Distribution
Certificate Verification:
This certificate is verifiable through the official SayPro website at: [Website Link]
Authorized Signature:
[Instructor Name]
[Instructor Title]
SayPro Strategic Partnerships Office
Certificate Issue Date:
[Issue Date]
Design Layout Details:
- Header:
- Place SayPro logo at the top center.
- Course title: “Certificate of Completion” in a bold, professional font below the logo.
- The words “SayPro Plastic Chair Manufacturing Training Course” as the main certificate title.
- Body:
- Participant’s full name should be displayed prominently, in larger font size, followed by their participant ID.
- Include the course description/overview of the training in clear, concise text.
- Details of the course duration and instructorโs name.
- Footer:
- SayProโs contact information, website for verification, and a small logo or watermark of the SayPro brand.
- Include space for the instructor’s signature and the authorized signatory.
- Color Scheme:
- Primary Colors: Professional tones such as navy blue, dark gray, or silver.
- Accent Colors: Lighter hues for contrast, like light gray or white.
- Certificate Border: A clean, simple border to make the certificate look polished and formal.
- Font Style:
- Use serif fonts for the title and header (e.g., Times New Roman, Georgia) to give a formal and academic feel.
- Sans-serif fonts for the body text (e.g., Arial, Helvetica) for readability.
- Certificate Size:
- Standard A4 size (210mm x 297mm) to ensure compatibility with printing.
This certificate of completion template can be customized for each participant, allowing SayPro to acknowledge their successful participation and achievement in the Plastic Chair Manufacturing Training Course. The professional design reflects the value and credibility of the training provided.
-
SayPro Course Title
SayPro Plastic Chair Manufacturing Training Course – Course Outline Template
Course Title: Plastic Chair Manufacturing Training Course
Course Overview:
This course is designed to provide participants with a comprehensive understanding of the plastic chair manufacturing process, from raw material selection to machine operation, quality control, troubleshooting, and safety protocols. Participants will gain practical experience and insights into the modern production methods used in the plastic chair industry.
Course Duration:
Total Duration: [Number of Days/Weeks]
Delivery Format: [Online/In-Person/Hybrid]
Sessions per Week: [Number of Sessions per Week]
Session Length: [Hours per Session]
Start Date: [Start Date]
End Date: [End Date]
Course Modules:
Module 1: Introduction to Plastic Chair Manufacturing
- Objective: Provide a broad overview of the plastic chair manufacturing industry, including market trends, types of plastic chairs, and production demands.
- Topics Covered:
- History and evolution of plastic chair manufacturing
- Market trends and consumer demands
- Types of plastic chairs and their uses
- Key challenges in the manufacturing process
Module 2: Understanding Plastic Manufacturing Machines
- Objective: Introduce participants to the various machines used in plastic chair manufacturing.
- Topics Covered:
- Overview of injection molding machines
- Understanding blow molding and extrusion machines
- Functions and applications of each machine type
- Basic operation principles
Module 3: Raw Materials and Material Selection
- Objective: Teach the importance of raw material selection and its impact on the final product.
- Topics Covered:
- Types of plastic materials (e.g., polypropylene, polyethylene)
- Material properties and how they affect chair quality
- Material sourcing and sustainability
- Cost considerations and quality control
Module 4: The Plastic Chair Manufacturing Process
- Objective: Provide an in-depth understanding of the step-by-step process involved in manufacturing plastic chairs.
- Topics Covered:
- Overview of the production process from raw material to finished product
- Injection molding process (steps, equipment, and control)
- Blow molding and extrusion processes
- Cooling, assembly, and finishing
Module 5: Quality Control and Assurance
- Objective: Focus on maintaining product quality through effective quality control measures.
- Topics Covered:
- The role of quality control in manufacturing
- Common defects and how to identify them
- Testing and inspection techniques
- Ensuring product durability and safety
Module 6: Machine Maintenance and Troubleshooting
- Objective: Equip participants with the skills to maintain and troubleshoot plastic manufacturing machines.
- Topics Covered:
- Routine maintenance practices
- Preventing common machine failures
- Troubleshooting techniques
- Managing machine downtime and repairs
Module 7: Safety Protocols and Environmental Compliance
- Objective: Educate participants on the importance of safety in the manufacturing environment and compliance with environmental regulations.
- Topics Covered:
- Workplace safety measures and regulations
- Machine safety features and operator protocols
- Environmental impact of plastic manufacturing
- Compliance with legal and environmental standards
Module 8: Post-Manufacturing Packaging and Distribution
- Objective: Provide insights into the packaging and distribution of finished plastic chairs.
- Topics Covered:
- Packaging techniques for plastic chairs
- Storage and handling of finished goods
- Distribution logistics and supply chain considerations
- Packaging for durability and sustainability
Assessment and Certification:
- Assessment Method:
- Quizzes at the end of each module
- Mid-course test (covering Modules 1-4)
- Final test (covering Modules 1-8)
- Practical exercises (hands-on machine operation, troubleshooting)
- Certification Criteria:
- Participants must achieve at least a 70% score on all assessments and practical exercises to receive the SayPro Certificate of Completion.
Additional Resources:
- Course Materials:
- Presentations, handouts, videos, and manuals will be provided to participants at the beginning of the course.
- Supplemental Learning:
- Access to online forums for discussions and Q&A.
- Additional reading materials and videos on advanced manufacturing techniques.
Instructor Information:
- Instructor Name: [Instructor Name]
- Instructor Bio: [Instructor Short Bio]
Course Schedule:
Week Module Topics Covered Assessment Due Week 1 Module 1: Introduction to Plastic Chair Manufacturing Overview of the plastic chair industry, market trends, types of chairs Quiz on Module 1 Week 1 Module 2: Understanding Plastic Manufacturing Machines Types of machines, injection molding, blow molding, extrusion Week 2 Module 3: Raw Materials and Material Selection Material properties, sourcing, cost considerations Quiz on Module 2 Week 2 Module 4: The Plastic Chair Manufacturing Process Injection molding process, blow molding, extrusion, cooling Mid-course Test (Modules 1-4) Week 3 Module 5: Quality Control and Assurance Defects, inspection, testing techniques Quiz on Module 3 Week 3 Module 6: Machine Maintenance and Troubleshooting Maintenance practices, troubleshooting techniques Week 4 Module 7: Safety Protocols and Environmental Compliance Workplace safety, environmental compliance Quiz on Module 4 Week 4 Module 8: Post-Manufacturing Packaging and Distribution Packaging techniques, distribution logistics Final Test (Modules 1-8)
Conclusion:
By the end of this course, participants will have gained a comprehensive understanding of the plastic chair manufacturing process, including theoretical knowledge, practical skills, and safety awareness, preparing them for a career in the industry or enhancing their current expertise.
This course outline template provides a clear structure for the SayPro Plastic Chair Manufacturing Training Course, ensuring that all key topics are covered and that participants have a roadmap for their learning journey.
-
SayPro Feedback Form
SayPro Plastic Chair Manufacturing Training Course – Participant Feedback Form
Thank you for completing the SayPro Plastic Chair Manufacturing Training Course!
We value your feedback and would appreciate your input on how we can improve the course for future participants. Please take a moment to fill out this feedback form.
1. Course Content and Structure
How would you rate the overall quality of the course content?
- Excellent
- Good
- Average
- Poor
Was the course content clear and easy to understand?
- Very clear
- Clear
- Somewhat clear
- Not clear at all
Did the course cover all the topics you expected?
- Yes
- No
(If no, please specify which topics were missing or need more coverage):- [Text Field]
How relevant was the course material to your professional or personal goals?
- Highly relevant
- Somewhat relevant
- Neutral
- Not relevant
2. Instructor Effectiveness
How would you rate the instructor’s knowledge of the subject matter?
- Excellent
- Good
- Average
- Poor
How effective were the instructor’s explanations and demonstrations?
- Very effective
- Effective
- Somewhat effective
- Not effective
Did the instructor encourage participation and interaction?
- Yes
- No
(If no, please provide suggestions for improvement):- [Text Field]
3. Course Delivery
How would you rate the overall delivery of the course (including online or in-person format)?
- Excellent
- Good
- Average
- Poor
Was the course pace appropriate for the content?
- Too fast
- Just right
- Too slow
How would you rate the quality of the course materials (presentations, videos, handouts)?
- Excellent
- Good
- Average
- Poor
Were the hands-on practical exercises helpful in reinforcing the course content?
- Very helpful
- Helpful
- Somewhat helpful
- Not helpful
4. Learning Environment
How would you rate the online or in-person learning environment (for virtual sessions: quality of platform, interaction, etc.)?
- Excellent
- Good
- Average
- Poor
If you attended in-person, how would you rate the facilities (comfort, space, equipment)?
- Excellent
- Good
- Average
- Poor
(If poor, please provide details):- [Text Field]
If you attended online, how would you rate the platform (ease of use, accessibility, technical support)?
- Excellent
- Good
- Average
- Poor
(If poor, please provide details):- [Text Field]
5. Overall Course Experience
How satisfied are you with the course overall?
- Very satisfied
- Satisfied
- Neutral
- Dissatisfied
What did you enjoy most about the course?
- [Text Field]
What areas do you think need improvement in the course?
- [Text Field]
Would you recommend this course to a colleague or peer?
- Yes
- No
(If no, please explain why):- [Text Field]
Do you feel more confident in your knowledge and skills in plastic chair manufacturing after completing this course?
- Yes, definitely
- Yes, somewhat
- Not really
- Not at all
6. Additional Comments
Please provide any additional feedback or suggestions for improving this training course:
- [Text Field]
Thank you for your valuable feedback!
Your input will help us enhance the quality of our training programs and improve the learning experience for future participants.
Submit Feedback
- [Submit Button]
This feedback form allows participants to provide detailed input on different aspects of the SayPro Plastic Chair Manufacturing Training Course, ensuring continuous improvement and a high-quality learning experience.
-
SayPro Certificate of Completion
Certificate of Completion
This is to certify that
[Participant Full Name]
(Participant ID: [ID Number])
Has successfully completed the
SayPro Plastic Chair Manufacturing Training Course
Course Overview:
This course provided comprehensive knowledge and hands-on experience in plastic chair manufacturing, including machine operation, production processes, quality control, troubleshooting, and safety protocols. By successfully completing all course requirements, [Participant Name] has demonstrated proficiency in the key aspects of the plastic chair manufacturing industry.
Course Duration:
[Start Date] to [End Date]
Issued on:
[Issue Date]
Course Modules Covered:
- Introduction to Plastic Chair Manufacturing
- Understanding Plastic Manufacturing Machines
- Raw Materials and Material Selection
- The Plastic Chair Manufacturing Process
- Quality Control and Assurance
- Machine Maintenance and Troubleshooting
- Safety Protocols and Compliance
- Post-Manufacturing Packaging and Distribution
Instructor:
[Instructor Name]
[Instructor Title]
Authorized Signature:
[SayPro Logo]
SayPro Strategic Partnerships Office
[Address]
[Contact Information]
Certificate Verification:
This certificate is verifiable through SayProโs official website at: [SayPro Website]
Note:
This certificate is awarded based on the successful completion of all modules, assessments, and practical exercises in the SayPro Plastic Chair Manufacturing Training Course. The participant has met the criteria set forth by SayPro and has shown proficiency in the subject matter.
Design Layout Elements:
- Header:
- SayPro logo at the top center.
- Title “Certificate of Completion” in bold and large font, centered beneath the logo.
- Body:
- Participant’s full name in large, bold text.
- Course details and dates in an easy-to-read font.
- List of modules covered in a bulleted format.
- Instructor’s name and signature area at the bottom.
- Footer:
- SayProโs contact information, website link for verification, and a small version of the SayPro logo.
- Certificate Color Scheme:
- Main colors: Professional shades like navy blue, silver, or dark green.
- Accent colors: Lighter shades for text and background.
- Border: Simple, clean border with a thin line around the edges.
This certificate is designed to be professional and visually appealing, while conveying the participantโs achievement in completing the training course. It serves as a formal recognition of the participantโs efforts and expertise in plastic chair manufacturing.
-
SayPro Plastic Chair Manufacturing Training Course
SayPro Plastic Chair Manufacturing Training Course – Participant Registration Form
Participant Information
- Full Name:
- [Text Field]
- Date of Birth:
- [Date Picker]
- Gender:
- Male
- Female
- Other
- Prefer not to say
- Contact Information:
- Phone Number:
- [Text Field]
- Email Address:
- [Text Field]
- Phone Number:
- Address:
- Street Address:
- [Text Field]
- City:
- [Text Field]
- State/Province:
- [Text Field]
- Postal Code:
- [Text Field]
- Country:
- [Text Field]
- Street Address:
- Preferred Mode of Training:
- Online (Webinars/Recorded Videos)
- In-Person (SayPro Headquarters/External Location)
Educational Background
- Highest Level of Education Completed:
- High School
- Associateโs Degree
- Bachelorโs Degree
- Masterโs Degree
- Other: [Text Field]
- Field of Study:
- [Text Field]
- Do you have any prior experience in manufacturing or industrial processes?
- Yes
- No
- [Text Field]
Course Preferences
- What are your primary goals for attending this course?
- Learn basic plastic chair manufacturing processes
- Gain hands-on experience with machinery
- Understand quality control and troubleshooting techniques
- Improve my skills for career advancement
- Other: [Text Field]
- Have you worked with plastic manufacturing machines before?
- Yes
- No
- Are you interested in certification upon successful completion of the course?
- Yes
- No
Payment Information (If applicable)
- Course Payment Method:
- Credit Card
- Bank Transfer
- PayPal
- Other: [Text Field]
- Payment Status:
- Paid
- Pending
Emergency Contact Information
- Emergency Contact Name:
- [Text Field]
- Emergency Contact Phone Number:
- [Text Field]
- Relationship to Emergency Contact:
- [Text Field]
Terms and Conditions
- Consent to Participate:
By submitting this form, I confirm that I understand and agree to SayProโs terms and conditions for this course, including the privacy policy and any applicable fees.
- I agree to the terms and conditions.
- Medical Conditions or Special Requirements (if applicable):
If you have any medical conditions or special requirements for participation, please provide details below. This information will help us accommodate your needs during the training.
- [Text Field]
Submit Registration
- Submit Form:
- [Submit Button]
Tracking Participant Progress
Once a participant registers, SayPro can track their progress throughout the course by recording their attendance, quiz/test scores, practical exercise performance, and overall completion status. Regular updates and reminders can be sent via email or through the SayPro website to ensure participants stay on track with their learning goals.
This registration form captures all the necessary participant details for course enrollment while allowing for streamlined tracking of progress and engagement throughout the SayPro Plastic Chair Manufacturing Training Course.
- Full Name:
-
SayPro Assessment Tools
SayPro Assessment Tools for Plastic Chair Manufacturing Training Course
1. Quizzes
Objective:
Quizzes will be used to assess participants’ understanding of key concepts covered in each module. They will focus on reinforcing the material and ensuring that the participants have grasped the foundational knowledge required for successful plastic chair manufacturing.Quiz Structure:
- Multiple Choice Questions (MCQs): To assess basic understanding of terminology and concepts.
- Example:
What is the most common plastic material used for injection molding of chairs?
a) Polyethylene
b) Polypropylene
c) PVC
d) Nylon
- Example:
- True/False Questions: To quickly check participants’ knowledge of key facts and industry practices.
- Example:
The blow molding process is typically used for manufacturing hollow plastic items. (True/False)
- Example:
- Short Answer Questions: To evaluate participants’ ability to explain concepts in their own words.
- Example:
Explain why material selection is crucial in plastic chair manufacturing.
- Example:
- Matching Questions: To assess the ability to link concepts with their corresponding definitions or applications.
- Example:
Match the machine type with its main function.- Injection Molding Machine โ a) Material mixing
- Blow Molding Machine โ b) Shaping hollow objects
- Extrusion Machine โ c) Shaping plastic into a continuous profile
- Example:
Quiz Frequency:
- Quizzes will be given at the end of each module to reinforce the topics discussed and ensure understanding before moving to the next subject.
2. Tests
Objective:
Tests will be used to evaluate a deeper understanding of the course content, focusing on broader knowledge and application of learned principles in a more comprehensive manner.Test Structure:
- Written Tests (Multiple sections):
- Theoretical Questions: These will assess participants’ knowledge on production trends, types of plastic chair designs, raw materials, and quality control.
- Example:
What are the key differences between injection molding and extrusion molding processes?
- Example:
- Case Study Analysis: Participants will be given a real-world scenario or case study involving plastic chair production. They will need to identify challenges, propose solutions, and justify their decisions.
- Example:
Given a situation where a batch of plastic chairs fails a durability test, explain the possible causes and suggest corrective actions.
- Example:
- Practical Application Questions: Participants will be asked how they would apply certain concepts or techniques in a manufacturing setting.
- Example:
You are tasked with troubleshooting an injection molding machine that is producing chairs with defects. What steps would you take to identify and fix the issue?
- Example:
- Theoretical Questions: These will assess participants’ knowledge on production trends, types of plastic chair designs, raw materials, and quality control.
Test Frequency:
- A mid-course test will be given after modules 4 and 5 (covering the production process and quality control).
- A final test will be administered at the end of the course, evaluating all topics covered throughout the course.
3. Practical Exercises
Objective:
Practical exercises are designed to evaluate participants’ ability to apply their theoretical knowledge in hands-on manufacturing tasks. These exercises will focus on the real-world operation of machines, troubleshooting, and product quality assessments.Types of Practical Exercises:
- Machine Operation Demonstrations:
Participants will be required to demonstrate basic operations of different types of machines used in plastic chair manufacturing (e.g., injection molding, extrusion). They will perform specific tasks under supervision to assess their competence with machine setup, operation, and maintenance.- Example:
Set up an injection molding machine to produce a basic chair seat component, ensuring the correct temperature and pressure settings.
- Example:
- Material Selection Exercise:
Participants will select appropriate materials for a given chair design, considering factors like strength, flexibility, and cost.- Example:
Choose the right material for manufacturing a lightweight chair with high load-bearing capacity.
- Example:
- Quality Control Exercise:
Participants will be asked to inspect a batch of plastic chairs for defects such as cracks, uneven surfaces, or poor molding. They will then suggest corrective actions to address the issues.- Example:
Conduct a visual inspection of 20 plastic chairs and identify any defects that might compromise their quality. Explain your inspection process.
- Example:
- Troubleshooting Scenario:
In this exercise, participants will be provided with a malfunctioning machine or faulty batch of chairs. They will need to diagnose the issue and recommend or implement solutions.- Example:
A batch of chairs produced from the injection molding machine is coming out with uneven finishes. Identify possible causes and suggest solutions.
- Example:
Practical Exercise Frequency:
- Mid-course practical: A hands-on practical session will take place after modules 4 and 5, assessing skills in the production process and quality control.
- End-of-course practical: A final practical exam will assess the participant’s ability to complete the entire manufacturing process from material selection to final product inspection.
4. Participant Feedback and Self-Assessment
Objective:
Feedback and self-assessment provide participants with the opportunity to evaluate their own progress and highlight areas for improvement.Feedback Methods:
- Self-Assessment Surveys: At the beginning and end of the course, participants will complete self-assessment surveys to evaluate their perceived progress and confidence in various areas of plastic chair manufacturing.
- Example Questions:
How confident are you in using the injection molding machine after completing the course?
Rate your understanding of quality control procedures in plastic chair production.
- Example Questions:
- Instructor Feedback: Continuous feedback will be provided during the course to address any participant challenges and help them refine their skills.
- Peer Feedback (if applicable): In group activities or case study discussions, participants will give and receive feedback on the work of their peers, fostering collaboration and learning.
Assessment Timeline:
Activity Timing Purpose Quiz (Module 1-3) End of each module Assess understanding of core concepts. Mid-course Test End of Week 2 (Modules 4-5) Evaluate comprehensive knowledge of process and quality control. Practical Exercises (Modules 4-5) End of Week 2 Assess hands-on proficiency with machines and quality control. Final Test End of course (Week 4) Evaluate knowledge across all topics. Final Practical Exam End of course (Week 4) Assess full manufacturing process understanding.
5. Grading and Certification:
- Assessment Weighting:
- Quizzes: 20% of final grade
- Mid-course Test: 25% of final grade
- Practical Exercises: 25% of final grade
- Final Test: 20% of final grade
- Participation and Engagement: 10% of final grade
- Certification Criteria:
- Participants must score at least 70% on quizzes, tests, and practical exercises combined.
- Successful completion of the practical exercises and final exam is required to receive the SayPro Certificate of Completion.
By utilizing a diverse set of assessment tools, SayPro ensures that participants are not only evaluated on their theoretical knowledge but also on their ability to apply these concepts effectively in practical scenarios. This comprehensive assessment approach will provide participants with a solid foundation for success in the plastic chair manufacturing industry.
- Multiple Choice Questions (MCQs): To assess basic understanding of terminology and concepts.
-
SayPro Plastic Chair Manufacturing Training Course Syllabus
SayPro Plastic Chair Manufacturing Training Course Syllabus
Course Title:
SayPro Monthly Plastic Chair Manufacturing Training Course
Course Duration:
4 Weeks (or as specified)
Mode of Delivery:
- Online (Webinars/Recorded Videos)
- In-Person (SayPro Headquarters or External Locations)
Course Objective:
The primary objective of this training course is to equip participants with the knowledge and practical skills needed to successfully understand and implement plastic chair manufacturing processes. Participants will learn about the raw materials, machines, production processes, quality control, and safety protocols necessary for producing high-quality plastic chairs. By the end of the course, participants will have a strong foundation in manufacturing principles and hands-on experience in machine operation, assembly, and troubleshooting.
Syllabus Outline:
Module 1: Introduction to Plastic Chair Manufacturing
- Objective: Understand the basics of plastic chair production and market dynamics.
- Overview of the plastic chair manufacturing industry.
- Analysis of current production trends and market demands.
- Key drivers of innovation in plastic chair designs.
- The role of plastics in furniture manufacturing.
- Industry standards and regulations.
Module 2: Understanding Plastic Manufacturing Machines
- Objective: Gain knowledge about the machines used in plastic chair manufacturing.
- Types of plastic manufacturing machines:
- Injection Molding Machines: Operation and applications.
- Blow Molding Machines: Operation, materials, and usage.
- Extrusion Machines: Functions and impact on production.
- Introduction to machine components and their roles in the manufacturing process.
- Basic machine operation and maintenance.
- Types of plastic manufacturing machines:
Module 3: Raw Materials and Materials Selection
- Objective: Learn about the key raw materials and their impact on chair quality.
- Types of plastics used in chair manufacturing (e.g., polyethylene, polypropylene).
- Criteria for selecting materials based on strength, flexibility, and cost.
- Material processing techniques and preparation.
- Managing supply chain and inventory for raw materials.
Module 4: The Plastic Chair Manufacturing Process
- Objective: Walk through the entire plastic chair production process.
- Step-by-step production process:
- Raw material selection and preparation.
- Molding (Injection molding, blow molding, etc.).
- Cooling and solidification of molded pieces.
- Assembly of components (legs, seat, backrest).
- Finishing: Cutting, trimming, painting, or other final treatments.
- Factors affecting production speed and quality control.
- Step-by-step production process:
Module 5: Quality Control and Assurance
- Objective: Understand the importance of ensuring product quality at each stage.
- Quality control techniques: Visual inspections, measurement tools, and stress testing.
- Importance of mold design and material selection in quality.
- Procedures for testing finished products for durability, safety, and comfort.
- Common defects and troubleshooting strategies.
Module 6: Machine Maintenance and Troubleshooting
- Objective: Learn best practices for keeping machines in optimal working condition.
- Preventive maintenance schedules for key machines.
- Troubleshooting common machine issues (e.g., injection molding machine failures, material jams).
- Lubrication and parts replacement procedures.
- Ensuring machine efficiency to reduce production downtime.
Module 7: Safety Protocols and Compliance
- Objective: Ensure that manufacturing operations are safe and compliant with environmental standards.
- Importance of safety in manufacturing: Machine safety, worker safety, and accident prevention.
- Adherence to environmental compliance and regulations.
- Personal protective equipment (PPE) required in the manufacturing environment.
- Training on fire safety, chemical handling, and emergency procedures.
Module 8: Best Practices in Plastic Chair Design and Innovation
- Objective: Learn about innovative design principles for producing ergonomic and market-competitive chairs.
- Key principles of ergonomics and design considerations in chair manufacturing.
- Impact of material choices on product design.
- Trends in design: Sustainability, eco-friendly materials, and aesthetics.
- Prototyping and CAD (Computer-Aided Design) software used for design modeling.
Module 9: Post-Manufacturing: Packaging and Distribution
- Objective: Understand how chairs are packaged and prepared for distribution.
- Best practices for packaging plastic chairs to prevent damage during transit.
- Logistics: Managing transportation and delivery.
- Understanding supply chain and how it affects delivery timelines.
- Customer return policies and handling complaints.
Evaluation Criteria:
- Quizzes and Written Tests: Following each module, a quiz or test will assess participants’ theoretical knowledge.
- Practical Assignments: Hands-on activities will assess the participantsโ practical skills.
- Final Assessment: A comprehensive exam covering all course material will be held at the end of the course.
- In-class Participation: Engagement in discussions, group activities, and case studies will be evaluated.
Learning Outcomes:
Upon completing the course, participants will be able to:
- Understand the full plastic chair manufacturing process from raw material selection to assembly.
- Operate key manufacturing machines such as injection molding, blow molding, and extrusion machines.
- Ensure quality control in production and troubleshoot machine malfunctions.
- Maintain safety protocols and comply with industry standards.
- Contribute to chair design and innovation efforts in manufacturing settings.
Prerequisites:
No prior knowledge or experience in manufacturing is required. However, participants should have basic mathematical skills (for measurements) and an interest in industrial processes.
Certification:
Upon successful completion of the course, including passing all assessments, participants will be awarded a SayPro Certificate of Completion in Plastic Chair Manufacturing.
This syllabus provides a comprehensive outline of the SayPro Monthly Plastic Chair Manufacturing Training Course. It ensures that participants will gain both theoretical knowledge and practical skills essential for success in the plastic chair manufacturing industry.
-
SayPro Evaluation and Certification Process
SayPro Evaluation and Certification Process for Plastic Chair Manufacturing Course
The evaluation and certification process is a critical component of SayProโs Plastic Chair Manufacturing Training Course. It ensures that participants not only understand the course material but can also apply their knowledge effectively in real-world scenarios. Below is a detailed outline of how the evaluation and certification will be carried out.
1. Participant Evaluation
To assess the participants’ understanding and mastery of the material, a structured evaluation process will be implemented. This will involve multiple stages, ensuring a comprehensive assessment of each participantโs skills and knowledge.
A. Evaluation Methods
1. Quizzes and Tests
- Regular quizzes will be administered after each module to test participantsโ knowledge and comprehension of the key concepts covered.
- Final Test/Exam: A comprehensive final exam will be conducted, covering all aspects of the plastic chair manufacturing process, including:
- Raw materials
- Manufacturing machines
- Production process
- Quality control techniques
- Safety protocols
2. Practical Assignments
- Hands-on assessments or simulated exercises will be given to participants to evaluate their ability to apply learned concepts in real-world scenarios.
- Example: Designing a basic plastic chair prototype using the correct materials or outlining the step-by-step process for molding a chair.
3. Group Discussions and Case Studies
- Participants will be assessed based on their engagement in group discussions and their ability to analyze real-life case studies related to plastic chair manufacturing.
- Example: Working in teams to identify key challenges in a plastic chair factory and suggesting solutions.
4. Instructor Observations
- Throughout the course, instructors will observe participants’ participation in discussions, group activities, and demonstrations to evaluate engagement, communication skills, and practical knowledge application.
B. Progress Tracking
- Participants’ performance will be tracked through the SayPro course platform to monitor completion rates, quiz scores, and participation in activities.
- Instructors will provide regular feedback on participantsโ progress, indicating areas for improvement or areas where the participant excels.
C. Ongoing Feedback
- Continuous feedback will be provided to participants during interactive Q&A sessions and follow-up assessments, allowing them to clarify doubts and ensure they are on track to pass.
2. Certification Process
Once the participants have successfully completed the course and demonstrated their knowledge and skills, they will be eligible to receive a certificate of completion. Hereโs how the process works:
A. Requirements for Certification
To receive a SayPro Certification in Plastic Chair Manufacturing, participants must:
- Complete all course modules and attend a minimum number of training hours (whether online or in-person).
- Achieve a passing score on quizzes and the final exam (e.g., 70% or higher).
- Submit any required practical assignments or participate in practical exercises and demonstrate proficiency in key manufacturing processes.
- Participate in group discussions and case studies (for in-person courses).
B. Certification Issuance
Once the participant has met all requirements, SayPro will issue certificates of completion, which may include:
- Electronic Certificates: A digital certificate will be issued, which participants can download from the SayPro platform. The digital certificate will be shareable and printable for participants’ professional use.
- Physical Certificates (for in-person training): A physical certificate can be mailed or handed out to participants at the conclusion of the course.
C. Certificate Details
The certificate will include:
- Participantโs full name
- Course title: Plastic Chair Manufacturing Training
- Date of completion
- SayPro logo and signature of the course facilitator
- Course completion score (if applicable)
- A unique certificate number for verification purposes
3. Post-Certification Support
A. Continuing Education
- After certification, participants will be encouraged to continue their professional development through advanced workshops or follow-up courses related to other aspects of plastic manufacturing or machine operation.
B. Alumni Network
- Participants who have completed the course will be invited to join SayProโs Alumni Network, where they can access exclusive resources, job opportunities, and networking events.
C. Feedback Collection
- After completing the course, participants will be asked to complete a feedback survey regarding the course content, delivery method, and overall experience. This feedback will be used to improve future training sessions.
4. Monitoring and Reporting
A. Tracking Course Performance
- Instructors and course administrators will track overall course performance through the SayPro platform, reviewing participant completion rates and evaluation results to monitor trends and identify any areas of improvement for future courses.
B. Certification Verification
- Participants and employers can verify the authenticity of the certificate through a unique certification ID on SayProโs website or platform. This ensures that the certification is valid and issued by the authorized training provider.
Conclusion
By implementing a robust evaluation and certification process, SayPro ensures that participants are thoroughly assessed and provided with the necessary tools to succeed in the plastic chair manufacturing industry. This certification serves as proof of their competence and knowledge, empowering them to apply their skills in practical environments and enhancing their professional credentials.
-
SayPro Conducting Training Sessions
SayPro Conducting Training Sessions for the Plastic Chairs Manufacturing Course
Delivering training sessions effectively, whether online or in-person, is crucial for providing participants with the knowledge and skills they need in plastic chair manufacturing. The goal is to ensure a seamless learning experience, keeping participants engaged and empowered to apply what theyโve learned. Below is a detailed plan for conducting training sessions for SayPro Monthly January SCSPR-98.
1. Preparing for the Training Sessions
Before delivering any sessions, it’s important to ensure all necessary materials, tools, and setups are in place, whether for online or face-to-face delivery.
A. Course Materials Preparation
Ensure that all training materials are ready for distribution and easily accessible for participants.
- Tasks:
- Slides & Presentations: Finalize PowerPoint presentations, ensuring they are visually appealing and informative, with clear bullet points, diagrams, and visuals.
- Instructional Videos: Have any pre-recorded instructional videos or tutorials ready for showing during the session.
- Handouts/Manuals: Prepare digital handouts or workbooks that participants can download and follow along with during the session.
- Quizzes & Assessments: Ensure that all quizzes, tests, and exercises are ready for use and can be easily accessed.
B. Technical Setup for Online Training
Ensure the technical setup for online training sessions is fully prepared.
- Tasks:
- Test Equipment: Test webcams, microphones, and internet connections before the session to ensure smooth delivery.
- Platform Familiarity: Familiarize yourself with the online platform being used (e.g., Zoom, Microsoft Teams, etc.) and ensure participants can easily access the meeting link and course materials.
- Interactive Tools: Set up tools for engagement, such as polls, Q&A sessions, and breakout rooms for group discussions.
- Backup Plan: Prepare for potential technical issues by having a backup plan (e.g., alternative contact methods or platform).
C. Room Setup for In-Person Sessions
For face-to-face sessions, make sure the room is properly set up for a productive learning environment.
- Tasks:
- Seating Arrangement: Arrange seating to encourage interaction, such as U-shaped or round tables for group discussions.
- Audio/Visual Equipment: Ensure that projectors, whiteboards, or flip charts are in place for presentations and discussions.
- Safety Measures: Ensure safety protocols are followed (e.g., social distancing, masks, sanitation stations) if necessary, especially for in-person sessions.
2. Delivering the Training Sessions
The core of the training is the engagement and effective delivery of course content. Whether you’re teaching online or face-to-face, maintaining participant engagement and providing clear explanations are key components of success.
A. Online Session Delivery
For online training, ensure that participants are actively engaged and can follow along easily.
- Tasks:
- Introductions: Start with a welcome message and introduce the course agenda. Ensure participants understand the course flow and objectives.
- Presenting Course Material: Use slides and visual aids to break down complex topics such as plastic chair manufacturing processes, machine types, and material selection.
- Interactive Elements: Incorporate tools like polls, chatboxes, and Q&A to encourage active participation. Regularly check the chat for any questions.
- Breakout Rooms: For group exercises or discussions, use breakout rooms to give participants a chance to collaborate and share insights in smaller groups.
- Hands-on Demonstrations: If possible, show virtual simulations or provide live demonstrations of the manufacturing processes to enhance understanding.
- Engagement Checkpoints: Frequently check in with participants by asking open-ended questions, requesting feedback, or conducting short quizzes to assess comprehension.
- Wrap-Up: Conclude with a recap of key points and allow time for any last-minute questions.
B. Face-to-Face Session Delivery
For in-person training, personal interaction is key. Ensure the atmosphere is conducive to learning and interaction.
- Tasks:
- Icebreaker Activities: Start with an icebreaker or introduction activity to engage participants and create a comfortable learning environment.
- Group Discussions: Encourage group discussions around case studies, real-world examples, or manufacturing challenges. Facilitate the exchange of ideas and experiences.
- Hands-on Demonstrations: Whenever possible, demonstrate machinery operation or molding processes live. Allow participants to get hands-on experience, either through mock demonstrations or by guiding them through practical exercises.
- In-Session Assessments: Incorporate small, on-the-spot quizzes or group exercises to reinforce concepts. Use visual aids, such as diagrams, charts, and models, to illustrate processes clearly.
- Interactive Sessions: Engage participants by encouraging them to ask questions and share their own experiences with the group.
- Live Q&A: At the end of each session or module, allow time for a Q&A session where participants can ask questions or clarify doubts related to the material.
3. Managing Participant Engagement
A. Online Engagement
Maintain an engaging environment for virtual learners, keeping them focused and involved.
- Tasks:
- Polls & Surveys: Use interactive tools like polls or surveys to keep participants engaged. Ask questions related to the course material and use the results to gauge understanding.
- Real-Time Interaction: Use the chatbox to allow participants to ask questions or comment during the session. Acknowledge contributions to keep discussions flowing.
- Gamification: Integrate gamified elements (e.g., quizzes, points, leaderboards) to make learning fun and encourage friendly competition.
- Live Demonstrations: Use screen-sharing tools to demonstrate software, simulations, or other visual content to make the material more digestible.
B. In-Person Engagement
Foster a dynamic and interactive in-person session where participants feel comfortable engaging.
- Tasks:
- Group Activities: Facilitate group activities or pair work to encourage collaboration. Have groups present their findings or insights to the larger group.
- Interactive Demonstrations: Allow participants to actively engage with physical models or molding machines during the session.
- Feedback Loops: After every segment or demonstration, ask participants for feedback to ensure theyโre grasping the concepts.
- Discussion Encouragement: Invite participants to share experiences or thoughts on the challenges and successes theyโve had in manufacturing. This helps foster a learning community.
4. Wrapping Up the Session
Conclude each session by summarizing key points, offering participants next steps, and encouraging further learning.
A. Online Wrap-Up
In online training sessions, wrap up with a clear, concise conclusion and next steps for participants.
- Tasks:
- Summarize Key Points: Review the main takeaways from the session to ensure clarity.
- Encourage Continued Engagement: Provide participants with additional resources such as reading material, recorded videos, or follow-up webinars.
- Ask for Feedback: Encourage participants to fill out a feedback form or survey to understand their learning experience and identify areas for improvement.
- Certifications: Remind participants about the certification process and how they can access their certificates upon completion.
B. In-Person Wrap-Up
For in-person sessions, close with a reflective activity and ensure that participants feel confident about applying what theyโve learned.
- Tasks:
- Group Reflection: Conduct a closing circle where participants reflect on what theyโve learned and how they plan to apply the skills in their roles.
- Takeaway Materials: Provide printed materials or additional resources to reinforce learning after the session.
- Networking Opportunity: Allow time for informal networking where participants can connect with each other and share insights.
- Post-Course Survey: Offer a feedback survey for participants to complete after the session to improve future training programs.
5. Post-Session Support
After the training session, continue providing value and support to participants.
A. Online Support
Offer additional support channels for participants, such as email support, follow-up Q&A sessions, or online discussion forums.
- Tasks:
- Email Follow-Ups: Send out follow-up emails with resources, additional training materials, and reminders of key learning points.
- Online Discussion Forums: Set up an online forum or group chat (e.g., on platforms like Slack or Discord) where participants can continue discussions, ask questions, and share their experiences.
B. In-Person Support
Provide ongoing support through personal contact or follow-up calls to ensure participants can apply the training in real-world scenarios.
- Tasks:
- One-on-One Consultations: Offer follow-up consultations for participants who need additional help or have specific questions.
- Continued Learning: Promote advanced workshops or follow-up courses for participants interested in expanding their skills further.
Conclusion
By delivering engaging and well-structured training sessions for both online and in-person formats, SayPro can create a comprehensive, effective learning experience for all participants. Maintaining engagement, ensuring clear explanations, and fostering a collaborative environment will help participants gain valuable skills in plastic chair manufacturing.
- Tasks:
-
SayPro Scheduling and Registration System
SayPro Scheduling and Registration System for Plastic Chairs Manufacturing Training Course
To effectively manage participant sign-ups and course scheduling for both online and in-person sessions of the Plastic Chairs Manufacturing Training Course, an online registration system is essential. This system must be user-friendly, efficient, and flexible to handle various participant needs. Here is a detailed plan for setting up and managing the SayPro Monthly January SCSPR-98 courseโs registration process.
1. Set Up an Online Registration System
The online registration system will be the primary tool for handling course enrollments, payment processing, and communication with participants.
A. Choose the Right Platform
Select an online registration platform that integrates well with SayProโs website, supports secure payment processing, and is flexible enough for managing both online and in-person courses. Popular options include Eventbrite, Acuity Scheduling, Cvent, or a custom registration system embedded directly into SayProโs website.
- Tasks:
- Platform Integration: Ensure the registration platform integrates with SayProโs website and CRM (customer relationship management) tools to streamline participant communication and data management.
- Mobile Compatibility: Choose a platform that works seamlessly across desktop and mobile devices to ensure accessibility for all potential participants.
- Security: Verify that the platform uses SSL encryption for secure transactions and complies with data protection regulations (e.g., GDPR) for safeguarding personal information.
B. Course Calendar and Schedule Setup
Set up a detailed course calendar and define key details such as the course start and end dates, sessions, and available time slots (for both online and in-person).
- Tasks:
- Online Course Dates: Specify the start date, duration, and time zone for the online course sessions.
- In-Person Sessions: Define dates, times, and venue for in-person training at SayProโs headquarters or any external locations.
- Time Zone Adjustments: For international participants, ensure the system automatically adjusts the time zone to match their location.
- Availability Limits: Set a cap on the number of participants for each session to avoid overcrowding, particularly for in-person courses.
- Real-Time Availability: Enable real-time updates so that participants can see the availability of specific dates or times and register for open slots.
C. Registration Form Design
Design a registration form that captures all necessary participant information while being quick and easy to fill out.
- Tasks:
- Personal Details: Include fields for name, email address, phone number, job title, and company (if applicable).
- Course Preference: Allow participants to choose their preferred course type (online or in-person) and preferred dates.
- Payment Information: Integrate payment options (credit card, PayPal, bank transfer) for course fees. If offering discounts or promotions, create input fields for discount codes.
- Special Requests: Add fields for any special accommodations (e.g., dietary needs, accessibility requirements) for participants attending in-person sessions.
- Terms and Conditions: Include a checkbox for participants to agree to the terms and conditions and privacy policy before completing registration.
D. Confirmation and Payment Processing
Once a participant completes the registration, the system should send an automatic confirmation email with course details and payment receipts.
- Tasks:
- Confirmation Email: Include a summary of course details (date, time, type), venue (for in-person courses), and a personalized greeting.
- Payment Receipt: Provide a receipt for the payment, including transaction details.
- Calendar Invite: Include an online calendar invite (e.g., for Google Calendar or Outlook) to help participants save the course date directly.
- Pre-Course Information: Share pre-course materials or a course prep guide in the confirmation email so participants can start preparing ahead of the course.
2. Manage Participant Sign-Ups for Online and In-Person Courses
To effectively manage both online and in-person courses, it’s important to organize and track participant registrations and communicate with attendees in advance.
A. Track Registrations
Ensure that the system tracks registrations in real-time, allowing you to monitor participant progress and adjust schedules as needed.
- Tasks:
- Monitor Enrollment Numbers: Track the number of participants in each session and ensure that no session exceeds the set capacity.
- Waitlist Management: Set up an automated waitlist for fully booked courses, allowing additional participants to be automatically enrolled if spots become available.
- Email Reminders: Set up automated email reminders for participants with important pre-course information, such as the agenda, venue details (for in-person courses), and login links (for online courses).
- Manage Refunds and Cancellations: Set up an easy-to-manage system for refund requests and course cancellations according to SayProโs policies.
B. Participant Communication
Effective communication is key to maintaining engagement and ensuring participants feel informed and prepared.
- Tasks:
- Confirmation Emails: After registration, send confirmation emails that include:
- A welcome message
- Course details (dates, times, venue/online link)
- Payment receipt
- What to expect next
- Pre-Course Reminders: Send an email reminder a few days before the course starts with details about:
- How to join the online course (including links to webinars or virtual sessions)
- Where to go for in-person sessions (location, directions, parking, etc.)
- Required materials or equipment (e.g., laptops, pens, notebooks)
- Post-Course Follow-Up: Send a follow-up email after the course to gather feedback and offer certificates of completion. Also, mention future courses or additional resources available to participants.
- Confirmation Emails: After registration, send confirmation emails that include:
C. Handling Multiple Course Formats (Online & In-Person)
To streamline operations for both online and in-person courses, make sure the system allows easy management of both formats.
- Tasks:
- Online Course Access: For online participants, provide clear access instructions (e.g., Zoom links, login details) and ensure that the virtual platform is user-friendly.
- In-Person Session Check-In: For in-person courses, implement an event check-in system where participants can sign in when they arrive at the venue, either using QR codes or manually.
- Interactive Course Schedules: Use a dynamic schedule on the registration page that clearly distinguishes between online and in-person courses, showing which slots are available for each.
3. Optimize for Different Participant Groups
For maximum efficiency, tailor the registration system to accommodate different types of participants, such as corporate groups, individuals, or existing clients.
A. Corporate Group Registrations
Allow companies to register multiple employees for the course with a group discount or special package.
- Tasks:
- Group Registration Option: Create a bulk registration option where companies can sign up multiple participants at once, including a discounted rate for larger groups.
- Custom Invoicing: Enable custom invoicing for companies registering multiple employees, making it easier for them to manage payments.
- Corporate Communication: Offer the option for group coordinators to receive group-specific communications (e.g., a dedicated email with an overview of all enrolled participants).
B. Special Discounts or Early Bird Rates
Incentivize early sign-ups or offer special pricing to increase registrations.
- Tasks:
- Discount Codes: Integrate discount codes or early-bird pricing options to encourage early sign-ups or to offer special deals to specific groups.
- Promotions for Returning Participants: Provide loyalty discounts for previous participants or those who register for multiple courses.
C. Accessibility Features
Ensure the registration system accommodates individuals with specific needs, especially those attending in-person courses.
- Tasks:
- Accessibility Options: Include options for special accommodations such as wheelchair access or dietary preferences for in-person events.
- Language Options: Offer multi-language registration options for international participants or non-native speakers.
4. Post-Registration Management
After the registration period is over, it is essential to manage participant data, send reminders, and track attendance.
A. Attendance Tracking
Track attendance for both online and in-person sessions to ensure all participants attend.
- Tasks:
- In-Person Check-In: Use a QR code scanner or a manual check-in list to ensure all participants have attended in-person courses.
- Online Attendance: For virtual sessions, monitor attendance by tracking logins, video participation, or chat engagement during the course.
B. Provide Certificates of Completion
Offer certificates to participants who meet the course requirements.
- Tasks:
- Certificate Generation: Automate certificate generation at the end of the course for participants who successfully complete all requirements.
- Email Distribution: Send digital certificates via email with an option to download or print for participants who complete the course.
Conclusion
By implementing a well-organized and efficient online registration system, SayPro can ensure a smooth experience for participants enrolling in both online and in-person sessions of the Plastic Chairs Manufacturing Training Course. The system should streamline participant registration, payment processing, communication, and post-course follow-up. With these systems in place, SayPro can efficiently manage enrollments, enhance participant satisfaction, and drive successful course outcomes.
- Tasks: