Your cart is currently empty!
SayPro Prepare the schedule for the month’s laboratory activities and ensure that all necessary equipment and materials are available.
SayPro is a Global Solutions Provider working with Individuals, Governments, Corporate Businesses, Municipalities, International Institutions. SayPro works across various Industries, Sectors providing wide range of solutions.
Email: info@saypro.online Call/WhatsApp: Use Chat Button 👇
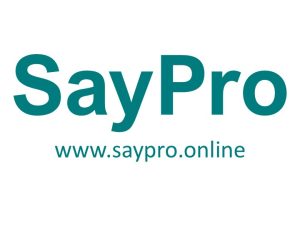
Preparing the schedule for the month’s laboratory activities and ensuring that all necessary equipment and materials are available is a critical responsibility for SayPro. The smooth operation of laboratory activities depends on meticulous planning, coordination, and timely execution. This process involves not only organizing the lab’s schedule but also ensuring that resources are properly allocated, equipment is maintained, and all safety protocols are followed.
Here’s a detailed, step-by-step guide on how to prepare the schedule for the month’s laboratory activities and ensure that all necessary equipment and materials are available:
1. Review Objectives for the Month
a) Understand the Scope of Laboratory Activities
Start by gaining a clear understanding of the goals and activities planned for the laboratory in the upcoming month. These could include:
- Research projects: New experiments, ongoing research, or new product testing.
- Product testing: Testing prototypes, quality control, or performance validation.
- Training: Employee or team training on new equipment or processes.
- Safety inspections: Ensuring that lab equipment and processes meet safety standards.
- Collaborative efforts: Working with external researchers, partners, or departments.
Understanding the focus of each activity helps allocate time, space, and resources accordingly.
2. Prepare the Laboratory Activity Schedule
a) Identify Key Dates and Deadlines
- Monthly milestones: Identify key deadlines for projects, reports, or research results due during the month. Make note of these in the schedule.
- Routine activities: Regular tasks like equipment calibration, maintenance, or safety checks.
- Meetings and reviews: Include any meetings with internal teams, external partners, or safety audits.
Example:
- Week 1: Product testing for prototype A
- Week 2: Research project on chemical reactions under temperature stress
- Week 3: Calibration of testing equipment and regular safety checks
- Week 4: Employee training session on the new spectrometer
b) Prioritize Activities
Consider the priority of each activity:
- Urgent vs. Non-Urgent: Are there any time-sensitive tasks that need to take precedence? For example, product testing might take priority over routine safety checks.
- Dependencies: Some activities may rely on others being completed first. For instance, product testing cannot proceed without the completion of prototype development.
Align activities based on their dependencies and urgency.
c) Time Allocation
- Estimate Duration: For each activity, estimate the time required, ensuring that enough time is allocated for each task. This includes setup time, actual work time, and cleanup time.
- Buffer Time: Include buffer time in the schedule for unexpected delays or overruns.
Example:
- Research project: 8 hours per day, Monday to Wednesday (total 24 hours)
- Equipment calibration: 4 hours on Thursday
d) Assign Responsible Personnel
Determine who will be responsible for each activity. Ensure that the right personnel with the required expertise are assigned to the tasks. This includes:
- Researchers for specific experiments.
- Technicians for maintenance or calibration.
- Safety officers for conducting safety checks.
Include their contact details and working hours in the schedule for easy coordination.
e) Create the Calendar
Using the information gathered, organize the activities into a calendar format:
- Daily Schedule: Display each day’s planned activities with the times allocated for each.
- Weekly Overview: Show an overview of all activities for the week, so it’s easy to see overlaps and plan for resource usage.
You can create this schedule using tools such as:
- Spreadsheets (Google Sheets, Microsoft Excel) for easy sharing and tracking.
- Project Management Tools (Trello, Asana, Microsoft Project) for more complex scheduling and task tracking.
3. Ensure Equipment and Materials Availability
a) List Required Equipment and Materials
For each laboratory activity, create a detailed list of the equipment, tools, and materials needed:
- Consumables: Reagents, chemicals, testing materials, or any disposable items required for experiments.
- Specialized Equipment: Instruments like spectrometers, centrifuges, or any other machinery.
- Safety Equipment: Personal protective equipment (PPE), first-aid kits, eyewash stations, etc.
Ensure the list is comprehensive to avoid last-minute shortages.
Example Equipment List for Product Testing:
- Spectrometer
- Product samples (Prototype A)
- Calibration standards
- Computer with software for data collection
- Safety gloves, goggles, and lab coats
b) Check Inventory and Availability
- Stock Review: Review the inventory to check whether all the materials are in stock and available for use. For any missing items, ensure they are ordered and delivered on time.
- Equipment Maintenance: Check the maintenance schedule for all equipment. If any equipment is due for servicing or calibration, plan it ahead of time to avoid delays. Arrange for spare parts if necessary.
Example:
- Ensure that the spectrometer used for product testing has been calibrated in the last six months.
- Check if there is enough stock of reagents for the research project and place any necessary orders.
c) Coordinate with Vendors and Suppliers
For materials that need to be sourced externally:
- Order in Advance: Place orders early to avoid delays in shipping. Consider lead times for items that need to be custom-made or sourced from specific vendors.
- Track Deliveries: Monitor the status of orders to ensure timely delivery. If items are delayed, make alternative arrangements or adjust the schedule.
d) Set Up an Equipment/Material Reservation System
For equipment that’s shared or used by multiple teams, set up a reservation system to prevent scheduling conflicts. This ensures that equipment is available when needed.
Example:
- Product Testing Team reserves the spectrometer from 9:00 AM to 12:00 PM, then the Research Team reserves it from 1:00 PM to 3:00 PM.
Use tools like:
- Google Calendar or Microsoft Outlook Calendar to manage reservations.
- Lab-specific software for scheduling equipment use.
4. Plan for Safety and Compliance
a) Review Safety Protocols
Each laboratory activity must follow established safety guidelines to ensure the safety of personnel and the integrity of experiments:
- Personal Protective Equipment (PPE): Ensure all team members have the appropriate PPE for the tasks they will be performing.
- Laboratory Safety Checklist: Review the safety checklist before starting each activity, covering items such as emergency exits, eyewash stations, fire extinguishers, and spill containment.
For high-risk activities (e.g., handling hazardous materials), ensure that proper safety procedures are in place.
b) Schedule Safety Inspections
Schedule routine safety inspections, equipment checks, and calibration as part of the lab’s activities. This will ensure that the lab is compliant with regulatory standards and that equipment is in good working condition.
Example Safety Inspection:
- Week 2: Safety audit and inspection of fire safety equipment.
- Week 3: Calibration of chemical fume hoods and ventilation systems.
5. Communicate the Schedule to All Stakeholders
a) Share the Schedule with Team Members
Once the schedule is finalized, share it with all relevant stakeholders:
- Internal Teams: Researchers, technicians, safety officers, and any other team members involved in laboratory activities.
- Management: Provide an overview to senior management so they are aware of key activities, milestones, and any resource needs.
- External Partners or Clients: If any external stakeholders are involved in lab activities, such as testing or research collaborations, share the schedule and ensure they are aware of any required materials or timeframes.
b) Set Up a Communication Plan
For any changes or emergencies, establish a clear communication plan. Use tools like email, messaging platforms (Slack, Microsoft Teams), or project management tools to keep everyone updated.
6. Monitor and Adjust as Needed
a) Track Progress and Adjust the Schedule
- Daily Monitoring: Keep track of how activities are progressing. Are tasks being completed on time? Is any equipment malfunctioning or delayed? Are there supply shortages?
- Adjust the Schedule: If issues arise, adjust the schedule accordingly. This might involve re-prioritizing tasks, moving resources, or rescheduling activities.
b) Collect Feedback and Improve
After the month’s activities are completed, gather feedback from the teams involved:
- What went well?
- Were there any bottlenecks or challenges?
- What can be improved for next month?
Use this feedback to improve the scheduling and resource management process for future months.
Conclusion
By following these detailed steps, SayPro can ensure that its laboratory activities for the month are well-planned, efficient, and fully resourced. Creating a structured schedule and ensuring that all necessary materials and equipment are available will help avoid delays, ensure safety and compliance, and ultimately contribute to the success of the laboratory’s objectives. Regular monitoring and feedback will also allow for continuous improvements in how laboratory operations are managed.
Leave a Reply