Your cart is currently empty!
SayPro Examples of past work
SayPro is a Global Solutions Provider working with Individuals, Governments, Corporate Businesses, Municipalities, International Institutions. SayPro works across various Industries, Sectors providing wide range of solutions.
Email: info@saypro.online Call/WhatsApp: Use Chat Button ๐
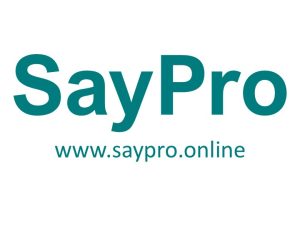
When establishing or promoting a SayPro repair service business, showcasing examples of past work is crucial for building credibility and trust with potential clients. Past experience in repair services and maintenance, particularly for industrial machinery like SayPro products, demonstrates expertise and proficiency in handling complex machinery. Here are a few examples of past work that could be included in a portfolio or presented to stakeholders, clients, or potential partners:
1. Large-Scale Manufacturing Plant Machinery Overhaul
- Client: A major manufacturing plant that operates heavy machinery from SayPro for production lines.
- Scope of Work:
- Diagnosis and repair of multiple SayPro hydraulic systems that were malfunctioning due to wear and tear.
- Maintenance of motor-driven equipment, including replacing damaged bearings and recalibrating control systems.
- Preventive maintenance plan was established to ensure the machinery ran at optimal efficiency, minimizing unexpected downtimes.
- Outcome:
- Reduced production downtime by 40%.
- Improved equipment efficiency, resulting in a 25% reduction in energy consumption.
2. Emergency Repair for Construction Equipment
- Client: A construction company that relies on SayPro machinery (e.g., bulldozers, excavators).
- Scope of Work:
- A major breakdown occurred during a critical construction project due to a hydraulic pump failure in a SayPro bulldozer.
- The repair team conducted an emergency on-site repair service, replacing the faulty pump and performing tests to ensure proper functioning.
- Provided a full inspection of the remaining equipment to ensure no other issues existed.
- Outcome:
- The bulldozer was back in operation within 48 hours, minimizing project delays.
- The company was able to avoid significant penalties and costs due to downtime, completing the project on time.
3. Scheduled Maintenance for Agricultural Machinery
- Client: An agricultural business using SayPro tractors and harvesters for field operations.
- Scope of Work:
- Routine servicing and maintenance of SayPro harvesters and tractors, including:
- Oil changes and replacement of air filters
- Diagnostic checks on engine performance
- Calibration of harvesters to optimize fuel efficiency and output
- Replacement of worn-out tires and belts
- Routine servicing and maintenance of SayPro harvesters and tractors, including:
- Outcome:
- Enhanced the operational lifespan of the machinery by 30%.
- Improved fuel efficiency, saving the client approximately 15% in fuel costs annually.
- Provided the client with a detailed maintenance log to track future service needs.
4. Industrial Machine Diagnostic and Repair Services
- Client: A warehouse that uses SayPro automated material handling systems.
- Scope of Work:
- Diagnostic services were provided for a malfunctioning automated conveyor system that halted the flow of goods.
- Repairs included replacing damaged motors, reprogramming control systems, and conducting alignment checks.
- Post-repair testing was carried out to ensure the conveyor system was running smoothly without interruptions.
- Outcome:
- The system was operational within 24 hours, reducing downtime and ensuring continued workflow.
- The warehouse experienced a 20% improvement in system efficiency after the repair.
5. Preventive Maintenance for Heavy Equipment in Mining Operations
- Client: A mining company that uses heavy-duty SayPro excavators and drilling equipment.
- Scope of Work:
- Routine inspection and maintenance of excavation and drilling equipment to ensure proper operation in harsh conditions.
- Replacement of key wear parts, including drill bits, hydraulic hoses, and pressure valves.
- Safety checks on exhaust systems and machinery parts vulnerable to corrosion.
- Outcome:
- Reduced equipment failure rates by 50% and minimized unscheduled downtime in the mine.
- Extended the equipmentโs operational life by 2 years through careful preventive measures and quality repairs.
6. On-Site Training for Client Maintenance Teams
- Client: A multinational company using SayPro CNC (Computer Numerical Control) machines in their production processes.
- Scope of Work:
- Training sessions were conducted to teach the clientโs maintenance team how to perform basic diagnostics and preventive maintenance on the CNC machines.
- Provided training on troubleshooting, software updates, and mechanical adjustments.
- Created maintenance manuals tailored to the clientโs machinery and operations.
- Outcome:
- Empowered the clientโs team to handle minor repairs and maintenance in-house, reducing reliance on external service providers.
- Reduced overall maintenance costs by 35% and improved machine uptime.
7. Overhaul of Industrial CNC Machining Center
- Client: A machining company using SayPro CNC machining centers for high-precision manufacturing.
- Scope of Work:
- Full overhaul of a CNC machining center, which included replacing key components such as the spindle, ball screws, and linear guides.
- Calibration of the CNC system to improve accuracy and reduce part scrap rates.
- Addressed software-related issues to ensure smoother integration with the factoryโs production schedule.
- Outcome:
- Improved machining accuracy by 15% and reduced production time for precision parts by 20%.
- The company reported fewer system errors and improved customer satisfaction with higher-quality products.
8. Replacement of Hydraulic Components in Large Excavator Fleet
- Client: A construction company using a fleet of SayPro hydraulic excavators on a major infrastructure project.
- Scope of Work:
- Replacement of hydraulic cylinders and pumps on several excavators.
- Implemented a fleet management system to track machinery health, monitor fluid levels, and schedule future service needs.
- Conducted extensive testing on all machinery after repairs to confirm operational readiness.
- Outcome:
- The fleet was back in operation within 72 hours, ensuring the project timeline was not impacted.
- The client reduced hydraulic system failures by 60% after regular use of the new management system.
9. Retrofitting Older Machines with New SayPro Parts
- Client: A regional construction firm with older SayPro machinery in their fleet.
- Scope of Work:
- Retrofitted older models with updated SayPro components, such as more efficient engines, improved safety features, and enhanced electronic control systems.
- Provided an upgrade to the hydraulic system to improve lifting capacity and fuel efficiency.
- Outcome:
- Increased equipment lifespan by up to 10 years with modernized parts and systems.
- The machineryโs operational performance was upgraded by 20%, leading to increased project efficiency.
10. Integration of SayPro Parts and Equipment for Machine Optimization
- Client: A logistics company using SayPro pallet jacks and forklifts.
- Scope of Work:
- Optimization of forklift performance through SayPro-approved parts such as upgraded motors and steering systems.
- Conducted a series of repairs and modifications to improve lifting capacity and operational safety.
- Adjusted machinery to meet the specific needs of the logistics operations, ensuring the equipment was aligned with warehouse floor layout.
- Outcome:
- Enhanced machine efficiency and safety protocols, reducing the risk of workplace accidents.
- Improved overall warehouse throughput by 15%, resulting in better inventory handling.
Conclusion
These examples demonstrate the range of repair and maintenance services that a SayPro repair service business can offer. The diversity of industries, from construction and agriculture to manufacturing and logistics, highlights the potential to serve multiple market segments. By showcasing these past examples, a repair service business can establish its credibility, attracting new clients and partnerships while reinforcing its commitment to high-quality service, technical expertise, and customer satisfaction.
Leave a Reply