Your cart is currently empty!
SayPro Safety, Compliance, and Technical Expertise in Repair Service Operations
SayPro is a Global Solutions Provider working with Individuals, Governments, Corporate Businesses, Municipalities, International Institutions. SayPro works across various Industries, Sectors providing wide range of solutions.
Email: info@saypro.online Call/WhatsApp: Use Chat Button 👇
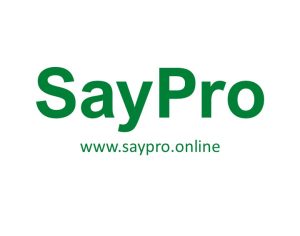
SayPro: Safety, Compliance, and Technical Expertise in Repair Service Operations
In any repair service business, especially one focused on specialized machinery like SayPro equipment, safety, compliance, and technical expertise are paramount. These factors not only ensure that repairs are done correctly but also protect both your employees and customers. Adhering to safety standards, complying with legal regulations, and maintaining a high level of technical proficiency are essential for building trust, maintaining high-quality service, and ensuring long-term success. This section will explore best practices for managing safety, compliance, and technical expertise in your SayPro repair service operations.
1. Ensuring Safety in Repair Operations
Safety should be a top priority in all aspects of your repair service business, especially when handling industrial machinery like SayPro’s products. Implementing strict safety protocols and ensuring that your technicians are adequately trained will minimize accidents, injuries, and damage to equipment.
a) Safety Training and Certification
- Regular Safety Training: Provide ongoing safety training to all service technicians, including specific training on the risks associated with working on heavy machinery and SayPro products. This training should cover proper handling of tools, safe operating procedures, and emergency response protocols.
- Personal Protective Equipment (PPE): Ensure that technicians are equipped with the appropriate personal protective equipment, such as gloves, goggles, ear protection, and steel-toed boots, depending on the nature of the repair work. Regularly inspect PPE to ensure that it is in good condition.
- Emergency Protocols: Implement clear emergency procedures for various scenarios, including electrical shock, equipment malfunctions, or chemical exposure. Make sure all technicians are trained in these protocols and know how to respond swiftly and appropriately.
- On-Site Safety Inspections: Conduct regular safety inspections on worksites to identify potential hazards, such as faulty equipment, exposed wiring, or improper lifting techniques. A well-maintained work environment is critical to preventing accidents.
b) Risk Assessment
- Conducting Risk Assessments: Perform regular risk assessments on all repair jobs, especially for complex tasks involving high-powered machinery. Assess potential hazards, such as electrical risks, mechanical failure, or equipment instability, and take proactive measures to minimize risks.
- Job Safety Analysis (JSA): Before starting any repair job, conduct a Job Safety Analysis (JSA) for each specific task. This helps identify hazards specific to the repair work and ensures that safety measures are in place before work begins.
- Lockout/Tagout Procedures: Implement lockout/tagout (LOTO) procedures to ensure that equipment is properly de-energized and cannot be started accidentally during repairs. This is essential for preventing injuries related to unintended machine activation.
c) Vehicle and Equipment Safety
- Maintenance of Service Vehicles: Ensure that service vehicles, which are often used to transport tools and equipment to job sites, are regularly maintained and inspected for safety. Proper vehicle maintenance reduces the risk of accidents during travel.
- Equipment Safety: Regularly inspect and maintain repair tools and equipment to ensure they are functioning safely. Replace any faulty tools and ensure that all technicians are trained on how to properly operate the tools required for each specific repair.
2. Compliance with Industry Regulations and Standards
Compliance with legal and industry-specific regulations is essential for the legitimacy of your repair service business. Following established safety and operational standards protects your business from legal risks, helps maintain credibility, and ensures you meet the expectations of regulatory bodies.
a) Adhering to Local, State, and Federal Regulations
- Workplace Safety Regulations: Comply with workplace safety regulations set by organizations such as the Occupational Safety and Health Administration (OSHA) or the equivalent regulatory body in your country. Familiarize yourself with the specific regulations related to machinery repair, hazardous materials handling, and workplace safety to avoid legal issues.
- Environmental Compliance: Be mindful of environmental regulations, especially if repairs involve the disposal of chemicals, oils, or other hazardous materials. Ensure that you follow proper procedures for waste disposal, recycling, and air quality management.
- Licensing and Certification: Obtain and maintain any necessary licenses or certifications required for operating a repair service business. This could include certifications from industry bodies or local government authorities. Working with certified technicians also adds credibility to your services.
- Insurance Requirements: Ensure that your business has adequate liability insurance to cover potential damage to customer equipment, injury to employees, or other unforeseen accidents. Insurance protects your business from financial losses and is often a requirement for compliance in many jurisdictions.
b) Health and Safety Standards for Machinery Repair
- Manufacturer-Specific Guidelines: Follow the safety and maintenance guidelines provided by the manufacturer, in this case, SayPro, for their equipment. This ensures that repairs are done in a manner that complies with industry standards and doesn’t void warranties or introduce unnecessary risks.
- Tool and Equipment Certification: Ensure that the tools and machinery you use for repairs are properly certified and meet industry standards. Any equipment that does not meet safety standards could jeopardize the repair job and expose your business to liability.
c) Industry Certifications and Best Practices
- ISO Certifications: If applicable, aim to achieve ISO (International Organization for Standardization) certifications related to your repair processes, such as ISO 9001 for quality management or ISO 45001 for occupational health and safety. These certifications serve as an industry-recognized mark of compliance and quality.
- Best Practices in Repair: Establish repair processes that align with recognized industry standards and best practices. By adhering to proven methods, your service team will not only ensure compliance but also improve the quality and consistency of repairs.
3. Maintaining Technical Expertise
Technical expertise is at the heart of a successful machinery repair business. For a SayPro-focused repair service, maintaining and continuously improving technical knowledge ensures that you can deliver precise and high-quality repairs, as well as adapt to evolving technologies.
a) Specialized Training on SayPro Machinery
- SayPro Product Training: Ensure that your technicians are trained extensively on SayPro’s machinery, including understanding the latest products, troubleshooting techniques, and maintenance requirements for each model. Regularly update your team’s skills as new products and technologies emerge from SayPro.
- Advanced Technical Courses: Offer specialized training programs for advanced repair techniques, including diagnostic methods, troubleshooting methods, and understanding the electronics and software involved in SayPro equipment. This level of training ensures that your technicians can handle the most complex repairs.
- On-the-Job Mentoring: Encourage experienced technicians to mentor newer team members. Peer-to-peer mentoring ensures that knowledge is passed on within the team, and it also helps develop a culture of continuous learning.
b) Staying Updated with Technological Advancements
- Research and Development: Keep abreast of technological advancements in machinery and repair techniques. Stay informed about upgrades, software updates, and new tools introduced by SayPro. Being proactive about learning the latest industry innovations helps position your repair service as a leader in technical expertise.
- Collaboration with SayPro: Establish a strong relationship with SayPro to stay updated on their products, upcoming changes, and any technical information or updates they release. This partnership can also provide access to exclusive training sessions, tools, or diagnostic equipment.
- Subscriptions to Industry Publications: Encourage your technicians and business managers to subscribe to industry journals, newsletters, and online resources to stay informed about changes in machinery repair and maintenance practices.
c) Quality Control and Diagnostic Tools
- Advanced Diagnostic Tools: Invest in state-of-the-art diagnostic equipment and software designed specifically for SayPro products. These tools enable technicians to quickly identify and resolve issues, reducing downtime and improving the accuracy of repairs.
- Regular Testing and Calibration: Ensure that all diagnostic tools and equipment are regularly tested and calibrated. Inaccurate tools can lead to misdiagnoses and subpar repairs, which undermine customer trust and damage your reputation.
- Repair Process Documentation: Document the repair processes for various SayPro machinery models, ensuring that each technician follows the best practices and standard procedures. Standardizing the repair process helps ensure that quality and accuracy are maintained across all service calls.
4. Ensuring Customer Satisfaction and Compliance
Customer satisfaction is directly linked to your ability to maintain high safety standards, adhere to legal regulations, and deliver repairs with technical excellence. By prioritizing customer needs and complying with industry regulations, you will foster trust and loyalty among your client base.
a) Clear Communication with Customers
- Transparent Repair Estimates: Before commencing any repair work, provide clear and detailed repair estimates to your customers, including labor, parts, and time requirements. This transparency builds trust and ensures that customers are not surprised by hidden fees.
- Detailed Reports: After repairs are completed, provide customers with detailed service reports that outline the work performed, the parts replaced, and any follow-up steps required. This documentation can serve as a valuable reference for future maintenance needs.
b) Compliance with Warranty and Service Agreements
- Honor Warranties: Ensure that all repairs made on SayPro machinery are covered by appropriate warranties and comply with any existing service agreements. Failure to honor warranties could result in customer dissatisfaction or legal disputes.
- Post-Service Support: Offer post-service support for any issues that may arise after repairs. This demonstrates your commitment to providing long-term service quality and helps establish a strong, ongoing relationship with your clients.
Conclusion
In the repair service industry, particularly when working with complex machinery like SayPro products, maintaining safety, compliance, and technical expertise is crucial for delivering high-quality services and ensuring the satisfaction of your customers. By implementing strict safety protocols, adhering to industry regulations, and continuously developing technical skills, your repair service business will not only operate efficiently but also build a reputation as a reliable and professional provider. This commitment to excellence will help you stand out in a competitive market and foster long-term business growth.
Leave a Reply